Flammability
Teledyne Gas & Flame Detection (Teledyne GFD) is making its final preparations for a trio of forthcoming energy sector events taking place in Europe and Asia. Visitors to the Teledyne GFD booth at All Energy 2025 (Glasgow, UK, 14-15 May), World Hydrogen Summit 2025 (Rotterdam, Netherlands, 20-22 May) and World Gas Congress 2025 (Beijing, China, 19-23 May) will learn for themselves the advantages of tapping into sector knowledge and solutions that stem from deca...
The HVAC/R industry is in the process of a major shift as A2L refrigerants become the standard in residential and commercial system HVAC. This change is being propelled by stricter environmental policy and advancements in refrigeration technology. However, the transition is not without its hurdles, posing new considerations for system owners, technicians, and equipment manufacturers. Favor of GWP alternatives The Environmental Protection Agency (EPA) has established clear guidelines to phase...
A-Gas, a world pioneer in environmentally responsible lifecycle refrigerant and fire suppressant management, acquired Refrigerant Services Inc. (RSI), a recognized brand in the Canadian refrigerant industry. The acquisition, finalized in late March 2025, further solidifies A-Gas' position as a world pioneer in the supply and lifecycle management of refrigerants and associated products and services. Strengthening Commitment It ensures that customers receive the maximum value and benefit of lif...
Anacove, the pioneering developer of AI-enabled, cloud-connected energy management solutions for the hotel industry, announced the formal market introduction of its Anacove Smart Thermostat as part of a complete line of energy management solutions that also include Anacove Staff Safety Alerts, Toilet Leak Detectors, and Asset Tracking Services. In tests with pioneering hotels for the last two years, including IHG Hotels, who have designated Anacove a preferred vendor, Anacove Smart Thermostats...
ACE Chemical, a pioneering developer and manufacturer of chemical treatments for the HVAC/R industry, announced the launch of the new American-made Monster® Series of coil cleaners, leak sealant, and accessories for HVAC/R pros. Formulated for professional use to conquer even the most challenging dirt and grease but remain gentle on hands and surfaces, the Monster® Series is an instant coil-cleaning legend for condensers, evaporators, walk-in coolers, ventilators, and refri...
Steam systems serve as the backbone of numerous industrial processes, providing the essential thermal energy required for a wide range of applications across various sectors. From powering machinery in manufacturing facilities to sterilizing equipment in healthcare settings, the importance of steam cannot be overstated. Improving Steam Operations American Plant Maintenance (APM Steam) offers specialized services aimed at optimizing steam systemsDespite their critical role, steam systems often...
News
Energy efficiency and sustainability are currently the most pressing priorities on the European and global HVAC/R market. At ISH 2025, CAREL will be presenting solutions for heat generation and indoor air quality. Adopting advanced technologies helps optimize system performance, reduce energy consumption and simplify management, while ensuring the highest reliability and compliance with the latest regulations. Efficiency and sustainability in heat generation CAREL offers a full ecosystem of technologies for air/water and water/water heat pumps Heat pumps are a key solution for the decarbonization of buildings, reducing CO2 emissions due to their high energy efficiency. CAREL offers a complete ecosystem of technologies for air/water and water/water heat pumps, including outdoor, indoor, and all-in-one units. Through the addition of inverters, variable-speed compressors, and electronic expansion valves, these units can adapt their operation dynamically based on actual conditions, optimizing energy consumption and performance. CAREL’s advanced software The c.pCO sistema programmable controllers have the task of managing the units, guaranteeing maximum flexibility and integration between system components. As further support, CAREL’s advanced software ensures optimized management of the refrigeration cycle, with upgraded and improved algorithms such as defrost management, low-load compressor operation, and revised alarm mapping. This software is either ready-to-use or can be easily customized using existing function blocks. New Stone Virtual Loop tool The products available are A3 ready and ATEX-certified, designed to ensure safety and faster unit The products available are A3 ready and ATEX-certified, designed to ensure safety and faster unit certification in applications where flammable refrigerants such as propane are used. Finally, the new Stone Virtual Loop tool can be used to simulate and test the thermodynamic behavior of units while they are still under development, improving design and reducing validation times in the field. Digital innovation: Virtual Loop and pYC mini Innovation is at the heart of CAREL’s proposal at ISH 2025, with two key innovations: Stone Virtual Loop and pYC mini. Virtual Loop is CAREL’s simulator that, using digital twin technology, replicates the behavior of actual thermodynamic units in a virtual environment. Integrating seamlessly into the STone ecosystem, this tool revolutionizes the design and testing of units such as heat pumps, chillers, and rooftops, allowing developers to test and optimize the implemented control logic in real time. By eliminating the need for physical prototypes and complex infrastructure, it makes development much faster and significantly less costly, ensuring both high efficiency and reliability of the end product. pYC mini is the new line of programmable controllers designed to meet the growing demand for efficiency, safety, and versatility in HVAC/R applications. With a compact structure and the flexibility offered by programmability, pYC mini also complies with the latest regulations on low GWP refrigerants, including flammable gases (A3, A2L). Serial communication, available as standard, is used to directly manage the main actuators on the unit, such as electronic expansion valves, fan speed controllers, and compressor inverters, thus optimizing control and energy efficiency. Wireless connectivity enables quick and intuitive setup using the APPLICA app, simplifying installation and monitoring. Finally, integration with supervisory systems is also available, for constant monitoring and detailed performance analysis. Indoor air quality and energy recovery In commercial buildings, the design and efficiency of ventilation systems is essential to ensure healthy, energy-efficient spaces. CAREL develops advanced solutions for energy recovery in air handling units, managed by the k.Air family parametric controllers, covering a wide range of possible system layouts and reducing both times and costs, from design to commissioning. The thermal wheels for sensible and latent heat recovery ensure both hygiene and no contamination between the different air streams. Optimal management of air flows in AHUs When combined with reverse-cycle heat pumps fitted with inverters and electronic expansion valves When combined with reverse-cycle heat pumps equipped with inverters and electronic expansion valves, part load operation is possible, to reduce energy consumption. Furthermore, continuous indoor air quality monitoring via advanced temperature, humidity, and CO2 sensors allows precise control of air quality parameters. The offering is completed by adiabatic and isothermal humidifiers that keep relative humidity within a suitable range, as well as dampers for optimal management of air flows in AHUs, improving overall system effectiveness. IAQ: a speech on how to combine comfort and health Alexander Willesch, CAREL Sales Manager Ventilation in the D-A-CH-NL area, will give a speech entitled “Indoor air quality: how to combine comfort and health for occupants of buildings”. The presentation will take place on 18 March, from 11:00 to 11:25 in Hall 12, Level 1, E03, in German. It will focus on the importance of ventilation systems and CO2 monitoring in ensuring indoor air quality, as outlined in the European legislation.
The spotlight on refrigerant leak detection, monitoring, and reporting has never been brighter as the HVAC and refrigeration (HVAC-R) industry navigates regulatory changes in their market. To help HVAC-R businesses address these changes, MSA Safety, Inc. will be showcasing its leak detection and monitoring management solution capabilities at next week’s AHR Expo in Orlando, Florida, February 10th through 12th. latest trends and topics MSA Safety is featuring its comprehensive solution of ALD systems and FieldServer Protocol Gateways As one of the largest HVAC-R events, the AHR Expo connects industry pioneers and experts with more than 50,000 professionals to discuss the latest trends and topics, while showcasing pioneering solutions and technologies. This year, MSA Safety is featuring its comprehensive solution of Automatic Leak Detection (ALD) systems, Parasense Refrigerant Tracking & Compliance Software, and FieldServer Protocol Gateways. Combined solution of ALD systems AHR Expo attendees can learn more about how this combined solution of ALD systems and Parasense software can help users address their own compliance needs, save money, and provide actionable data to help achieve better leak detection management outcomes. Show visitors will also learn how FieldServer Gateway devices help users easily and securely connect with their detection devices to improve efficiency with products, processes, and production. monitoring and reporting software AHR Expo attendees can learn more about how this combined solution of ALD systems “With MSA Safety’s expertise in automatic leak detection, combined with our monitoring and reporting software, we can help customers explore solutions that may be best for them on their compliance journeys and deliver on their sustainability goals,” said Rob Senko, MSA Safety Global Business Pioneer for HVAC-R. “Our innovative, turnkey solution that includes hardware, software, and service is capable of detecting refrigerant leaks at the lowest levels, ultimately helping to reduce leaks more quickly and proactively. This not only helps customers drive better sustainability behaviors and practices, but also helps deliver real bottom-line impact, supporting our mission of safety by helping to safeguard people, places and our planet.” MSA Safety’s featured ALD solutions MSA Safety’s featured ALD solutions include the MSA Bacharach® Multi-Zone Gas Monitor, and MSA Chillgard® 5000 Refrigerant Leak Monitor. Both are aspirated detection systems, meaning they pull air from strategically placed sample points into the unit, where sensors measure the concentration of refrigerant in the air and trigger alerts if a leak is detected. Parasense Refrigerant Tracking & Compliance Software Both systems are capable of monitoring up to 16-zones for more than 60 different refrigerants Both systems are capable of monitoring up to 16-zones for more than 60 different refrigerants and are capable of detecting leaks as low as 1 ppm – considered very early detection for the average leak rate. With an increased industry focus on tracking refrigerant usage and regulatory compliance, MSA Safety is showcasing its Parasense Refrigerant Tracking & Compliance Software. This cloud-based software offers refrigerant management and tracking tools designed to help users reduce operating costs, understand and address their own compliance needs, and achieve sustainability and efficiency goals. Different HVAC-R products and network protocols AHR Expo attendees can learn more about MSA’s suite of FieldServer Protocol Gateways and how they can help customers with building automation and controls, refrigerant leak detection, and data management. These Industrial Internet of Things (IIoT) gateways are secure, easy-to-configure devices that serve as entry points for data communication and processing between different HVAC-R products and network protocols to the cloud. Latest AHR Expo 2025 FieldServer Gateways are connectivity solutions supporting more than 140 protocols, including Modbus, BACnet, LonWorks, and KNX. These solutions, expert personnel and more will be featured at MSA Safety’s Booth #1361 in the Orange County Convention Center West Building. Keep up to date with the latest AHR Expo happenings by visiting the MSA’s AHR Expo website and following MSA’s social media platforms.
Carrier has launched a new line of K-Series WeatherMaker® Applied rooftop units available with more environmentally sustainable R-454B refrigerant, known commercially as Puron Advance. Carrier is a part of Carrier Global Corporation, pioneer in intelligent climate and energy solutions. The K-series is available in 20-to-60-ton nominal cooling capacities and features a robust indoor fan system and improved design for higher efficiency compared to legacy Carrier models. Variable Air Volume configurations The K-Series, which includes the 48K with gas heating and electric cooling and the 50K with electric cooling with optional electric or hydronic heat, has a commercial-grade cabinet with fully hinged access panels, designed to fit most legacy Carrier curbs. The K-Series has a high-capacity forward curve indoor fan with variable frequency drive control and available Staged Air Volume or Variable Air Volume configurations to meet a wide range of application requirements. Humidi-MiZer® dehumidification Other parts Carrier SmartVu™ controls with a 7-inch touchscreen display, a refrigerant leak detection system Other features include Carrier SmartVu™ controls with a 7-inch touchscreen display, a refrigerant leak detection system with dissipation control, and a variety of factory-installed options, including an ultra-low leak economizer, modulating gas or electric heat, Humidi-MiZer® dehumidification and double wall construction with available Agion® anti-microbial coating. “Carrier’s K-Series rooftop units are the latest in a long line of flexible, efficient and reliable solutions for commercial air conditioning and indoor air quality needs,” said Michael Jones, Product Manager, Applied Packaged Systems, Carrier. EPA’s lower GWP requirements Jones added: “We’re helping our customers prepare to meet regulatory requirements while also designing our products to be efficient and innovative, all while offering easy installation and compatibility with existing curbs.” The adoption of Puron Advance surpasses the EPA’s lower GWP requirements for 2025. R-454B has a GWP100 of 466 according to the Intergovernmental Panel on Climate Change Fourth Assessment Report — a 75% reduction from R-410A — and non-ozone depleting potential, the refrigerant was selected as one of the best solutions to minimize environmental impact and provide longevity-based on the United Nations Montreal Protocol Kigali Agreement phasedown plan. GWP is a measure of a substance’s climate warming impact compared to CO2.
A-Gas, a world pioneer in environmentally responsible lifecycle refrigerant management, is excited to announce its participation in the HVAC Excellence Conference 2025, taking place March 16-19 in Las Vegas, Nevada. Attendees are invited to join an engaging session focused on equipping HVAC professionals with essential knowledge for navigating key industry changes. Regulatory Insights for HVAC The session will be about common myths of refrigerant reclamation and supplyAt the event, A-Gas will present an educational session exploring the AIM Act and sustainable refrigerant supply strategies. The session will tackle common myths about refrigerant reclamation and supply and offer a regulatory overview to help professionals adapt to the evolving HVAC landscape. Future-Ready Compliance Strategies Attendees will leave with actionable insights on ensuring compliance and implementing effective refrigerant management practices that will serve their businesses now and in the future. Optimizing Refrigerant Recovery “This conference provides a unique opportunity for HVAC professionals and educators to learn more about the challenges and opportunities in lifecycle refrigerant management,” said Anthony Nash, A-Gas Rapid Recovery Network Training Manager, who is presenting at the conference. “We look forward to connecting with attendees and sharing solutions that promote compliance, efficiency, and environmental responsibility, all while supporting the great content HVAC Excellence provides.” Environmental Commitment in HVAC A-Gas is committed to helping the HVAC industry transition to sustainable solutions while addressing environmental and regulatory challenges. By offering innovative lifecycle refrigerant management services, A-Gas continues to lead the way in supporting a circular economy.
