Capacity
As demand continues to grow for sustainable, energy-efficient solutions in refrigeration and heating, both Europe and North America are navigating a rapid transition toward natural refrigerants. There is a strong demand for new CO2 systems, including heat pumps and various other applications. Higher capacity compressors with larger operating envelope, such as Danfoss’ Bock HGX56 CO2 T series, will play a critical role in supporting this growing need. Air to water heat pumps As shown in...
Modern data centers require advanced cooling solutions to operate at peak performance. As one of the most rapidly growing industries in the world, data centers are changing how they develop new cooling technology at a record pace. The data center market is projected to continue growing by 8.5% per year over the next five years, to over $600 billion by 2029. Global power demand by 2028 Artificial intelligence (AI) and machine learning (ML) are driving increased data center demand, and the...
A survey conducted by Baxi of 200 state school estate managers, consultant engineers, and M&E contractors has found that while enthusiasm for net zero and support for low-carbon heating systems in schools is thriving, persistent barriers remain. The survey found extremely strong support for net zero within schools, with 90% of estates managers who responded agreeing that net zero is a priority, a sentiment echoed by 78% of consultant engineers and contractors. 99% of the school estate manag...
Viessmann Climate Solutions (VCS) has combined with Carrier to become the core of Carrier’s newly formed business unit Residential and Light Commercial for European, Middle East and Africa. This business unit is now able to offer brands like Carrier, Toshiba, and Beretta next to the premium brand Viessmann, thus covering additional user segments with differentiated products at various price points. Climate system technology “The climate system technology of Viessmann Climate Solu...
Does anyone still think that heat pump technologies for residential applications are ineffective in cold climates? If so, they are missing opportunities available through advancements in heat pump technology. New developments in heat pumps are significantly transforming the residential HVAC market. These advanced heat pumps can maintain 100% heating capacity at 0 degrees F and operate efficiently at low temperatures. Secondary heat sources These capabilities reduce the need for secondary hea...
Two Tyneham 290HT 27kW air source heat pumps from Hamworthy Heating – a trusted British manufacturer and supplier of commercial heating and hot water products – have been installed in cascade for underfloor heating in a new extension at a primary school in Cambridge. To accurately meet the heating requirements of the new school extension and ensure an even distribution of heat, the new system from Hamworthy Heating includes two 290HT 27kW Tyneham heat pumps with natural refrigerant,...
News
A-Gas, a world pioneer in environmentally responsible lifecycle refrigerant and fire suppressant management, acquired Refrigerant Services Inc. (RSI), a recognized brand in the Canadian refrigerant industry. The acquisition, finalized in late March 2025, further solidifies A-Gas' position as a world pioneer in the supply and lifecycle management of refrigerants and associated products and services. Strengthening Commitment It ensures that customers receive the maximum value and benefit of lifecycle refrigerant management This acquisition aligns with A-Gas' commitment to delivering enhanced refrigerant solutions and support to businesses across North America. It also ensures that customers in the Canadian market receive the maximum value and benefit of lifecycle refrigerant management while maintaining access to a full range of products and services. "We are thrilled to welcome Refrigerant Services Inc. to A-Gas," said Mike Armstrong, Managing Director and President of A-Gas in the Americas. “We are excited to continue serving the Canadian market, combining our expertise to provide circular solutions in the refrigerant industry with RSI’s over thirty years of exceptional customer service and dedication to the Canadian market. We look forward to delivering the same dedication and expertise that has defined both companies." Strengthening Innovation "We are excited to join forces with A-Gas, as their global expertise and resources will significantly enhance our ability to serve the Canadian market," said Jim Thomas , President of Refrigerant Services Inc. "Together, we will continue to innovate and provide environmentally responsible refrigerant management solutions that meet the evolving needs of our customers." Enhanced Refrigerant Solutions Both companies' merger and brands will remain intact, ensuring continuity and familiarity for existing customers. This strategic move allows A-Gas to leverage the strengths of both organizations, combining their expertise to better serve the evolving needs of the Canadian refrigerant market. A-Gas, with the support of its co-investors TPG Rise Climate and KKR, continues to strengthen its position as a world pioneer in the supply and lifecycle management of refrigerants and associated products and services. With this latest acquisition, A-Gas is poised to deliver enhanced solutions and support to businesses across Canada, furthering its goal of promoting environmentally conscious and circular practices in the refrigerant industry. Expert Consultancy A-Gas received legal advisory services from Stikeman Elliott LLP, financial advisory services from PricewaterhouseCoopers LLP and environmental support from Stantec Consulting Ltd.