Carrier has launched a new line of V-Series WeatherMaster® Applied rooftop units available with more environmentally sustainable R-454B refrigerant, known commercially as Puron Advance. Carrier is a part of Carrier Global Corporation, pioneer in intelligent climate and energy solutions. The V-Series, which includes the 48V with gas heating and electric cooling and the 50V with electric cooling with optional electric or hydronic heat, can integrate with both legacy curbs and select competitor models in replacement or retrofit applications. Carrier SmartVu™ controls Carrier SmartVu™ controls with a 7-inch touchscreen display, a refrigerant leak detection system The series is available in 27.5 to 100 ton nominal cooling capacities and features a direct drive indoor fan array with electronically commuted motors, a standard capacity variable speed scroll compressor, Carrier SmartVu™ controls with a 7-inch touchscreen display, a refrigerant leak detection system with dissipation control, and a variety of factory installed options, including modulating gas or electric heat, and Humidi-MiZer® dehumidification. The series also offers selectable configurations for staged air volume in single-zone applications, as well as variable air volume options suitable for both single-zone and multi-zone applications. Carrier V-Series rooftop units “The Carrier V-Series rooftop units are designed to provide customers with a flexible, efficient and reliable solution for their air conditioning and indoor air quality needs, while also offering easy installation and compatibility with existing curbs,” said Michael Jones, Product Manager, Applied Packaged Systems, Carrier. “And by adopting R-454B, we’re helping our customers prepare to meet regulatory requirements while also designing our products to be efficient and innovative. Puron Advance shows our commitment to going beyond the minimum, surpassing the EPA’s lower GWP requirements for 2025.” Reduction from R-410A R-454B has a GWP100 of 466 according to the Intergovernmental Panel on Climate Change Fourth Assessment Report — a 75% reduction from R-410A — and non-ozone depleting potential, the refrigerant was selected as one of the best solutions to minimize environmental impact and provide longevity based on the United Nations Montreal Protocol Kigali Agreement phasedown plan. GWP is a measure of a substance’s climate warming impact compared to CO2.
A-Gas, a pioneer in environmentally responsible lifecycle refrigerant management (LRM), is thrilled to announce its recognition as a recipient of the Ohio Environmental Protection Agency’s (Ohio EPA) Encouraging Environmental Excellence (E3) Silver Award for 2024. This esteemed accolade reflects A-Gas’ unwavering commitment to environmental stewardship, sustainability, and reducing its environmental impact, while conserving vital natural resources. Elevating Environmental Standards A-Gas has been honored with the Silver Award for its exceptional contributions to sustainability The Ohio EPA’s E3 program highlights organizations that go above and beyond regulatory requirements to implement meaningful environmental practices. A-Gas has been honored with the Silver Award for its exceptional contributions to sustainability, which include pioneering efforts in LRM — a closed-loop approach to refrigerant use that focuses on recovery, reclamation, and reuse (or safe destruction). By prioritizing the safe handling and proper lifecycle management of refrigerants, A-Gas not only reduces the potential for harmful greenhouse gas emissions, but also supports industries in meeting environmental compliance and sustainability goals. “This award is a testament to our team’s hard work and steadfast dedication to building a sustainable future,” said Tammy Myers, Environmental, Health, and Safety Manager, A-Gas’ Bowling Green, Ohio facility. Sustainability Through Refrigerant Management Tammy Myers adds, “At A-Gas, environmental responsibility is central to our mission. We are proud to champion circular business practices that ensure critical resources stay in use, reducing the need to produce virgin refrigerants and further contribute to global warming.” A-Gas’ recognition by the Ohio EPA reaffirms its position as a global pioneer in LRM, showcasing how innovative approaches to environmental responsibility can support the industry. By leveraging its expertise, A-Gas continues to contribute meaningful change, helping businesses align with long-term economic and ecological objectives.
Energy efficiency and sustainability are currently the most pressing priorities on the European and global HVAC/R market. At ISH 2025, CAREL will be presenting solutions for heat generation and indoor air quality. Adopting advanced technologies helps optimize system performance, reduce energy consumption and simplify management, while ensuring the highest reliability and compliance with the latest regulations. Efficiency and sustainability in heat generation CAREL offers a full ecosystem of technologies for air/water and water/water heat pumps Heat pumps are a key solution for the decarbonization of buildings, reducing CO2 emissions due to their high energy efficiency. CAREL offers a complete ecosystem of technologies for air/water and water/water heat pumps, including outdoor, indoor, and all-in-one units. Through the addition of inverters, variable-speed compressors, and electronic expansion valves, these units can adapt their operation dynamically based on actual conditions, optimizing energy consumption and performance. CAREL’s advanced software The c.pCO sistema programmable controllers have the task of managing the units, guaranteeing maximum flexibility and integration between system components. As further support, CAREL’s advanced software ensures optimized management of the refrigeration cycle, with upgraded and improved algorithms such as defrost management, low-load compressor operation, and revised alarm mapping. This software is either ready-to-use or can be easily customized using existing function blocks. New Stone Virtual Loop tool The products available are A3 ready and ATEX-certified, designed to ensure safety and faster unit The products available are A3 ready and ATEX-certified, designed to ensure safety and faster unit certification in applications where flammable refrigerants such as propane are used. Finally, the new Stone Virtual Loop tool can be used to simulate and test the thermodynamic behavior of units while they are still under development, improving design and reducing validation times in the field. Digital innovation: Virtual Loop and pYC mini Innovation is at the heart of CAREL’s proposal at ISH 2025, with two key innovations: Stone Virtual Loop and pYC mini. Virtual Loop is CAREL’s simulator that, using digital twin technology, replicates the behavior of actual thermodynamic units in a virtual environment. Integrating seamlessly into the STone ecosystem, this tool revolutionizes the design and testing of units such as heat pumps, chillers, and rooftops, allowing developers to test and optimize the implemented control logic in real time. By eliminating the need for physical prototypes and complex infrastructure, it makes development much faster and significantly less costly, ensuring both high efficiency and reliability of the end product. pYC mini is the new line of programmable controllers designed to meet the growing demand for efficiency, safety, and versatility in HVAC/R applications. With a compact structure and the flexibility offered by programmability, pYC mini also complies with the latest regulations on low GWP refrigerants, including flammable gases (A3, A2L). Serial communication, available as standard, is used to directly manage the main actuators on the unit, such as electronic expansion valves, fan speed controllers, and compressor inverters, thus optimizing control and energy efficiency. Wireless connectivity enables quick and intuitive setup using the APPLICA app, simplifying installation and monitoring. Finally, integration with supervisory systems is also available, for constant monitoring and detailed performance analysis. Indoor air quality and energy recovery In commercial buildings, the design and efficiency of ventilation systems is essential to ensure healthy, energy-efficient spaces. CAREL develops advanced solutions for energy recovery in air handling units, managed by the k.Air family parametric controllers, covering a wide range of possible system layouts and reducing both times and costs, from design to commissioning. The thermal wheels for sensible and latent heat recovery ensure both hygiene and no contamination between the different air streams. Optimal management of air flows in AHUs When combined with reverse-cycle heat pumps fitted with inverters and electronic expansion valves When combined with reverse-cycle heat pumps equipped with inverters and electronic expansion valves, part load operation is possible, to reduce energy consumption. Furthermore, continuous indoor air quality monitoring via advanced temperature, humidity, and CO2 sensors allows precise control of air quality parameters. The offering is completed by adiabatic and isothermal humidifiers that keep relative humidity within a suitable range, as well as dampers for optimal management of air flows in AHUs, improving overall system effectiveness. IAQ: a speech on how to combine comfort and health Alexander Willesch, CAREL Sales Manager Ventilation in the D-A-CH-NL area, will give a speech entitled “Indoor air quality: how to combine comfort and health for occupants of buildings”. The presentation will take place on 18 March, from 11:00 to 11:25 in Hall 12, Level 1, E03, in German. It will focus on the importance of ventilation systems and CO2 monitoring in ensuring indoor air quality, as outlined in the European legislation.
The spotlight on refrigerant leak detection, monitoring, and reporting has never been brighter as the HVAC and refrigeration (HVAC-R) industry navigates regulatory changes in their market. To help HVAC-R businesses address these changes, MSA Safety, Inc. will be showcasing its leak detection and monitoring management solution capabilities at next week’s AHR Expo in Orlando, Florida, February 10th through 12th. latest trends and topics MSA Safety is featuring its comprehensive solution of ALD systems and FieldServer Protocol Gateways As one of the largest HVAC-R events, the AHR Expo connects industry pioneers and experts with more than 50,000 professionals to discuss the latest trends and topics, while showcasing pioneering solutions and technologies. This year, MSA Safety is featuring its comprehensive solution of Automatic Leak Detection (ALD) systems, Parasense Refrigerant Tracking & Compliance Software, and FieldServer Protocol Gateways. Combined solution of ALD systems AHR Expo attendees can learn more about how this combined solution of ALD systems and Parasense software can help users address their own compliance needs, save money, and provide actionable data to help achieve better leak detection management outcomes. Show visitors will also learn how FieldServer Gateway devices help users easily and securely connect with their detection devices to improve efficiency with products, processes, and production. monitoring and reporting software AHR Expo attendees can learn more about how this combined solution of ALD systems “With MSA Safety’s expertise in automatic leak detection, combined with our monitoring and reporting software, we can help customers explore solutions that may be best for them on their compliance journeys and deliver on their sustainability goals,” said Rob Senko, MSA Safety Global Business Pioneer for HVAC-R. “Our innovative, turnkey solution that includes hardware, software, and service is capable of detecting refrigerant leaks at the lowest levels, ultimately helping to reduce leaks more quickly and proactively. This not only helps customers drive better sustainability behaviors and practices, but also helps deliver real bottom-line impact, supporting our mission of safety by helping to safeguard people, places and our planet.” MSA Safety’s featured ALD solutions MSA Safety’s featured ALD solutions include the MSA Bacharach® Multi-Zone Gas Monitor, and MSA Chillgard® 5000 Refrigerant Leak Monitor. Both are aspirated detection systems, meaning they pull air from strategically placed sample points into the unit, where sensors measure the concentration of refrigerant in the air and trigger alerts if a leak is detected. Parasense Refrigerant Tracking & Compliance Software Both systems are capable of monitoring up to 16-zones for more than 60 different refrigerants Both systems are capable of monitoring up to 16-zones for more than 60 different refrigerants and are capable of detecting leaks as low as 1 ppm – considered very early detection for the average leak rate. With an increased industry focus on tracking refrigerant usage and regulatory compliance, MSA Safety is showcasing its Parasense Refrigerant Tracking & Compliance Software. This cloud-based software offers refrigerant management and tracking tools designed to help users reduce operating costs, understand and address their own compliance needs, and achieve sustainability and efficiency goals. Different HVAC-R products and network protocols AHR Expo attendees can learn more about MSA’s suite of FieldServer Protocol Gateways and how they can help customers with building automation and controls, refrigerant leak detection, and data management. These Industrial Internet of Things (IIoT) gateways are secure, easy-to-configure devices that serve as entry points for data communication and processing between different HVAC-R products and network protocols to the cloud. Latest AHR Expo 2025 FieldServer Gateways are connectivity solutions supporting more than 140 protocols, including Modbus, BACnet, LonWorks, and KNX. These solutions, expert personnel and more will be featured at MSA Safety’s Booth #1361 in the Orange County Convention Center West Building. Keep up to date with the latest AHR Expo happenings by visiting the MSA’s AHR Expo website and following MSA’s social media platforms.
Carrier has launched a new line of K-Series WeatherMaker® Applied rooftop units available with more environmentally sustainable R-454B refrigerant, known commercially as Puron Advance. Carrier is a part of Carrier Global Corporation, pioneer in intelligent climate and energy solutions. The K-series is available in 20-to-60-ton nominal cooling capacities and features a robust indoor fan system and improved design for higher efficiency compared to legacy Carrier models. Variable Air Volume configurations The K-Series, which includes the 48K with gas heating and electric cooling and the 50K with electric cooling with optional electric or hydronic heat, has a commercial-grade cabinet with fully hinged access panels, designed to fit most legacy Carrier curbs. The K-Series has a high-capacity forward curve indoor fan with variable frequency drive control and available Staged Air Volume or Variable Air Volume configurations to meet a wide range of application requirements. Humidi-MiZer® dehumidification Other parts Carrier SmartVu™ controls with a 7-inch touchscreen display, a refrigerant leak detection system Other features include Carrier SmartVu™ controls with a 7-inch touchscreen display, a refrigerant leak detection system with dissipation control, and a variety of factory-installed options, including an ultra-low leak economizer, modulating gas or electric heat, Humidi-MiZer® dehumidification and double wall construction with available Agion® anti-microbial coating. “Carrier’s K-Series rooftop units are the latest in a long line of flexible, efficient and reliable solutions for commercial air conditioning and indoor air quality needs,” said Michael Jones, Product Manager, Applied Packaged Systems, Carrier. EPA’s lower GWP requirements Jones added: “We’re helping our customers prepare to meet regulatory requirements while also designing our products to be efficient and innovative, all while offering easy installation and compatibility with existing curbs.” The adoption of Puron Advance surpasses the EPA’s lower GWP requirements for 2025. R-454B has a GWP100 of 466 according to the Intergovernmental Panel on Climate Change Fourth Assessment Report — a 75% reduction from R-410A — and non-ozone depleting potential, the refrigerant was selected as one of the best solutions to minimize environmental impact and provide longevity-based on the United Nations Montreal Protocol Kigali Agreement phasedown plan. GWP is a measure of a substance’s climate warming impact compared to CO2.
A-Gas, a world pioneer in environmentally responsible lifecycle refrigerant management, is excited to announce its participation in the HVAC Excellence Conference 2025, taking place March 16-19 in Las Vegas, Nevada. Attendees are invited to join an engaging session focused on equipping HVAC professionals with essential knowledge for navigating key industry changes. Regulatory Insights for HVAC The session will be about common myths of refrigerant reclamation and supplyAt the event, A-Gas will present an educational session exploring the AIM Act and sustainable refrigerant supply strategies. The session will tackle common myths about refrigerant reclamation and supply and offer a regulatory overview to help professionals adapt to the evolving HVAC landscape. Future-Ready Compliance Strategies Attendees will leave with actionable insights on ensuring compliance and implementing effective refrigerant management practices that will serve their businesses now and in the future. Optimizing Refrigerant Recovery “This conference provides a unique opportunity for HVAC professionals and educators to learn more about the challenges and opportunities in lifecycle refrigerant management,” said Anthony Nash, A-Gas Rapid Recovery Network Training Manager, who is presenting at the conference. “We look forward to connecting with attendees and sharing solutions that promote compliance, efficiency, and environmental responsibility, all while supporting the great content HVAC Excellence provides.” Environmental Commitment in HVAC A-Gas is committed to helping the HVAC industry transition to sustainable solutions while addressing environmental and regulatory challenges. By offering innovative lifecycle refrigerant management services, A-Gas continues to lead the way in supporting a circular economy.
Carrier has launched a new line of V-Series WeatherMaster® Applied rooftop units available with more environmentally sustainable R-454B refrigerant, known commercially as Puron Advance. Carrier is a part of Carrier Global Corporation, pioneer in intelligent climate and energy solutions. The V-Series, which includes the 48V with gas heating and electric cooling and the 50V with electric cooling with optional electric or hydronic heat, can integrate with both legacy curbs and select competitor models in replacement or retrofit applications. Carrier SmartVu™ controls Carrier SmartVu™ controls with a 7-inch touchscreen display, a refrigerant leak detection system The series is available in 27.5 to 100 ton nominal cooling capacities and features a direct drive indoor fan array with electronically commuted motors, a standard capacity variable speed scroll compressor, Carrier SmartVu™ controls with a 7-inch touchscreen display, a refrigerant leak detection system with dissipation control, and a variety of factory installed options, including modulating gas or electric heat, and Humidi-MiZer® dehumidification. The series also offers selectable configurations for staged air volume in single-zone applications, as well as variable air volume options suitable for both single-zone and multi-zone applications. Carrier V-Series rooftop units “The Carrier V-Series rooftop units are designed to provide customers with a flexible, efficient and reliable solution for their air conditioning and indoor air quality needs, while also offering easy installation and compatibility with existing curbs,” said Michael Jones, Product Manager, Applied Packaged Systems, Carrier. “And by adopting R-454B, we’re helping our customers prepare to meet regulatory requirements while also designing our products to be efficient and innovative. Puron Advance shows our commitment to going beyond the minimum, surpassing the EPA’s lower GWP requirements for 2025.” Reduction from R-410A R-454B has a GWP100 of 466 according to the Intergovernmental Panel on Climate Change Fourth Assessment Report — a 75% reduction from R-410A — and non-ozone depleting potential, the refrigerant was selected as one of the best solutions to minimize environmental impact and provide longevity based on the United Nations Montreal Protocol Kigali Agreement phasedown plan. GWP is a measure of a substance’s climate warming impact compared to CO2.
A-Gas, a pioneer in environmentally responsible lifecycle refrigerant management (LRM), is thrilled to announce its recognition as a recipient of the Ohio Environmental Protection Agency’s (Ohio EPA) Encouraging Environmental Excellence (E3) Silver Award for 2024. This esteemed accolade reflects A-Gas’ unwavering commitment to environmental stewardship, sustainability, and reducing its environmental impact, while conserving vital natural resources. Elevating Environmental Standards A-Gas has been honored with the Silver Award for its exceptional contributions to sustainability The Ohio EPA’s E3 program highlights organizations that go above and beyond regulatory requirements to implement meaningful environmental practices. A-Gas has been honored with the Silver Award for its exceptional contributions to sustainability, which include pioneering efforts in LRM — a closed-loop approach to refrigerant use that focuses on recovery, reclamation, and reuse (or safe destruction). By prioritizing the safe handling and proper lifecycle management of refrigerants, A-Gas not only reduces the potential for harmful greenhouse gas emissions, but also supports industries in meeting environmental compliance and sustainability goals. “This award is a testament to our team’s hard work and steadfast dedication to building a sustainable future,” said Tammy Myers, Environmental, Health, and Safety Manager, A-Gas’ Bowling Green, Ohio facility. Sustainability Through Refrigerant Management Tammy Myers adds, “At A-Gas, environmental responsibility is central to our mission. We are proud to champion circular business practices that ensure critical resources stay in use, reducing the need to produce virgin refrigerants and further contribute to global warming.” A-Gas’ recognition by the Ohio EPA reaffirms its position as a global pioneer in LRM, showcasing how innovative approaches to environmental responsibility can support the industry. By leveraging its expertise, A-Gas continues to contribute meaningful change, helping businesses align with long-term economic and ecological objectives.


Expert Commentary
It’s often said the only constant in life is change. In the HVACR industry, that phrase has been especially true. We saw another year of transitions in 2024 that included evolving efficiency and refrigerant regulations, changing corporate net zero targets, the continued emergence of advanced heat pumps, and the impact of artificial intelligence (AI) in building management. Smart and sustainable Throughout these transformations, the industry continues to overcome challenges and innovate as we transform the places where people live, work, and play into smarter, healthier, and more sustainable spaces. As we look toward 2025, we can expect to see a continued, industrywide focus on decarbonization, heat pump development, A2L refrigerants, and AI as regulations expand and new technologies emerge. Decarbonization Decarbonization continues to be a very high priority for both the residential and commercial sectors Decarbonization continues to be a very high priority for both the residential and commercial sectors. This focus has transformed the way we design and install HVAC equipment and has created tremendous opportunities for those who invest in educating themselves on the evolving technologies, regulations, and incentives. Today’s building professionals and homeowners have an unprecedented number of incentives available at the federal, state, and utility levels encouraging decarbonization transitions. Digital and net zero services For example, tax credits such as 25C for consumers and 179D for commercial building owners were expanded under the Inflation Reduction Act (IRA) and can significantly reduce the upfront costs of high-efficiency equipment, creating a compelling offer to replace less efficient systems. In commercial buildings, combining high-efficiency HVAC equipment like electric heat pumps with digital technologies and net zero services can help empower organizations to optimize their buildings and subsystems for both the short- and long-term. Heat pumps Heat pump technology has advanced significantly in recent years, providing an electrified, high-efficiency HVAC option for nearly all applications – even those operating within colder climates. The Department of Energy’s (DOE) Residential Cold Climate Heat Pump (CCHP) Technology Challenge has propelled the successful introduction of heat pump prototypes that can withstand subfreezing weather. Similarly, the DOE’s Commercial Building Rooftop Heat Pump Accelerator program has helped drive packaged heat pump performance toward greater efficiency for commercial and light commercial buildings located in colder climate zones. Water-to-water heat pumps Water-to-water heat pumps can replace legacy chiller and boiler combinations without the need for major changes Innovations in commercial water-to-water compound centrifugal heat pumps are also accelerating decarbonization within building retrofits. For facilities that require simultaneous heating and cooling, such as hospitals and universities, water-to-water heat pumps can replace legacy chiller and boiler combinations without the need for major changes to the existing HVAC infrastructure. This partial decarbonization approach can help building operators achieve their decarbonization goals while also lowering operational expenses (OpEx). In many instances, this reduction in OpEx also provides a path to funding additional decarbonization strategies. A2L refrigerants The EPA continues to make strides in reducing the consumption and production of hydrofluorocarbons (HFCs) under the American Innovation and Manufacturing (AIM) Act. As part of the AIM Act, the Technology Transitions Program will usher in sector-based regulations beginning January 1, 2025, prohibiting the manufacturing of equipment using refrigerants with a GWP higher than 700. New protocols As a result, new equipment will continue to hit the market throughout 2025. In tandem, many contractors and technicians will begin working with A2L refrigerants for the first time. Because these refrigerants are classified by ASHRAE as mildly flammable, new protocols for safe refrigerant servicing, storage, and transportation, and refrigerant leak detection (RDS) requirements will be necessary for some applications. ACCA A2L refrigerant training Contractors should complete ACCA A2L refrigerant training and EPA section 608 certification With these changes, it is important to become familiar with updated codes, including UL 60335-2-40, 3rd and 4th editions, ASHRAE 15 and 15.,2, and the AHRI Safe Refrigerant Transition Task Force (SRTTF), as well as local and state regulations. Contractors should also complete ACCA A2L refrigerant training and EPA section 608 certification. Additionally, new digital tools such as RDS calculators can help contractors navigate A2L leak detection requirements and mitigation strategies while in the field. AI and controls AI is positioned to continue to make a huge impact in HVAC. We’re seeing more service techs using generative AI and co-pilots for troubleshooting rather than paging through manuals. At the same time, AI technology can predict if connected HVAC units may have issues, making it possible for service techs to address potential issues in their earliest stages or prevent them from happening altogether. Both of these use cases can help technicians service equipment more quickly, efficiently, and accurately, which can increase equipment longevity and reliability while reducing downtime and total cost of ownership. Building performance AI-powered building controls can provide a holistic view into contextualized, full-building performance More HVAC systems are being equipped with AI-enhanced controls and reporting. The capabilities these tools provide can give building owners greater opportunities to optimize building performance, improve occupant comfort and well-being, and more easily reach sustainability targets. From a building management perspective, AI-powered building controls can provide a holistic view into contextualized, full-building performance, occupant experience, and sustainability. Openness and flexibility As AI becomes more commonplace, AI-centric building standards, such as ASHRAE Guideline 36, will also continue to emerge that balance sustainability with occupant comfort, health, and safety. As we move into 2025, we can expect to see another year of equipment innovations, technology advancements, and evolving regulations. As an industry, we continue to face change with openness and flexibility. And it’s this mindset that empowers us to meet, and exceed, expectations – now and in the year to come.
As environmental regulations become increasingly stringent, the HVAC/R industry is turning to sustainable refrigerants to minimize environmental impact. A3 refrigerants—flammable gases with low global warming potential (GWP)—are emerging as a preferred choice. However, their adoption introduces additional regulatory requirements. EPA regulations To address these challenges, the industry is leveraging innovative solutions like enhanced small-diameter copper tubes, which enable compliance with EPA guidelines while maintaining performance and safety standards. In this article, we’ll explore key EPA regulations for A3 refrigerants and how small-diameter copper tubes play a vital role in optimizing system performance, ensuring safety, and achieving regulatory compliance. Understanding A3 Refrigerants A3 refrigerants help HVAC/R systems align with current and upcoming environmental regulations A3 refrigerants are characterized by their low GWP and flammability, making them a sustainable alternative to traditional high-GWP refrigerants. Common examples include propane (R-290) and isobutane (R-600a). By reducing greenhouse gas emissions, A3 refrigerants help HVAC/R systems align with current and upcoming environmental regulations. Their benefits go beyond regulatory compliance. energy efficiency A3 refrigerants improve energy efficiency, enabling systems to operate more effectively while consuming less energy. This dual advantage of sustainability and operational efficiency reduces both carbon footprints and operating costs. As global regulations continue to phase out high-GWP refrigerants, A3 options stand out as a viable solution that balances environmental responsibility with system performance. Their efficiency and compliance capabilities position A3 refrigerants as a key player in the future of HVAC/R system design. Advantages of Small-Diameter Copper Tubes 1. Meeting EPA Charge Limits Small-diameter copper tubes offer a significant advantage in adhering to EPA refrigerant charge limits. With their reduced internal volume, these tubes require less refrigerant to maintain optimal performance. This feature is particularly beneficial when working with A3 refrigerants, as the EPA enforces strict charge limits to mitigate flammability risks while upholding efficiency. 2. Boosting System Efficiency with Enhanced Heat Transfer When enhanced with internal grooves, small-diameter copper tubes maximize surface area contact with refrigerants Copper’s exceptional thermal conductivity, even with smaller tube diameters, ensures effective heat transfer. When enhanced with internal grooves, small-diameter copper tubes maximize surface area contact with refrigerants, further increasing heat transfer efficiency. This improvement translates to lower energy consumption and reduced operating costs, all while delivering reliable cooling performance. 3. Durability, Safety, and Ease of Installation Using small-diameter copper tubes reduces the refrigerant charge required within a system, enhancing safety. Copper’s lightweight and flexible properties, especially when annealed, simplify installation, particularly in compact systems with complex configurations. Its natural corrosion resistance also ensures durability and long-term reliability, minimizing maintenance needs over the equipment’s lifespan. Innovating for a Sustainable Future As the HVAC/R industry transitions to A3 refrigerants, adapting to stricter EPA regulations requires innovative system designs that address safety, efficiency, and performance challenges. Small-diameter copper tubes provide a practical solution by reducing refrigerant charges, enhancing heat transfer, and delivering reliable, durable performance. reducing environmental impact These copper innovations are especially valuable for compact, high-performance systems that demand precision and compliance with environmental standards. By embracing these advancements, the HVAC/R industry can ensure systems are future-ready, capable of meeting evolving regulations while maintaining efficiency and safety. Small-diameter copper tubes are paving the way for a more sustainable HVAC/R landscape, helping businesses succeed in reducing their environmental impact while achieving regulatory compliance.