Trane Technologies a global climate innovator, is revolutionizing mission critical operations with the development of two new air-cooled chiller offerings – Magnetic Bearing chillers and Ascend chillers for facility chilled water-cooling applications. Trane’s Magnetic Bearing Chiller provides unparalleled cooling capacity to address the escalating capacity needs of data center thermal management systems. Introduction of the Ascend chiller platform for data centers provides even greater efficiency for high ambient temperature operations. Advanced Thermal Solutions “Next-gen microprocessors are expected to exponentially increase rack density, elevating demand for efficient, higher capacity and higher ambient air-cooled chillers,” said Steve Obstein, Vice President and General Manager, Data Centers & High-Tech, Trane Technologies. “Building on our leading platforms, in close collaboration with our customers, gives us the ability to redefine the standards of cooling efficiency, capacity, and environmental sustainability for data center owners and operators, helping them stay ahead of rapidly advancing thermal management needs.” Maximize Cooling Capacity with a Reduced Footprint The new chiller helps maximize cooling capacity per square foot of unit footprint The new air-cooled chiller, based on Trane’s proven Magnetic Bearing compressor platform, produces up to 850 tons, 3MW at data center conditions on a single unit frame. The new chiller helps maximize cooling capacity per square foot of unit footprint, often allowing for a reduction in the number of chillers needed onsite and helping to enable lower installation costs. Replacing multiple chillers with a single larger capacity chiller can help reduce sound transmission to the local environment, helping reduce the impact in sound sensitive locations. Higher Ambient Temperature Operations Through the extended capabilities of the Ascend screw-compressor chiller platform, Trane is leading with solutions that meet customer needs to address escalating ambient temperatures from greater heat density generated by modern GPUs and AI adoption. Expansion of the Trane Ascend Air-Cooled Chiller with integrated indirect free cooling, supports data center uptime with efficient operation at up to 145F. Free cooling reduces reliance on mechanical cooling, and helps reduce energy consumption and operational costs. Designed for Higher Efficiency and Serviceability The new air-cooled chillers use refrigerants with lower global warming potential, supporting reduced energy costs and carbon footprints. Both chillers are equipped with Trane’s Symbio 800 unit controller with AdaptiView user interface, offering secure enhanced connectivity, flexibility, and serviceability. Trane supports operations and uptime throughout the lifecycle of the data center with thousands of local service experts across North America, strategically located in proximity to customers, and Smart Service options for proactive monitoring, predictive maintenance, and improved thermal management systems.
Pfannenberg, Inc., a pioneering manufacturer of thermal management and signaling technologies, proudly announces the DHS Hybrid Series (DHS 34X1). By combining free cooling with active cooling, this closed-loop system safeguards critical electronics within an enclosure while lowering energy consumption, cutting costs, and reducing carbon emissions. Free cooling with active cooling DHS-Series achieves its optimal efficiency by combining free cooling with active cooling “The DHS-Series combines the best of free cooling and active cooling to radically impact an end-user's energy consumption and carbon emissions while cooling their critical electronics,” says James Wong, Pfannenberg’s Director of Global NEMA Product Management. The DHS-Series achieves its optimal efficiency by combining free cooling with active cooling. Free cooling is a technology that minimizes energy use by using the cooler air outside the enclosure to remove heat from inside the enclosure. Efficiency of the cooling unit Active cooling utilizes a compressor and refrigerant cycle to cool the air in the enclosure when it exceeds the desired temperature of the enclosure. This combination optimizes the efficiency of the cooling unit, thereby reducing energy usage. This dual system also provides redundancy in a single unit to avoid downtime, fits all full-sized enclosures, and also features an easy-to-read status display. Warehouse automation The product proves ideal for locations with lower ambient temperatures The DHS-Series is offered in indoor (Type 12), outdoor (Type 3R/4), and in washdown (Type 4X) configurations. The product proves ideal for locations with lower ambient temperatures, climate-controlled facilities, and operations that periodically run at partial capacity. This can include everything from automotive manufacturing and warehouse automation to outdoor facilities and food and beverage manufacturing. DHS-Series UL 60335 standard The DHS-Series meets high standards for electrical safety, being certified to the UL 60335 standard. Additionally, the hybrid cooler is pre-gasketed to make installation even easier. The product has also been designed to meet upcoming environmental regulations governing the use of the R-513A refrigerant.