Until a couple of years ago, most of the talk about heat pumps occurred around this time of year, when more than half the planet prepares for an autumn cooldown. These discussions were typically limited to regions that only experienced moderate winters. But as anyone who has recently perused an HVACR trade magazine or website—or participated in an industry webinar, event, or social media conversation—can tell you, the topic of heat pumps is virtually unavoidable. Not only do heat pump discussions now occur year-round, but they’ve also ascended to consistent headline status and transcended the traditional boundaries of moderate climates. The decarbonization megatrend One might say heat pumps have taken their place on the global stage. If you’re asking why this has happened, the answer requires just three words: the decarbonization megatrend. However, for industry professionals looking to grow their businesses, it’s helpful to gain a deeper understanding of heat pumps—how they work, ways they are currently meeting HVACR needs, and where the technology is headed for next-generation applications. Through this understanding, members of the industry can better forecast customer needs as well as identify opportunities for expanding in both current markets and, potentially, new ones. How heat pumps work—don’t let the name fool you The heat released as the refrigerant condenses is then transferred to interior spaces What heat pumps do and, more specifically, how they do it provides the key as to why they are now being considered a “hero” of decarbonization. The term can be misleading, because “heat pumps” do not generate heat. Because of this, heat pumps are being more widely embraced as the lower-carbon-emission alternative to combustion-based heating technology that uses, for example, fossil fuels. Instead of creating heat, heat pumps extract heat energy from where it’s not needed and move it to where it is needed. When a heat pump is in heating mode, its refrigerant evaporates as it absorbs heat from the outside. The heat released as the refrigerant condenses is then transferred to interior spaces. In warmer weather, a heat pump kicks into cooling mode and the process is reversed, as heat is extracted inside and released outside. This non-combustion process of moving heat from one place to another provides several potential benefits to society: Heat pumps support the megatrend toward decarbonization. They replace fossil-fuel heating with high-efficiency technology. They can be paired with lower-global-warming-potential (GWP) A2L refrigerants—such as R-454B and R-32—to further increase environmental benefits, while offering similar performance to the legacy R-410A. They offer the ability to tap into alternative energy sources, such as industrial waste heat as well as heat sourced from the air (ambient), ground (geothermal), or lakes/ponds (water). Meeting today’s needs—these aren’t your grandfather’s heat pumps Heat pump technology has been commercially available and in use since the 1950s. Early versions of heat pumps were essentially reversible air conditioning units, and most used traditional refrigerants—like R-22 and, more recently, R-410A. These units performed well and operated safely using lower-toxicity, nonflammable (A1) refrigerants. However, they were known to sometimes struggle at lower ambient temperatures. As often happens in the world of science and technology, challenges drive the search for solutions. Today, we’re seeing innovations that result in efficient, effective cold-climate heat pumps that optimize various components, such as compressors, heat exchangers, expansion valves, and their controls. Thanks to these innovations and others, the U.S. and other countries are experiencing broader heat pump adoption and, in turn, supporting progress toward decarbonization. Heat pump technology has been commercially available. Increasing heat pump accessibility and viability in more places and spaces is also critical to the HVACR industry’s commitments to the environment—and its need to heed regulations advancing the transition to systems reducing climate impact. Emerging systems use mildly flammable (A2L) refrigerants. They are similar in design to legacy systems and include modifications to mitigate risks associated with the change to A2Ls. Where things are headed—heat pump technology is just getting started Even with the significant advances we’ve seen in colder-climate heat pumps, there is still untapped potential in terms of what the technology can achieve. We can expect to see continued innovation as end-user needs and environmental priorities continue to evolve. Some foreseeable growth areas for heat pumps include: Traditional applications—that is, moderate climates Expansion into nontraditional climates—heating in very cold climates and cooling in hotter regions Domestic water heating, replacing fossil-fuel systems Leveraging a variety of heat sources—geothermal, air-sourced, and water-sourced Harnessing waste heat generated by energy-intensive industrial processes Use of lower-GWP A2L refrigerants System optimization will also drive greater use of lower-GWP A2L refrigerants, such as R-454B Supporting these growth areas will be innovations that optimize high-performance, high-efficiency delivery of extracted heat, using a combination of traditional and new split-ducted, ductless/mini-split, and mono-block technologies. System optimization will also drive greater use of lower-GWP A2L refrigerants, such as R-454B, while limiting the use of highly flammable refrigerants such as R-290. Refrigerant selection will also play an increasingly important role and may offer additional opportunities for application-specific technology. As heat pump applications expand, we can expect to see greater focus on selecting the optimum refrigerant to use as the working fluid. Criteria will weigh system design, operating conditions, and other priorities against key refrigerant properties: Physical—boiling point, vapor pressure, density, and material compatibility Thermodynamic—cooling/heat capacity, energy efficiency, pressure-enthalpy (PH) curves Environmental—ozone depletion potential (ODP) and global warming potential (GWP) Safety and health—flammability and toxicity Conclusion: There’s strong and ample reason to “stay pumped” Over the past several years, members of the HVACR industry have enthusiastically embraced new heat pump solutions. Evolving heat pump technology and expanding applications will continue as the industry progresses along the path of more energy-efficient, lower-GWP, and more sustainable new-generation and next-generation heating and cooling. This, coupled engineering and science that leverages untapped heat pump potential, will mean more opportunities for HVACR contractors to deliver new options to the markets they serve. With a strong understanding of their customers’ individual heating and cooling needs, climate challenges, and sustainability goals, contractors can confidently select the best heat-pump refrigerant solution.
Editor's Note
The HVAC Industry gathered in Orlando for AHR Expo 2025, focusing on the latest advancements in technology. Attendees included contractors, manufacturers, engineers, system design professionals, facility managers, architects, wholesalers, and distributors. This year’s expo highlighted game-changing innovations, regulatory shifts, and emerging trends designed to enhance efficiency, sustainability, and connectivity. For HVAC professionals, these developments translate into practical solutions that improve system performance, optimize energy use, and simplify compliance with evolving industry standards. The Next Phase of Refrigerant Transition The transition to A2L refrigerants is a dominant theme at this year’s expo, with major players such as Arkema, Chemours, LG Electronics, Rheem, Daikin, and others showcasing the latest refrigerants and equipment solutions. Following the deadline of Jan. 1, 2025, the shift from R-410A to R-32 and R-454B is well underway, with 80% of manufacturers opting for R-454B. While concerns about flammability persist, experts emphasize that proper training and system design can mitigate risks. LG Electronics' full product line Some OEMs opted for R-454B as an option that is closer to a “drop-in” solution Some OEMs opted for R-454B as an option that is closer to a “drop-in” solution. Daikin was among the manufacturers to go all-in on R-32, which required a complete redesign of product components, ultimately pioneering to more efficient, cost-effective systems, according to the company. LG Electronics' full product line now uses R-32 refrigerant, and they started shipping products in December. All R-410A equipment will be gone by the end of Q1. variety of products on R-454B refrigerant Rheem announced their 100-year anniversary, and a new tagline, "Engineered for Life." They say the trend is toward side-discharge heat pumps, although the industry needs a mix of both. They had a variety of products on display that use R-454B refrigerant. Attendees at AHR Expo 2025 came away with an understanding that refrigerant regulations and selecting compatible equipment will be crucial for ensuring smooth transitions in commercial and residential applications. Intelligent Building Automation and Controls Smart HVAC technology is revolutionizing building control, with AI-driven automation Smart HVAC technology is revolutionizing building management, with AI-driven automation, IoT connectivity, and remote monitoring taking center stage. Companies like Distech Controls and Schneider Electric are introducing IP-based controllers that integrate seamlessly with existing building management systems. Belimo’s intelligent butterfly valve and Delta’s Node-RED Programming with built-in Python support, among other products, are making automation more powerful and user-friendly. Copeland’s Sensi Touch 2 smart thermostat Copeland’s Sensi Touch 2 smart thermostat and Sensi equipment interface module (EIM) can eliminate the need to pull additional wires during installation. The system is weatherproof, indoor, or outdoor, and communicates using radio frequency (RF). AHR Expo 2025 made a strong case that investing in smart controls will improve operational efficiency, reduce downtime, and enable predictive maintenance. Hydronic Systems for Data Center Cooling One major player is Bell & Gossett/Xylem, whose hydronic cooling systems target data center market The rise of data center cooling solutions was another recurring theme at AHR. One prominent player is Bell & Gossett/Xylem, whose hydronic cooling systems target the data center market. The company’s e-1531X and e-1532X smart pumps offer enhanced energy efficiency and a larger "efficiency island." These systems are designed to meet the growing demand for sustainable data center cooling, providing a net-zero roadmap. As data center energy consumption rises, hydronic solutions offer a scalable, efficient approach to thermal management. Heat Pumps Expand Capabilities and Market Reach Heat pumps continue to dominate as a top energy-efficient alternative for commercial and residential applications. Companies such as Danfoss, Mitsubishi, and Samsung are pushing the boundaries with heat pumps that operate in extreme temperatures. Danfoss is progressing forward related to four application areas at AHR 2025--heat pumps, data centers, RTU/DOAS, and retail/refrigeration. Emphasis is on lower emissions and better energy efficiency. Midea drew a lot of attention at AHR 2025, including modular air handler Midea drew a lot of attention at AHR 2025, including their modular air handler – the EVOX G³ – that breaks down into three pieces for easy movement and installation in any of six configurations. They are also opening showrooms throughout the country so consumers and contractors can see and touch the products. Integration with renewable energy sources Johnson Controls-Hitachi mini-splits have a self-cleaning feature called FrostWash Johnson Controls-Hitachi Air Conditioning’s Hitachi mini-splits have a self-cleaning feature called "FrostWash;" they intentionally build a frost layer on the coil so the fine particulates can be captured and then melted away, thus avoiding mold and other contaminants. It can be used in lieu of UV light, which damages plastics. The heat pump market is growing rapidly, and advancements in low-temperature performance and integration with renewable energy sources will drive adoption. The Drive Toward Sustainability Sustainability is a recurring theme at the expo, with manufacturers prioritizing energy-efficient equipment, smart automation, and low-GWP refrigerants. Companies like Lennox, and Rheem are launching highly efficient packaged rooftop units and unitary heat pump systems. Grundfos’s distributed pumping technology and Ziehl-Abegg’s ZAcore intelligent control platform further demonstrate the industry's push toward lower energy consumption and minimal environmental impact. Investing in sustainable HVAC technologies Availability is paramount, and they are opening a new factory in Mexico Lennox is serving the "emergency replacement" market for HVAC equipment with their Xion line. Availability is paramount, and they are opening a new factory in Mexico. Telling the "story" of humidification at AHR 2025, Condair has products for any vertical. They say more education and awareness are needed on the value of humidification. As regulations tighten and demand for green building solutions rises, investing in sustainable HVAC technologies will be critical for long-term success. Smarter, Cleaner, and More Efficient AHR Expo 2025 underscores the industry's shift toward smarter, cleaner, and more efficient HVAC solutions. Whether it’s refrigerant transitions, intelligent automation, or advanced heat pump technology, staying ahead of these trends will help HVAC professionals deliver superior performance while meeting regulatory requirements. The innovations showcased in Orlando set the stage for a future where HVAC systems are not only more efficient and environmentally friendly but also easier to manage and integrate into modern buildings.
TE Connectivity’s main product categories for the HVAC market are power interconnects, signal interconnects, magnet wire for motors, and heat-shrink tubing to seal against environmental factors. component materials The company works with HVAC original equipment manufacturers (OEMs) to solve challenges such as harsh environments, safety, and power and signal usage. Although components are a “small” element when an OEM assembles an HVAC system, their impact can be big. For example, a tiny component not producing a spark could make it safer to introduce mildly flammable refrigerants into the newer HVAC systems. Addressing material compatibility Raising questions about component materials not degrading by exposure to newer chemicals over time Also related to the transition to newer refrigerants is the issue of materials compatibility, raising questions about component materials not degrading by exposure to newer chemicals over time. “The big trends in HVAC are higher efficiency, more intelligence (in the context of the Internet of Things), faster data transmission, better safety, and more reliability,” says Joseph Burch, Business Development Manager for TE Connectivity’s Appliance Business Unit. product portfolio TE Connectivity is a brand associated with high quality. OEM customers think of the company (rather than lower-cost competitors) when they have a critical design and/or they need to access TE Connectivity’s vast product portfolio spanning a variety of markets. Broadly speaking, their products include wire-to-board connectors and wire-to-wire connectors at a range of amperages, voltages, and sealing requirements. The broad product line means there are likely solutions within the TE Connectivity family for many OEM design needs. durability and sustainability “We try to meet customers where they are and where the supply chain is,” says Burch. In addition to dealing directly with OEMs, the company works around the world alongside contract manufacturers of various subsystem components. Currently, TE Connectivity is a global leader with a strong focus on reliability, durability, and sustainability in its connectivity and sensor products. They serve a range of industries, including HVAC, and are known for their contributions to technological advancements. the efficiency of heat pumps Higher efficiency requires precise monitoring of electrical signals and transmission of data For TE Connectivity and others, driving development in the HVAC market is the transition to heat pumps, a rapidly growing equipment category. Achieving the improved efficiency of heat pumps raises the stakes from a component perspective boosting the need for sensors and faster data transmission. Higher efficiency requires precise monitoring of electrical signals and transmission of data. Integration of heat pumps with renewable energy sources, such as solar, requires even more connections and better communications. rapid data transmission The ability of newer systems to adapt to changing environmental conditions depends on the fast transmission of sensor data to guide operation. In effect, rapid data transmission, using signal interconnects, makes it possible to achieve higher efficiencies that are critical to newer systems. The faster signals are communicated, the more efficient the systems are. Larger systems are increasing the demand for higher power, and efficiency standards are driving more sensing needs, as is the trend toward smart homes. flame retardant Addressing one of the big challenges in the HVAC market, TE Connectivity sells its products to withstand harsh environments such as moisture and vibration. In a typical HVAC scenario, half the system is located outdoors and exposed to weather and other elements. From a safety perspective, electrical connectors on HVAC units are unattended 24/7, so reliability is critical, and materials must be flame retardant and withstand high temperatures. Parts must adhere to the Underwriter’s Laboratories (UL) VO flammability rating, which means a flame extinguishes within 10 seconds and there is no dripping. competitive analysis TE Connectivity’s business development teams seek broadly to assess the size of a market, such as HVAC, and the magnitude of the opportunity in each market for their various product lines. In addition, the company attends trade shows to see the latest trends to seize the opportunities to promote the company’s brands and products to the market. TE Connectivity engineers conduct “in-house teardowns” of existing OEM products to analyze how various components are used and how they might be improved to refine the overall solution. TE Connectivity’s competitive analysis labs are frequently looking for new opportunities to innovate. address design-related issues A “system architecture team” within the engineering group is tasked with understanding how systems work TE Connectivity’s engineers also work directly with OEM customer engineers to address any design-related issues. The field engineering team works on the “front line” with customers and provides feedback to the company’s development engineering team, which gets involved as needed. A “system architecture team” within the engineering group is tasked with understanding how systems work, new technologies, new regulations, and innovations, and establishing roadmaps to forecast needs looking ahead five to ten years. Multiple design trends “Our engineering teams are problem-solvers, focused on connectivity problems across many industries,” says Joshua Poterjoy, Senior Manager, Product Development Engineering. Multiple design trends are among the factors driving product needs, such as miniaturization, higher-speed data transmission, the need for ergonomic and modular designs (for ease of assembly), and components designed for assembly and packaging automation. Components also adhere to Restriction of Hazardous Substances (RoHS) directives that avoid the use of hazardous substances in electrical and electronic equipment. ease of installation GRACE INERTIA series signal connectors provide fine-pitch connections for smaller electronics Creating components to deploy ergonomic and modular designs promotes ease of installation, both for assembly by the OEM company and for installers in the field. Components are designed to be as simple as possible while achieving all the operation and reliability standards. Quick-connect and twist-and-lock systems provide an assuring “click” when a robust connection is made. For example, the company’s Universal MATE-N-LOK multi-position power connectors are often used in the HVAC market from powering control cards to motors to fans. Also, the GRACE INERTIA series signal connectors provide fine-pitch connections for smaller electronics. TE Connectivity’s history TE Connectivity’s history can be traced back to the founding of AMP Incorporated in 1941, which pioneered the development of electrical connectors. In the 1990s, AMP became part of the Tyco International conglomerate, further expanding and diversifying. In 2007, Tyco International split into three independent companies, including Tyco Electronics, which focuses on connectivity and sensor solutions. Tyco Electronics changed its name to TE Connectivity in 2011.
SNAP Rule 26 marks an important milestone in the transition from commercial refrigeration to new refrigerants. The rule lists refrigerant substitutes that provide a spectrum of technological solutions to meet required performance, global warming potential (GWP), safety, and environmental standards. SNAP stands for Significant New Alternatives Policy, a program by the U.S. EPA (Environmental Protection Agency) under the Clean Air Act. In general, the program aims to evaluate and regulate substitutes for ozone-depleting substances, considering their overall risks to both human health and the environment. Impact of SNAP Rule 26 Final SNAP Rule 26, Protection of Stratospheric Ozone, lists acceptable substitutes in commercial and industrial refrigeration. SNAP Rule 26 will be effective July 15, 2024. The incorporation by reference of certain material listed in the rule is approved by the Director of the Federal Register as of July 15, 2024. The incorporation by reference of certain material listed in the rule is approved by the Director of the Federal Register “To date, the SNAP program has provided a very effective framework for evaluation and approval in support of innovation and the transition to new technology,” says Andrew Pansulla, Technical Service Engineer, The Chemours Company, a global chemistry company that provides a range of refrigerant products. We asked Pansulla to elaborate further on the impact of SNAP Rule 26 and what lies ahead. Q: How will the Rule’s finalization impact various commercial refrigeration sectors? Pansulla: The rule’s finalization will impact commercial refrigeration in several ways. Areas, where impact will likely be seen, include providing more acceptable refrigerant options, adherence to updated standards, new equipment design standards, and the exemption of propane from the venting prohibition for refrigerated food processing and dispensing equipment. These impacts could trigger changes in operational, manufacturing, and environmental compliance strategies in the commercial refrigeration sectors. SNAP Rule 26 will enable the adoption of the listed substitutes, including Chemours Opteon™ refrigerants, with global warming potential (GWP) lower than existing refrigerants. This rule does not require any changes to existing equipment and will impact only new equipment that uses the specific substances referenced in the SNAP rule. Q: What is the outlook for additional requirements for safe handling and use of alternative refrigerants? What specific safety standards are expected or appropriate? Pansulla: As part of the comparative risk framework used by the EPA to assess new alternatives, the EPA considers and implements use conditions that will ensure the safe use of products. These use conditions rely upon existing safety standards (e.g., UL and ASHRAE) which are available at the time the rule is finalized. In the case of SNAP Rule 26, many of the use conditions require adherence to UL 60335-2-89 and ASHRAE-15-2022. These standards are reviewed and updated periodically to maintain relevance with the products subject to the standards. Q: What are any limitations of the use of A2L refrigerants under SNAP Rule 26? Pansulla: There are two main categories of limitations under SNAP Rule 26. The first, as mentioned above, is the adherence to specific safety standards that apply to refrigerants that are designated as mildly flammable (A2L). The second is based on the GWP of the refrigerant. In the case of the A2L refrigerants subject to SNAP Rule 26, the EPA imposed conditions on the type of equipment and specific circumstances in which the substitute may be used. For example, the EPA is permitting the use of R-454A in supermarket systems, but only on the high side of a cascade system, or when the refrigerant charge capacity is less than 200 pounds. Q: Which new-generation A2L refrigerants are fit for which commercial refrigeration applications? Pansulla: Under SNAP Rule 26, the EPA deems R-1234yf, R-1234ze(E), R-454C, R-455A, R-457A, and R-516A as acceptable subject-to-use conditions for various commercial refrigeration applications. This selection is primarily driven by these refrigerants having GWPs under 150. However, certain applications necessitate refrigerants with higher GWPs due to unique performance characteristics. For example, R-454B and R-32 were listed for industrial process refrigeration with exiting fluid temperatures below minus 30 degree Celsius because these two specific refrigerants have lower boiling points than the other six less-than-150-GWP alternatives. However, it is critically important to consider the additional use conditions when designing equipment with refrigerants that have a GWP greater than 150. Q: So various equipment needs different refrigerants? Pansulla: The EPA purposefully lists several different refrigerants in each application to allow for equipment manufacturers to consider a variety of different factors that go into refrigerant selection, such as energy efficiency, capacity, normal boiling point, temperature glide, cost, safety, and use conditions. There is no one-size-fits-all solution for the entire commercial refrigeration industry. Q: How can commercial refrigeration businesses achieve a smooth transition to A2Ls? Pansulla: Keys to a smooth transition to A2Ls include understanding what refrigerants the EPA has approved as acceptable substitutes under the SNAP program, the sector-based GWP limits imposed by the Technology Transitions Program under the American Innovation and Manufacturing (AIM) Act, and which refrigerants provide the best combination of technical performance and environmental characteristics. Many resources are available to navigate the regulatory landscape and select the best low-GWP refrigerants to meet the needs of this industry. Working with companies like Chemours, who has nearly a century of refrigerant innovation and experience, is a great first step in the transition process. Q: What is the “staying power” of A2Ls — based on their chemistry, sustainability, and other attributes, combined with regulations such as SNAP Rule 26? Pansulla: The identification, selection, and development of new refrigerants that deliver required performance while meeting increasingly stringent environmental standards is a challenging process. With the identification of certain hydrofluoroolefin-based (HFO) refrigerants as an alternative to meet these criteria came a new safety classification. These HFO-based refrigerants are classified as A2Ls. While slightly more flammable than existing hydrofluorocarbon-base (HFC) refrigerants, HFOs are much less flammable than hydrocarbons, which are classified as A3 (two categories higher on the ASHRAE flammability spectrum). Moreover, such refrigerants offer an excellent alternative to substances with higher toxicity, such as R-717. The listing of A2L refrigerants in SNAP Rule 26 clearly indicates that such refrigerants can be used safely in commercial refrigeration as well as many other applications, which are subject to the SNAP Program, when adhering to the applicable safety standards.
Case studies
PARAT (Parat Halvorsen AS) will deliver the modern IEH 2 x 20MW Electrode Steam Boilers with 6kV connection to AITESA - VALTEC UMISA. The boiler system will have a design pressure of 16 barg and a design temperature of 204°C. The delivery also includes the circulation pump, feedwater pump, chemical dosing unit, start-up, and training of personnel. PARAT’s first Power to Heat project in Spain PARAT is very excited about their first Power to Heat project in Spain PARAT is very excited about their first Power to Heat project in Spain and sees several upcoming projects in the country, with a high focus on installing new renewable energy. The Viscofan Group is the globally renowned company in casings for meat products, which it distributes in over 100 countries worldwide. About Viscofan Viscofan is a global firm in the meat industry’s manufacturing, production and distribution of casings. Their production sites are located in Spain, Australia, Brazil, Belgium, Canada, China, the Czech Republic, Germany, Mexico, Serbia, Uruguay and the United States of America (USA). Viscofan wants to go beyond the traditional borders with a new purpose - Reshaping food and well-being for many, for long, seeking to help to provide access to food and nutrition throughout the world, and to improve the well-being and health of people. They hope to achieve all this with a long-term vision of generating a permanent impact over time. PARAT Power to Heat system will be installed at the Viscofan site in Navarra, Spain.
Paragon House – an 11 story teaching block at the University of West London (UWL), has recently replaced its gas boiler heating system with a ground-breaking first for Europe and the UK, by Finn Geotherm installing three x 210kW Panasonic air-to-water heat pumps with a bespoke cascading thermostatic control system to heat the entire building. The University of West London were looking to improve the energy performance of the building in a more sustainable way, reducing their carbon footprint and energy consumption, with the help of a Salix funded government grant (the UK Government’s Public Sector Decarbonization Scheme (PSDS) and the Low Carbon Skills Fund (LCSF)). Paragon House installs Panasonic heat pump system UWL appointed Ameresco as the main energy improvement contractor for the project UWL appointed Ameresco as the main energy improvement contractor for the project with Finn Geotherm as the contractor who specified and installed the 3 x 210kW Panasonic heat pump system, along with a bespoke cascade thermostatic control system that links with the building’s BMS. Paragon House is situated in a prestigious London location adjacent to the M4 with a mix of classroom and lecture theatres across 11 floors. Sustainable energy efficient system The main challenge for the project was that the University ideally wanted minimum internal disruption and an energy efficient system that could link and work with their existing pipework, radiators, cassettes and fan coils. A further challenge was lifting the three large 210kW units, each 6 square meters and weighing just over two tons onto the roof of the 11 story building. Detailed structural surveys were carried out to ensure the weight and distribution of the units at roof level would work effectively and safely. Panasonic air source heat pumps Guy Ransom, the Commercial Director at Finn Geotherm commented, “Originally it was thought that the best solution to meet the heat load for the entire building would be a ground source heat pump system but on initial surveys and inspections, it became apparent that the drilling of bore holes would be impossible given the ground space available and the proximity of the building to the M4 motorway and other busy London road networks.” Guy Ransom adds, “We have worked with Panasonic air source heat pumps over a number of years now and have developed a trusted two-way partnership with the team and where Panasonic has become our manufacturer of choice – we respect the quality of the units – they do what they say they can do.” Panasonic 210kW heat pump units installed Panasonic 210kW heat pump units installed at Paragon House were the first of their kind in the UK The Panasonic 210kW heat pump units installed at Paragon House were the first of their kind in the UK and Europe to be installed – the units offer outstanding efficiency with extremely high SEER and SCOP figures, can operate in temperatures as lows a -17 degrees Celsius in heating mode, are quiet in operation, offer a customizable design with capacities from 20k to 210kW, and can be integrated into a BMS control system. The team at Finn Geotherm worked with Panasonic’s European R&D and UK teams to obtain test data to support the specification of the units. The two teams liaised over a number of weeks to verify the data, ensuring the required range of output and input temperatures would work effectively on the bespoke thermostatic cascading control system. Maximize the use of the heat pump The aim was to maximize the use of the heat pump use when a back-up system was insisted on by the client for the Paragon House project. Guy Ransom stated, “We worked closely with the wider team at Panasonic and carefully laser measured and assessed the heat loss for each area of the building to ensure that the units would be able to distribute a similar level of comfort to the existing gas boiler system.” He adds, “The Panasonic system now installed at Paragon House was the first of its kind in Europe – this ground-breaking project pushes the envelope for similar large renovation projects in the future that are looking to decarbonize their heating systems - the customer is very happy with the end result.” Panasonic system lowers the carbon footprint The Panasonic system has lowered the carbon footprint of the property The Panasonic system has lowered the carbon footprint of the property and is highly energy efficient to run with little impact on the interior pipework and space within the building. The units are located on the roof to ensure they are discreet, quiet and unobtrusive to the surrounding area, having very little impact on the day to day running of the building during installation. A construction of support spreader beams and plates was designed to distribute the load within the tolerance of the roof area. University of West London pleased with the results Claire Willits, the Director of Property Services at the University of West London (UWL) said, “The University of West London has been very pleased with the results of the project and having now been through our first winter running on the new systems we can safely say the technology works!” Claire Willits adds, “This project has made a significant contribution in our carbon reduction journey and has given us reassurance that change for the better of the environment can also be cost-effective and deliver a practical operational solution.” Exceptional energy savings It is estimated that Paragon House will receive energy savings in the region of 1,058,000 kWh per year It is estimated that Paragon House will receive energy savings in the region of 1,058,000 kWh per year. Considering the other two Panasonic installs at UWL, the total amount of energy saving is expected to be in excess of 500 tons of CO2 per annum. The above project was recently announced as the award winner of the National Renewable Heat Project of the Year at the Energy Efficiency Awards 2022. Seamless design and installation Harvey Loyal, Specification Sales London for Panasonic, stated “The control of the 210kW units were new to the market when Finn Geotherm came to us with the project – we worked with the wider Panasonic technical team and Finn Geotherm to provide a seamless design and installation.” Harvey Loyal adds, “As this was a European first and so for peace of mind, the original boilers were kept as a back-up should the outside temperatures reach -5 degree or lower. 12 months following the installation, Paragon House has confirmed the boiler system has not once been utilized and the heating produced from the Panasonic Air-to-Water system fully meets the heating requirements of the building.” Since the initial installation of Panasonic air source heat pumps at Paragon House, Finn Geotherm has installed similar Panasonic systems in several other similar buildings across UWL, as well as many other large projects in and around the London area.