Quilt, a pioneering innovator in smart home climate technology, announced that Matt Rogers, CEO and co-founder of Mill, co-founder of Nest, and founder of Incite, has joined its board of directors. A prominent figure in the smart home, design, and climate space, Rogers is widely respected for creating the iconic smart thermostat and for accelerating growth for mission-driven organizations. Quilt's growth and innovation Quilt, Nest and Mill are among the most successful startups in the smart home space, and Rogersʼ deep expertise in product development, business scaling, and partnership building will be instrumental in driving Quilt's continued growth and innovation. Since launching in the Bay Area in May 2024, Quilt has quickly emerged as an industry pioneer, selling through its entire 2024 installation capacity shortly after its debut, and earning Energy Star recognition as the most efficient two-zone heat pump on the market. Adoption of smart home technology Quilt is poised to roll out industry-defining features and will expand its extreme smart heat pump Following such exceptional demand and recognition, Quilt is poised to roll out industry-defining features and will expand its revolutionary smart heat pump to new markets across the country in 2025. Rogersʼ appointment underscores the growing mainstream adoption of smart home technology, with intuitive and elegantly designed systems like Quilt heralding a future where sustainable living is both responsible and highly desirable. Modern home comfort to new markets "Matt has been an invaluable advisor to Quilt since our earliest days, and we are thrilled to officially welcome him to our board," said Paul Lambert, CEO of Quilt. "His deep industry expertise, proven business acumen, and collaborative spirit will be instrumental as we scale and bring our vision for modern home comfort to new markets nationwide." Incredible technology and people-centric approach “Quilt has developed technology that will change what is possible with smart climate control inside our homes. It gives people the ability to manage heating and cooling in a way thatʼs intuitive, effortless and cost-effective. Not only is this a better experience in your home, itʼs better for the planet too." "I love this combination of incredible technology and a people-centric approach. I am excited to join the board and continue to support Quiltʼs vision for the future,ˮ Matt Rogers, CEO, Co-Founder of Mill and Founder of Incite.
The Plumbing and Heating Federation (SNIPEF) has raised concerns that the Scottish Government’s announcement on a revised Heat in Buildings Bill failed to address the core challenge of how decarbonization will be delivered, with no mention of workforce skills, installer training or targeted support for small and medium-sized businesses (SME’s). This support is crucial, as 80% of heat pump installations are expected to be completed by SME’s. How Scotland will develop the skilled workforce While welcoming the move to more realistic long-term targets and a renewed focus on fuel poverty, SNIPEF said the announcement lacked critical detail on how Scotland will develop the skilled workforce and business capacity required to install low-carbon heating at scale. Fiona Hodgson, Chief Executive of SNIPEF, said: “We support the Government’s intention to move away from immediate restrictions on homeowners and instead focus on national targets. That change of tone is constructive and gives the plumbing and heating profession a clearer signal on the direction of travel." Rising apprenticeship costs SNIPEF represents over 700 member firms using more than 3,500 plumbing and heating experts Hodgson added: “But today’s announcement is silent on how the work will actually get done. There is no reference to skills, vocational training or business support; yet these are the foundations on which success depends. Without them, we risk setting targets that are simply undeliverable.” SNIPEF, which represents over 700 member firms employing more than 3,500 plumbing and heating professionals, also highlighted the financial strain facing smaller businesses, particularly in relation to rising apprenticeship costs following the significant increase in minimum apprentice wage rates. Policy measures The Federation is calling on the Scottish Government to ensure that the forthcoming Bill and accompanying policy measures include: Dedicated and accessible funding for SMEs to support upskilling and investment in low-carbon technologies Increased investment in apprenticeships and vocational education to grow a future-ready workforce Clear, stable policy direction that enables businesses to plan and invest with confidence. Skills, training, and SME capacity “Around 80% of our members still work in the traditional heating market,” Hodgson added. “They are willing to play a key role in Scotland’s transition, but they can’t do that without practical support. Skills, training and SME capacity must be at the heart of the next stage." “Apprenticeship funding has remained stagnant for over eight years, placing additional financial strain on small businesses already managing rising employer National Insurance contributions, increased minimum wage rates and growing operational costs. These pressures are real, and without targeted intervention, they risk choking off the very workforce we need to deliver change.”