In line with the UK’s Net-Zero targets, local governments are transitioning communities to a greener future. Kemsley Community Centre, based in Sittingbourne, Kent, United Kingdom (UK) were looking for a more energy efficient and sustainable system to heat and cool their large and multiple areas of the community center, in order to replace a 1960’s oil-fired system. Phoenix ACR, specialists in AC and refrigeration, specified a Panasonic R32 split system with 4 x 20kW PACi outdoor units and 11 of the Panasonic PACi NX Elite range of wall mounted indoor units with nanoe X. Panasonic R32 split system installed The new system needed to meet the needs of the entire community center, covering the main hall, bar area and reception area. Each section required units suited to the individual area, which could seamlessly combine and function under a single control system. The Panasonic PACi NX Elite range was specified by installer, Nathan Bell, the Managing Director of Phoenix ACR, who explains “We have worked with Panasonic a lot in the past, so we knew its range was the best to deliver the efficiency, reliability and value for money that was key to this installation. The energy-saving design and high efficiency makes the Panasonic units ideal for this project.” Panasonic PACi NX Elite wall mounted indoor units The PACi NX Elite range allows a great amount of flexibility in design and install The PACi NX Elite range allows a great amount of flexibility in design and install, which was crucial to ensuring we could adapt to the needs of each room, providing the perfect solution for the customer. The addition of nanoe X technology, which inhibits viruses and bacteria, was a key benefit of the Panasonic units, to help provide a better indoor environment for the community center staff and its users in a post-pandemic world.” Featuring nanoe X technology In the main hall and bar area, 11 Panasonic PACi NX Elite wall-mounted units with nanoe X technology were installed. These are especially beneficial for high ceiling areas, such as found in the community center. The reception area has two PACi ceiling suspended units, with the slim design making them more discreet for the smaller room, along with being one of the quietest units currently on the market. Facilities Trustee of Kemsley Community Centre, David Grawler, said “It is so important that we provide a sustainable future for our community. Phoenix ACR recommended this solution, and we are very happy with how it meets our energy efficiency needs. With our old system, if we hired out a single room, we would end up having to heat the entire building.” David Grawler adds, “The new Panasonic system allows us to control all units as one for the entire building, but also enables us isolate the individual spaces, adding a new way for us to function in a more energy efficient way, without having to compromise on comfort.” PACi NX Standard and PACi NX Elite ranges The PACi NX Standard and PACi NX Elite ranges provide high quality heating and cooling The PACi NX Standard and PACi NX Elite ranges provide high quality heating and cooling, boasting top class SEER ratings of A++ and SCOP ratings of A+ and A++ at 10kW respectively. Both provide slim, lightweight and compact designs. The PACi Elite offers greater design flexibility, making it adaptable to various building types and sizes, key to delivering the perfect solution across larger projects. The design allows for high quality under a wide range of conditions, with cooling possible in temperatures as lows as -15 degrees or as high as 46 degrees, and heating in temperatures as low as -20 degrees. Kemsley Community Centre Kemsley Community Centre has a touch screen centralized controller installed behind the bar, allowing the management of the entire system from a single point. Additionally, the system utilizes WIFI adaptors which connect the units to the Panasonic comfort cloud App, allowing for remote management and monitoring of the multiple air conditioning units required for this project. The units came with nanoe X technology as standard, a unique and proven technology to help improve air hygiene by preventing transmission of airborne pathogens, to create a safer and healthier indoor environment. Nanoe X works independently from the heating and cooling operation when the unit is in fan mode, improving protection 24 hours a day, 7 days a week. Panasonic units – a great addition to the community center David Gawler concludes, “The Panasonic units have proven to be a great addition to the community center, they helped us cope during the summer heat wave of 2022, and heating capabilities this winter. It is great that we can still provide comfort in the center to all those who use it whilst also taking a big step to a greener future.”
When they are one of the largest beverage distributors in the U.S., it’s crucial to stay ahead of the curve on everything that drives customer satisfaction, corporate responsibility, and a strong bottom line. Hensley Beverage Company did exactly that when it collaborated with Chemours and American Refrigeration Supplies, Inc. (ARS) to implement a system utilizing a new-generation A2L refrigerant, Chemours Opteon™ XL20 (R-454C). Completed in 2023, the installation paves the way for companies throughout the commercial refrigeration industry to embrace refrigerant technologies that are both cost-effective and environmentally sustainable. Situation The company recently ended an acquisition that grew its distribution footprint into New Mexico Hensley Beverage, a Phoenix-based beverage wholesaler, supports a customer base of more than 9,000 accounts and more than 2,500 individual products, operating out of six locations across Arizona. The company recently completed an acquisition that expanded its distribution footprint into New Mexico, making it one of the largest family-owned and operated beverage distributors in the nation. As it grows, Hensley remains committed to maintaining exceptional product integrity, upholding its multi-generational family business legacy, and supporting a variety of environmental objectives. These factors, coupled with the current regulatory landscape (notably, the phasedown of legacy hydrofluorocarbon (HFC) refrigerants), have put Hensley’s focus on ways to upgrade its refrigeration systems. Phasedown of HFC refrigerants For the past several years, Chemours, ARS, and Hensley have worked together to retrofit the distributor’s existing R-22 and R-404A systems to Opteon™ XP40 (R-449A), a hydrofluoroolefin (HFO) blend offering zero ozone depletion potential (ODP) and a significantly lower global warming potential (GWP) than legacy products. However, with the ongoing phasedown of HFC refrigerants under the U.S. EPA’s American Innovation and Manufacturing Act (AIM), the teams began weighing the benefits of an even bolder upgrade. “Hensley Beverage is proud to partner with Chemours, TBSI, and ARS to help develop innovative solutions and responsible business practices that drive sustainability in our community. These groundbreaking results are a culmination of partnership and collaboration. It is refreshing to work with three organizations that are this passionate about developing pioneering products that will help shape a better future for the communities we serve,” Alex Dunn SVP of Operations, Hensley Beverage. Solution Chemours recommended bringing Opteon™ XL20 (R-454C) into Hensley’s refrigeration plan Even as Chemours, ARS, and Hensley continued to strategically employ retrofit solutions in some areas, they explored options that would put the company in a stronger position for the long term. Chemours recommended bringing Opteon™ XL20 (R-454C) into Hensley’s refrigeration plan. A mildly flammable refrigerant with an ASHRAE A2L safety classification, Opteon™ XL20 is designed for use in new equipment, so Hensley identified an old R-22 system near the end of its life that was ideal for replacement by a new system using Opteon™. Opteon™ XL20 has been used for several years in Europe and is expected to become the new norm in the U.S. by 2026, based on the current direction provided by the EPA. Leveraging its experience in Europe, the Chemours team of technical service and business development resources is prepared to support end users as they consider trial installations using A2L refrigerants. Features of Opteon™ XL20 Opteon™ XL20—the future of sustainable low- and medium-temperature refrigeration GWP of 148 (a 96% reduction versus R-404A) Zero ODP Enables much higher charge sizes than highly flammable A3 refrigerants Is a close performance match to R-22 and R-404A Offers the optimum balance of performance and environmental sustainability Provides an easy, cost-effective alternative to legacy refrigerants in new equipment applications Utilizes well-known technology for ease of service and maintenance Benefits of HFOs Hensley was an early adopter of Opteon™ XP40, retrofitting equipment to experience better “Hensley was an early adopter of Opteon™ XP40, retrofitting equipment to experience better environmental outcomes, as well as high performance in low- and medium-temperature applications. Experiencing these benefits of HFOs whet their appetite to ask, ‘What next?’ With a strong dedication to supporting their communities and the environment while operating an efficient and thriving business, Hensley is a company that pushes the envelope." "Chemours was ready with our next-generation Opteon™ XL20—that will ensure they achieve maximum performance, operating efficiency, and sustainability," Joe Martinko President, Thermal and Specialized Solutions, Chemours. New low GWP refrigerant “Our industry is undergoing some of the most significant regulatory changes in history and will be for the foreseeable future. ARS was excited to work with Chemours and be a part of the launch at Hensley of the new low GWP refrigerant." "It’s been a privilege for ARS to help bring together such an excellent group of partners for this project—and to install a first-of-its-kind system right here in Tucson, a community we’ve proudly served since 1948,” John White President, American Refrigeration Supplies, Inc. Opteon™ XL20 properties ASHRAE Number: R-454C Composition Weight%: R-32/R-1234yf 21.5/78.5 Molecular Weight: 90.8 g/mol Normal Boiling Point: -45.6 °C (-50.0 °F) Critical Pressure: 4318.9 kPa (626.4 psia) Critical Temperature: 85.7 °C (186.2 °F) Liquid Density at 21.1 °C (70 °F): 1058.2 kg/m³ (66.1 lb/ft³) Ozone Depletion Potential (CFC-11 = 1.0): 0 AR4 (AR5) GWP (CO₂ = 1.0): 148 (146) ASHRAE Safety Classification: A2L Temperature Glide: ~6 K (~10.8 R) LFL (UL 60335 2-89 WCF): 0.291 kg/m³ (0.018 lb/ft³). Collaboration and Installation The installation brought together additional resources from the HVACR industry, including Copeland and Heatcraft Refrigeration Products— two ARS manufacturing partners—as well as Technical Building Services, Inc. (TBSI), the local HVACR service provider. As HVACR technology providers helping customers achieve their sustainability, decarbonization, and regulatory compliance goals, Heatcraft and Copeland had the knowledge and experience of emerging A2L requirements and the capabilities to support the project. TBSI was selected as the contractor for installation and servicing. Use of R-22 in other Hensley systems Installation, evacuation, and setting methods were very similar to the recent refrigerants With the team assembled, Chemours took the lead on the project, ensuring that the contractor, Hensley’s service personnel, and others involved were certified through the ESCO Institute’s A2L refrigerant training program, and answering any questions from the local authorities. After safely recovering the R-22 for use in other Hensley systems, the team from TBSI started removing the existing Keg 6 equipment, hanging new evaporator coils, and running new refrigerant lines. Installation, evacuation, and charging procedures were very similar to the current refrigerants in use by industry, making for a time- and cost-efficient process. Next generation of climate technology “Copeland has always been focused on not just setting the standard in climate solutions with pioneering brands in compression, controls, software, and monitoring—but pioneering the evolution in this space. Our role in the system design and installation for Hensley was right in our wheelhouse. What we accomplished together demonstrates that by bringing together energy-efficient products, regulation-ready solutions, and expertise, we can revolutionize the next generation of climate technology for the better,” Brian Schroeder Engineering Manager, Refrigerants, Copeland. “Our tools and gauges were already enabled for the R-454C refrigerant. The startup and charging of both systems went pretty smoothly. TBSI is proud to have participated in the project at Hensley and, by doing so, adding to the variety of equipment we’ve worked on since founding our business in 1990. This was a great opportunity to grow our experience with A2Ls,” Sergio Pelayo Vice President, TBSI. Copeland monitoring data Copeland applied monitoring units to the systems that capture nearly two dozen data points every second To make sure the system performed as expected, Copeland applied monitoring units to the systems that capture nearly two dozen data points every second. The data has shown that the systems are running as designed. “We are thrilled with the results of the R-454C project with Hensley Beverage. As we continue our journey toward new regulation compliance, this successful collaboration has been instrumental in leveraging Heatcraft’s new product design efforts, with A2L refrigerants being an important part of the mix. We are poised to lead the industry and provide more customers like Hensley with cutting-edge solutions that drive their success,” Bob Landi Vice President and General Manager, Heatcraft Refrigeration Products. Summary Influenced by upcoming regulatory changes and stronger organizational ESG commitments, the commercial refrigeration industry’s transition to lower GWP refrigerants is inevitable. Opteon™ refrigerants provide organizations with lower GWP options that can help extend the useful life of their systems, as well as new equipment options that enable decades of reliable operation. Moreover, these systems answer the consumer preference for businesses that utilize responsibly manufactured products and support a greener environment. Hensley’s approach demonstrates an ideal way for companies to meet the needs of refrigerating their products while following the guidelines of the HFC phasedown. It’s important to assess where your equipment is in its lifecycle and determine if it makes the most sense in terms of budget, performance needs, and corporate vision to (1) retrofit existing equipment for more efficient and sustainable operation or (2) replace it with A2L refrigerant technologies and products.
The emphasis on sustainable processes has never been greater than in today’s marketplace. Environmental conservation must be considered in every phase of appliance design and in every step of the product lifecycle. Product designers use sustainable materials to limit carbon footprint, efficient and reliable components are chosen to reduce environmental impact during product operation, and, after the end of a product’s useful life, responsible companies must even plan for recycling and disposal. TE Connectivity’s Industrial Technology Index, a survey of global companies focused on the innovation culture of engineers and executives, showed that innovation and sustainability are business priorities for most engineers and executives alike. Sustainable practices are now being integrated early in the innovation process, providing more opportunities to limit the environmental impact of new products. Sustainable design considerations throughout the product life cycle Sustainable Design Considerations TE’s connectors play a vital role in enabling the safe, reliable and efficient interaction of a wide variety of essential components. A growing emphasis on sustainable practices has compelled the team to develop sustainable products for various types of equipment. Designs for sustainability replace virgin materials that have large carbon footprints with recycled or renewable, biological-based alternatives. Designs for sustainability replace virgin materials that have large carbon footprints Likewise, efficiency improvements during manufacturing, as well as more reliable, energy-saving connector designs, further limit the environmental footprint of these products. TE’s cluster block products, used for compressor applications like air conditioners, heat pumps, and refrigerators, have been redesigned with this sustainability in mind. These innovative products will help enhance the reliability of compressors, while reducing energy consumption and minimizing carbon footprint. Enhanced Safety, Performance and Productivity Reducing the temperature of connectors in operation results in less wasted energy. This can improve the performance of the compressor which translates to better appliance efficiency. The sustainable cluster block achieves this goal with an additional contact beam, shown in Figure 2, that minimizes electrical contact resistance, optimizing the energy transmission, reducing temperature rise and providing the required connection. Additionally, the innovative lead-in alignment feature, illustrated in Figure 3, helps to error-proof the connection, improving safety as well as productivity of automated assembly processes. The sustainable cluster block achieves this goal with an additional contact beam Potential health hazards The cluster block uses a renewable, plant-based material (Figure 4) that can be sustainably produced with minimal impact to the environment. This high-performance material meets the stringent International Electrical Code (IEC) with flammability ratings tested to UL 94 V-0, CTI 600V and GWEPT 750°C (1380°F) no flame requirements. Made up of 50% castor bean oil, the material is halogen-free which further limits the potential environmental impact. This material reduces the carbon footprint by more than 45% during production, use and disposal while also eliminating potential health hazards. Conversion of renewable, plant-based material into halogen-free, flame-resistant resin for the cluster block housing Minimizing environmental impact TE’s new cluster block (Figure 5) was designed to minimize environmental impact by reducing consumption of natural resources, minimizing waste and promoting renewable energy. To mitigate climate change, the cluster block connector features 19% lower plastic usage and 26% lower metal usage, when compared to legacy connectors (Figure 6). The cluster block connector features 19% lower plastic usage and 26% lower metal usage The sustainable cluster block will help TE contribute to maximizing the safety, performance and sustainability of compressor applications. This technology is a key step in meeting the growing demand for cost effective, environmentally friendly solutions that are compatible with modern automated assembly processes. As the appliance industry continues to evolve, sustainable connector designs will undoubtedly play a key role in shaping the future of compressor applications and beyond.
Tarkett’s vinyl flooring factory in Ronneby, Sweden, is using ABB data insights and service expertise to save 800 megawatt-hours (MWh) of energy per year from their motor-driven systems. This is around 1 percent of the site’s total energy consumption in a year and is equivalent to the energy needed to charge 68 million smartphones for the same amount of time. ABB Ability™ Digital Powertrain Energy Appraisal solution With the current energy prices, the payback period would be only 18 months or less With the data gathered through the ABB Ability™ Digital Powertrain Energy Appraisal solution, ABB identified that upgrading 10 motors to IE5 SynRM technology would boost efficiency from 80 percent to 95 percent. With the current energy prices, the payback period would be only 18 months or less. The service is underpinning Tarkett’s wider strategy to deploy innovative technology and act sustainably in its operations. Upgrading motors to ensure energy efficiency “The biggest lesson for us is that we’ve been maintaining motors that we should have exchanged years ago. We are really impressed by the savings obtained by just upgrading 10 of our motors to more efficient ones,” says Ted Evaldsson, Tarkett’s Supervisor Electrical Maintenance. Having seen the positive results, Tarkett is now planning to further connect additional motors with ABB digital services to yield greater energy savings at Ronneby in 2023, with the help of the digital energy audit. Tarkett extends the coverage of monitored assets By extending the coverage of monitored assets, Tarkett will be better positioned to constantly identify and prioritize energy-saving opportunities at a larger scale, while also saving considerably in CO2 emissions.
PARAT (Parat Halvorsen AS) will deliver the modern IEH 2 x 20MW Electrode Steam Boilers with 6kV connection to AITESA - VALTEC UMISA. The boiler system will have a design pressure of 16 barg and a design temperature of 204°C. The delivery also includes the circulation pump, feedwater pump, chemical dosing unit, start-up, and training of personnel. PARAT’s first Power to Heat project in Spain PARAT is very excited about their first Power to Heat project in Spain PARAT is very excited about their first Power to Heat project in Spain and sees several upcoming projects in the country, with a high focus on installing new renewable energy. The Viscofan Group is the globally renowned company in casings for meat products, which it distributes in over 100 countries worldwide. About Viscofan Viscofan is a global firm in the meat industry’s manufacturing, production and distribution of casings. Their production sites are located in Spain, Australia, Brazil, Belgium, Canada, China, the Czech Republic, Germany, Mexico, Serbia, Uruguay and the United States of America (USA). Viscofan wants to go beyond the traditional borders with a new purpose - Reshaping food and well-being for many, for long, seeking to help to provide access to food and nutrition throughout the world, and to improve the well-being and health of people. They hope to achieve all this with a long-term vision of generating a permanent impact over time. PARAT Power to Heat system will be installed at the Viscofan site in Navarra, Spain.
Paragon House – an 11 story teaching block at the University of West London (UWL), has recently replaced its gas boiler heating system with a ground-breaking first for Europe and the UK, by Finn Geotherm installing three x 210kW Panasonic air-to-water heat pumps with a bespoke cascading thermostatic control system to heat the entire building. The University of West London were looking to improve the energy performance of the building in a more sustainable way, reducing their carbon footprint and energy consumption, with the help of a Salix funded government grant (the UK Government’s Public Sector Decarbonization Scheme (PSDS) and the Low Carbon Skills Fund (LCSF)). Paragon House installs Panasonic heat pump system UWL appointed Ameresco as the main energy improvement contractor for the project UWL appointed Ameresco as the main energy improvement contractor for the project with Finn Geotherm as the contractor who specified and installed the 3 x 210kW Panasonic heat pump system, along with a bespoke cascade thermostatic control system that links with the building’s BMS. Paragon House is situated in a prestigious London location adjacent to the M4 with a mix of classroom and lecture theatres across 11 floors. Sustainable energy efficient system The main challenge for the project was that the University ideally wanted minimum internal disruption and an energy efficient system that could link and work with their existing pipework, radiators, cassettes and fan coils. A further challenge was lifting the three large 210kW units, each 6 square meters and weighing just over two tons onto the roof of the 11 story building. Detailed structural surveys were carried out to ensure the weight and distribution of the units at roof level would work effectively and safely. Panasonic air source heat pumps Guy Ransom, the Commercial Director at Finn Geotherm commented, “Originally it was thought that the best solution to meet the heat load for the entire building would be a ground source heat pump system but on initial surveys and inspections, it became apparent that the drilling of bore holes would be impossible given the ground space available and the proximity of the building to the M4 motorway and other busy London road networks.” Guy Ransom adds, “We have worked with Panasonic air source heat pumps over a number of years now and have developed a trusted two-way partnership with the team and where Panasonic has become our manufacturer of choice – we respect the quality of the units – they do what they say they can do.” Panasonic 210kW heat pump units installed Panasonic 210kW heat pump units installed at Paragon House were the first of their kind in the UK The Panasonic 210kW heat pump units installed at Paragon House were the first of their kind in the UK and Europe to be installed – the units offer outstanding efficiency with extremely high SEER and SCOP figures, can operate in temperatures as lows a -17 degrees Celsius in heating mode, are quiet in operation, offer a customizable design with capacities from 20k to 210kW, and can be integrated into a BMS control system. The team at Finn Geotherm worked with Panasonic’s European R&D and UK teams to obtain test data to support the specification of the units. The two teams liaised over a number of weeks to verify the data, ensuring the required range of output and input temperatures would work effectively on the bespoke thermostatic cascading control system. Maximize the use of the heat pump The aim was to maximize the use of the heat pump use when a back-up system was insisted on by the client for the Paragon House project. Guy Ransom stated, “We worked closely with the wider team at Panasonic and carefully laser measured and assessed the heat loss for each area of the building to ensure that the units would be able to distribute a similar level of comfort to the existing gas boiler system.” He adds, “The Panasonic system now installed at Paragon House was the first of its kind in Europe – this ground-breaking project pushes the envelope for similar large renovation projects in the future that are looking to decarbonize their heating systems - the customer is very happy with the end result.” Panasonic system lowers the carbon footprint The Panasonic system has lowered the carbon footprint of the property The Panasonic system has lowered the carbon footprint of the property and is highly energy efficient to run with little impact on the interior pipework and space within the building. The units are located on the roof to ensure they are discreet, quiet and unobtrusive to the surrounding area, having very little impact on the day to day running of the building during installation. A construction of support spreader beams and plates was designed to distribute the load within the tolerance of the roof area. University of West London pleased with the results Claire Willits, the Director of Property Services at the University of West London (UWL) said, “The University of West London has been very pleased with the results of the project and having now been through our first winter running on the new systems we can safely say the technology works!” Claire Willits adds, “This project has made a significant contribution in our carbon reduction journey and has given us reassurance that change for the better of the environment can also be cost-effective and deliver a practical operational solution.” Exceptional energy savings It is estimated that Paragon House will receive energy savings in the region of 1,058,000 kWh per year It is estimated that Paragon House will receive energy savings in the region of 1,058,000 kWh per year. Considering the other two Panasonic installs at UWL, the total amount of energy saving is expected to be in excess of 500 tons of CO2 per annum. The above project was recently announced as the award winner of the National Renewable Heat Project of the Year at the Energy Efficiency Awards 2022. Seamless design and installation Harvey Loyal, Specification Sales London for Panasonic, stated “The control of the 210kW units were new to the market when Finn Geotherm came to us with the project – we worked with the wider Panasonic technical team and Finn Geotherm to provide a seamless design and installation.” Harvey Loyal adds, “As this was a European first and so for peace of mind, the original boilers were kept as a back-up should the outside temperatures reach -5 degree or lower. 12 months following the installation, Paragon House has confirmed the boiler system has not once been utilized and the heating produced from the Panasonic Air-to-Water system fully meets the heating requirements of the building.” Since the initial installation of Panasonic air source heat pumps at Paragon House, Finn Geotherm has installed similar Panasonic systems in several other similar buildings across UWL, as well as many other large projects in and around the London area.
In line with the UK’s Net-Zero targets, local governments are transitioning communities to a greener future. Kemsley Community Centre, based in Sittingbourne, Kent, United Kingdom (UK) were looking for a more energy efficient and sustainable system to heat and cool their large and multiple areas of the community center, in order to replace a 1960’s oil-fired system. Phoenix ACR, specialists in AC and refrigeration, specified a Panasonic R32 split system with 4 x 20kW PACi outdoor units and 11 of the Panasonic PACi NX Elite range of wall mounted indoor units with nanoe X. Panasonic R32 split system installed The new system needed to meet the needs of the entire community center, covering the main hall, bar area and reception area. Each section required units suited to the individual area, which could seamlessly combine and function under a single control system. The Panasonic PACi NX Elite range was specified by installer, Nathan Bell, the Managing Director of Phoenix ACR, who explains “We have worked with Panasonic a lot in the past, so we knew its range was the best to deliver the efficiency, reliability and value for money that was key to this installation. The energy-saving design and high efficiency makes the Panasonic units ideal for this project.” Panasonic PACi NX Elite wall mounted indoor units The PACi NX Elite range allows a great amount of flexibility in design and install The PACi NX Elite range allows a great amount of flexibility in design and install, which was crucial to ensuring we could adapt to the needs of each room, providing the perfect solution for the customer. The addition of nanoe X technology, which inhibits viruses and bacteria, was a key benefit of the Panasonic units, to help provide a better indoor environment for the community center staff and its users in a post-pandemic world.” Featuring nanoe X technology In the main hall and bar area, 11 Panasonic PACi NX Elite wall-mounted units with nanoe X technology were installed. These are especially beneficial for high ceiling areas, such as found in the community center. The reception area has two PACi ceiling suspended units, with the slim design making them more discreet for the smaller room, along with being one of the quietest units currently on the market. Facilities Trustee of Kemsley Community Centre, David Grawler, said “It is so important that we provide a sustainable future for our community. Phoenix ACR recommended this solution, and we are very happy with how it meets our energy efficiency needs. With our old system, if we hired out a single room, we would end up having to heat the entire building.” David Grawler adds, “The new Panasonic system allows us to control all units as one for the entire building, but also enables us isolate the individual spaces, adding a new way for us to function in a more energy efficient way, without having to compromise on comfort.” PACi NX Standard and PACi NX Elite ranges The PACi NX Standard and PACi NX Elite ranges provide high quality heating and cooling The PACi NX Standard and PACi NX Elite ranges provide high quality heating and cooling, boasting top class SEER ratings of A++ and SCOP ratings of A+ and A++ at 10kW respectively. Both provide slim, lightweight and compact designs. The PACi Elite offers greater design flexibility, making it adaptable to various building types and sizes, key to delivering the perfect solution across larger projects. The design allows for high quality under a wide range of conditions, with cooling possible in temperatures as lows as -15 degrees or as high as 46 degrees, and heating in temperatures as low as -20 degrees. Kemsley Community Centre Kemsley Community Centre has a touch screen centralized controller installed behind the bar, allowing the management of the entire system from a single point. Additionally, the system utilizes WIFI adaptors which connect the units to the Panasonic comfort cloud App, allowing for remote management and monitoring of the multiple air conditioning units required for this project. The units came with nanoe X technology as standard, a unique and proven technology to help improve air hygiene by preventing transmission of airborne pathogens, to create a safer and healthier indoor environment. Nanoe X works independently from the heating and cooling operation when the unit is in fan mode, improving protection 24 hours a day, 7 days a week. Panasonic units – a great addition to the community center David Gawler concludes, “The Panasonic units have proven to be a great addition to the community center, they helped us cope during the summer heat wave of 2022, and heating capabilities this winter. It is great that we can still provide comfort in the center to all those who use it whilst also taking a big step to a greener future.”
When they are one of the largest beverage distributors in the U.S., it’s crucial to stay ahead of the curve on everything that drives customer satisfaction, corporate responsibility, and a strong bottom line. Hensley Beverage Company did exactly that when it collaborated with Chemours and American Refrigeration Supplies, Inc. (ARS) to implement a system utilizing a new-generation A2L refrigerant, Chemours Opteon™ XL20 (R-454C). Completed in 2023, the installation paves the way for companies throughout the commercial refrigeration industry to embrace refrigerant technologies that are both cost-effective and environmentally sustainable. Situation The company recently ended an acquisition that grew its distribution footprint into New Mexico Hensley Beverage, a Phoenix-based beverage wholesaler, supports a customer base of more than 9,000 accounts and more than 2,500 individual products, operating out of six locations across Arizona. The company recently completed an acquisition that expanded its distribution footprint into New Mexico, making it one of the largest family-owned and operated beverage distributors in the nation. As it grows, Hensley remains committed to maintaining exceptional product integrity, upholding its multi-generational family business legacy, and supporting a variety of environmental objectives. These factors, coupled with the current regulatory landscape (notably, the phasedown of legacy hydrofluorocarbon (HFC) refrigerants), have put Hensley’s focus on ways to upgrade its refrigeration systems. Phasedown of HFC refrigerants For the past several years, Chemours, ARS, and Hensley have worked together to retrofit the distributor’s existing R-22 and R-404A systems to Opteon™ XP40 (R-449A), a hydrofluoroolefin (HFO) blend offering zero ozone depletion potential (ODP) and a significantly lower global warming potential (GWP) than legacy products. However, with the ongoing phasedown of HFC refrigerants under the U.S. EPA’s American Innovation and Manufacturing Act (AIM), the teams began weighing the benefits of an even bolder upgrade. “Hensley Beverage is proud to partner with Chemours, TBSI, and ARS to help develop innovative solutions and responsible business practices that drive sustainability in our community. These groundbreaking results are a culmination of partnership and collaboration. It is refreshing to work with three organizations that are this passionate about developing pioneering products that will help shape a better future for the communities we serve,” Alex Dunn SVP of Operations, Hensley Beverage. Solution Chemours recommended bringing Opteon™ XL20 (R-454C) into Hensley’s refrigeration plan Even as Chemours, ARS, and Hensley continued to strategically employ retrofit solutions in some areas, they explored options that would put the company in a stronger position for the long term. Chemours recommended bringing Opteon™ XL20 (R-454C) into Hensley’s refrigeration plan. A mildly flammable refrigerant with an ASHRAE A2L safety classification, Opteon™ XL20 is designed for use in new equipment, so Hensley identified an old R-22 system near the end of its life that was ideal for replacement by a new system using Opteon™. Opteon™ XL20 has been used for several years in Europe and is expected to become the new norm in the U.S. by 2026, based on the current direction provided by the EPA. Leveraging its experience in Europe, the Chemours team of technical service and business development resources is prepared to support end users as they consider trial installations using A2L refrigerants. Features of Opteon™ XL20 Opteon™ XL20—the future of sustainable low- and medium-temperature refrigeration GWP of 148 (a 96% reduction versus R-404A) Zero ODP Enables much higher charge sizes than highly flammable A3 refrigerants Is a close performance match to R-22 and R-404A Offers the optimum balance of performance and environmental sustainability Provides an easy, cost-effective alternative to legacy refrigerants in new equipment applications Utilizes well-known technology for ease of service and maintenance Benefits of HFOs Hensley was an early adopter of Opteon™ XP40, retrofitting equipment to experience better “Hensley was an early adopter of Opteon™ XP40, retrofitting equipment to experience better environmental outcomes, as well as high performance in low- and medium-temperature applications. Experiencing these benefits of HFOs whet their appetite to ask, ‘What next?’ With a strong dedication to supporting their communities and the environment while operating an efficient and thriving business, Hensley is a company that pushes the envelope." "Chemours was ready with our next-generation Opteon™ XL20—that will ensure they achieve maximum performance, operating efficiency, and sustainability," Joe Martinko President, Thermal and Specialized Solutions, Chemours. New low GWP refrigerant “Our industry is undergoing some of the most significant regulatory changes in history and will be for the foreseeable future. ARS was excited to work with Chemours and be a part of the launch at Hensley of the new low GWP refrigerant." "It’s been a privilege for ARS to help bring together such an excellent group of partners for this project—and to install a first-of-its-kind system right here in Tucson, a community we’ve proudly served since 1948,” John White President, American Refrigeration Supplies, Inc. Opteon™ XL20 properties ASHRAE Number: R-454C Composition Weight%: R-32/R-1234yf 21.5/78.5 Molecular Weight: 90.8 g/mol Normal Boiling Point: -45.6 °C (-50.0 °F) Critical Pressure: 4318.9 kPa (626.4 psia) Critical Temperature: 85.7 °C (186.2 °F) Liquid Density at 21.1 °C (70 °F): 1058.2 kg/m³ (66.1 lb/ft³) Ozone Depletion Potential (CFC-11 = 1.0): 0 AR4 (AR5) GWP (CO₂ = 1.0): 148 (146) ASHRAE Safety Classification: A2L Temperature Glide: ~6 K (~10.8 R) LFL (UL 60335 2-89 WCF): 0.291 kg/m³ (0.018 lb/ft³). Collaboration and Installation The installation brought together additional resources from the HVACR industry, including Copeland and Heatcraft Refrigeration Products— two ARS manufacturing partners—as well as Technical Building Services, Inc. (TBSI), the local HVACR service provider. As HVACR technology providers helping customers achieve their sustainability, decarbonization, and regulatory compliance goals, Heatcraft and Copeland had the knowledge and experience of emerging A2L requirements and the capabilities to support the project. TBSI was selected as the contractor for installation and servicing. Use of R-22 in other Hensley systems Installation, evacuation, and setting methods were very similar to the recent refrigerants With the team assembled, Chemours took the lead on the project, ensuring that the contractor, Hensley’s service personnel, and others involved were certified through the ESCO Institute’s A2L refrigerant training program, and answering any questions from the local authorities. After safely recovering the R-22 for use in other Hensley systems, the team from TBSI started removing the existing Keg 6 equipment, hanging new evaporator coils, and running new refrigerant lines. Installation, evacuation, and charging procedures were very similar to the current refrigerants in use by industry, making for a time- and cost-efficient process. Next generation of climate technology “Copeland has always been focused on not just setting the standard in climate solutions with pioneering brands in compression, controls, software, and monitoring—but pioneering the evolution in this space. Our role in the system design and installation for Hensley was right in our wheelhouse. What we accomplished together demonstrates that by bringing together energy-efficient products, regulation-ready solutions, and expertise, we can revolutionize the next generation of climate technology for the better,” Brian Schroeder Engineering Manager, Refrigerants, Copeland. “Our tools and gauges were already enabled for the R-454C refrigerant. The startup and charging of both systems went pretty smoothly. TBSI is proud to have participated in the project at Hensley and, by doing so, adding to the variety of equipment we’ve worked on since founding our business in 1990. This was a great opportunity to grow our experience with A2Ls,” Sergio Pelayo Vice President, TBSI. Copeland monitoring data Copeland applied monitoring units to the systems that capture nearly two dozen data points every second To make sure the system performed as expected, Copeland applied monitoring units to the systems that capture nearly two dozen data points every second. The data has shown that the systems are running as designed. “We are thrilled with the results of the R-454C project with Hensley Beverage. As we continue our journey toward new regulation compliance, this successful collaboration has been instrumental in leveraging Heatcraft’s new product design efforts, with A2L refrigerants being an important part of the mix. We are poised to lead the industry and provide more customers like Hensley with cutting-edge solutions that drive their success,” Bob Landi Vice President and General Manager, Heatcraft Refrigeration Products. Summary Influenced by upcoming regulatory changes and stronger organizational ESG commitments, the commercial refrigeration industry’s transition to lower GWP refrigerants is inevitable. Opteon™ refrigerants provide organizations with lower GWP options that can help extend the useful life of their systems, as well as new equipment options that enable decades of reliable operation. Moreover, these systems answer the consumer preference for businesses that utilize responsibly manufactured products and support a greener environment. Hensley’s approach demonstrates an ideal way for companies to meet the needs of refrigerating their products while following the guidelines of the HFC phasedown. It’s important to assess where your equipment is in its lifecycle and determine if it makes the most sense in terms of budget, performance needs, and corporate vision to (1) retrofit existing equipment for more efficient and sustainable operation or (2) replace it with A2L refrigerant technologies and products.
The emphasis on sustainable processes has never been greater than in today’s marketplace. Environmental conservation must be considered in every phase of appliance design and in every step of the product lifecycle. Product designers use sustainable materials to limit carbon footprint, efficient and reliable components are chosen to reduce environmental impact during product operation, and, after the end of a product’s useful life, responsible companies must even plan for recycling and disposal. TE Connectivity’s Industrial Technology Index, a survey of global companies focused on the innovation culture of engineers and executives, showed that innovation and sustainability are business priorities for most engineers and executives alike. Sustainable practices are now being integrated early in the innovation process, providing more opportunities to limit the environmental impact of new products. Sustainable design considerations throughout the product life cycle Sustainable Design Considerations TE’s connectors play a vital role in enabling the safe, reliable and efficient interaction of a wide variety of essential components. A growing emphasis on sustainable practices has compelled the team to develop sustainable products for various types of equipment. Designs for sustainability replace virgin materials that have large carbon footprints with recycled or renewable, biological-based alternatives. Designs for sustainability replace virgin materials that have large carbon footprints Likewise, efficiency improvements during manufacturing, as well as more reliable, energy-saving connector designs, further limit the environmental footprint of these products. TE’s cluster block products, used for compressor applications like air conditioners, heat pumps, and refrigerators, have been redesigned with this sustainability in mind. These innovative products will help enhance the reliability of compressors, while reducing energy consumption and minimizing carbon footprint. Enhanced Safety, Performance and Productivity Reducing the temperature of connectors in operation results in less wasted energy. This can improve the performance of the compressor which translates to better appliance efficiency. The sustainable cluster block achieves this goal with an additional contact beam, shown in Figure 2, that minimizes electrical contact resistance, optimizing the energy transmission, reducing temperature rise and providing the required connection. Additionally, the innovative lead-in alignment feature, illustrated in Figure 3, helps to error-proof the connection, improving safety as well as productivity of automated assembly processes. The sustainable cluster block achieves this goal with an additional contact beam Potential health hazards The cluster block uses a renewable, plant-based material (Figure 4) that can be sustainably produced with minimal impact to the environment. This high-performance material meets the stringent International Electrical Code (IEC) with flammability ratings tested to UL 94 V-0, CTI 600V and GWEPT 750°C (1380°F) no flame requirements. Made up of 50% castor bean oil, the material is halogen-free which further limits the potential environmental impact. This material reduces the carbon footprint by more than 45% during production, use and disposal while also eliminating potential health hazards. Conversion of renewable, plant-based material into halogen-free, flame-resistant resin for the cluster block housing Minimizing environmental impact TE’s new cluster block (Figure 5) was designed to minimize environmental impact by reducing consumption of natural resources, minimizing waste and promoting renewable energy. To mitigate climate change, the cluster block connector features 19% lower plastic usage and 26% lower metal usage, when compared to legacy connectors (Figure 6). The cluster block connector features 19% lower plastic usage and 26% lower metal usage The sustainable cluster block will help TE contribute to maximizing the safety, performance and sustainability of compressor applications. This technology is a key step in meeting the growing demand for cost effective, environmentally friendly solutions that are compatible with modern automated assembly processes. As the appliance industry continues to evolve, sustainable connector designs will undoubtedly play a key role in shaping the future of compressor applications and beyond.
Tarkett’s vinyl flooring factory in Ronneby, Sweden, is using ABB data insights and service expertise to save 800 megawatt-hours (MWh) of energy per year from their motor-driven systems. This is around 1 percent of the site’s total energy consumption in a year and is equivalent to the energy needed to charge 68 million smartphones for the same amount of time. ABB Ability™ Digital Powertrain Energy Appraisal solution With the current energy prices, the payback period would be only 18 months or less With the data gathered through the ABB Ability™ Digital Powertrain Energy Appraisal solution, ABB identified that upgrading 10 motors to IE5 SynRM technology would boost efficiency from 80 percent to 95 percent. With the current energy prices, the payback period would be only 18 months or less. The service is underpinning Tarkett’s wider strategy to deploy innovative technology and act sustainably in its operations. Upgrading motors to ensure energy efficiency “The biggest lesson for us is that we’ve been maintaining motors that we should have exchanged years ago. We are really impressed by the savings obtained by just upgrading 10 of our motors to more efficient ones,” says Ted Evaldsson, Tarkett’s Supervisor Electrical Maintenance. Having seen the positive results, Tarkett is now planning to further connect additional motors with ABB digital services to yield greater energy savings at Ronneby in 2023, with the help of the digital energy audit. Tarkett extends the coverage of monitored assets By extending the coverage of monitored assets, Tarkett will be better positioned to constantly identify and prioritize energy-saving opportunities at a larger scale, while also saving considerably in CO2 emissions.


Products

From A To L: Your A2L Transition Guide
Download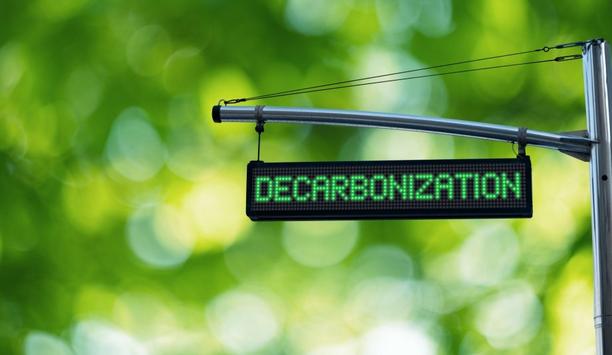
Leveraging Radiant And Hydronics To Help Achieve Decarbonization Goals
Download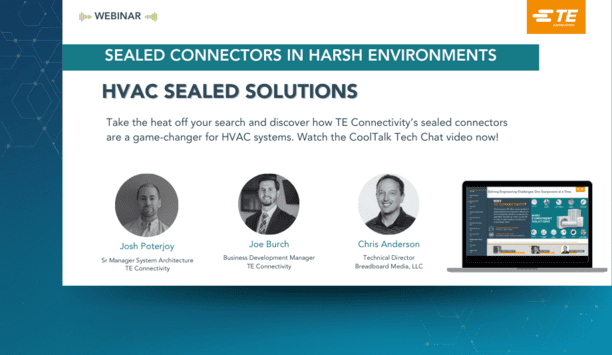
Sealed Connectors In Harsh Environments
Download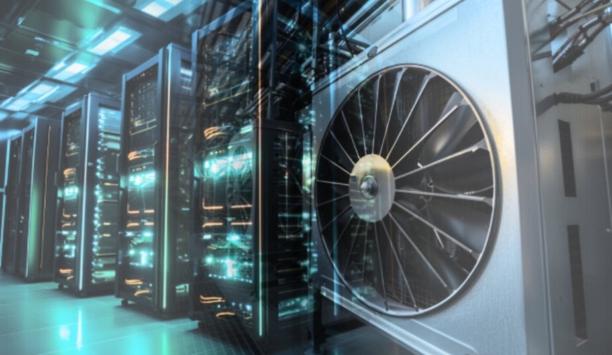
Powering And Cooling Next Generation Data Centers
Download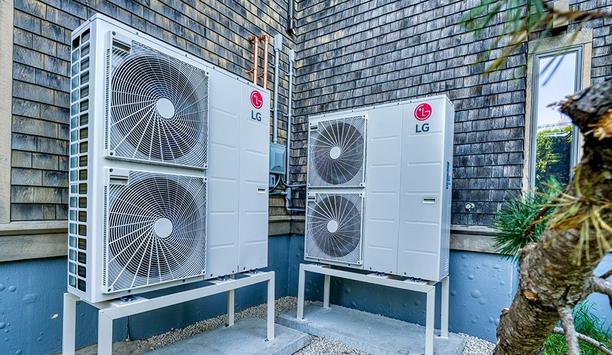
Debunking Myths To Promote A Bright Future For Heat Pumps
Download