The power grid is undergoing a transformation to keep pace with the rising energy demands of our modern era. This shift is driven by major trends such as the electrification of transportation and HVAC systems, as well as the rapid expansion of AI and renewable energy. Smart Grid The goal is to evolve the traditional electric infrastructure into a more advanced To enhance capacity, resilience, and adaptability, the goal is to evolve the traditional electric infrastructure into a more advanced "Smart Grid." This modernization takes inspiration from Industry 4.0, which leverages tools such as sensors, IoT, and data analytics, to revolutionize operational efficiency across all sectors of the economy. The cornerstone of this digital ecosystem is the intelligence it brings to grid operations, offering valuable insights and actionable data. It enables real-time asset health monitoring and supports proactive, condition-based maintenance. By identifying potential issues early, operators can implement predictive strategies—such as refilling gas or replacing O-rings—before failures occur. This condition-driven approach addresses problems based on the actual state of equipment, reducing the risk of unexpected breakdowns, lowering the need for expensive emergency repairs, and extending the lifespan of critical, high-value assets. The Role of Advanced Gas Density Sensors A key enabler of this transformation is the adoption of advanced gas density sensors in gas-insulated switchgear (GIS). Since the 1980s, GIS has become widely popular due to its compact design, excellent reliability, and ability to handle higher voltage levels efficiently. High-voltage switchgear has evolved significantly—from the bulky air-insulated switchgear (AIS), which occupied the size of a football field, to GIS systems that require just 10% of that space. This innovation is possible thanks to pressurized chambers filled with highly compressed insulating gas, which house the high-voltage components. This gas effectively prevents or extinguishes arc faults and short circuits, enabling more reliable and space-saving power systems. Critical Gas Density Sulfur hexafluoride is the most effective gas for insulation and arc extinguishing at high voltages Sulfur hexafluoride is the most effective gas for insulation and arc extinguishing at high and extra-high voltages. However, SF6 has a greenhouse gas effect 23,500 times greater than CO2, making even small leaks unacceptable. For this reason, strict regulations worldwide demand rigorous monitoring to prevent SF6 from escaping. Effectively monitoring insulating gas density is more critical than ever for ensuring the reliability and safety of gas-insulated high-voltage systems. Maintaining proper gas density within pressure compartments is essential to prevent functionality issues, safety risks, and environmental violations caused by leaks. This is also critical as the industry explores less environmentally harmful alternatives to SF6, which still require precise monitoring to ensure sufficient insulating gas levels are maintained. Predictive Maintenance Utilities now face dual challenges: operating plants without interruptions and reducing plant sizes. This has led to a shift toward continuous electronic density monitoring and predictive maintenance over traditional warning and shutdown systems. As smaller compartments with reduced insulation volumes become the norm, tighter gas monitoring is essential. Traditional Gas Density Monitoring Pressure gauges, using Bourdon tubes and bimetallic temperature compensation, were once standard for monitoring systems. While cost-effective, they are less precise due to design limitations. Gas density is typically inferred from pressure using manometers or sensors, but significant temperature variations in closed systems lead to inaccuracies without proper compensation. In a closed, gas-insulated system, the number of gas molecules (density) remains constant, but pressure and temperature vary based on isochores. Outdoor installations face temperature extremes from -40°C to +60°C, requiring precise temperature compensation to avoid false readings. Without this, sunlight or frost can cause density displays to fluctuate, even when the actual gas density remains unchanged. Extreme Condition Challenges Outdoor installations are an increasing share of gas-insulated switchgear (GIS) setups due to the rapid growth of renewable energy projects and the rising need to support bulk power transfers across long distances. Bimetallic temperature compensation must be tailored to the insulating gas, but large temperature fluctuations can lead to significant measurement inaccuracies. At extreme temperatures, these inaccuracies increase further, resulting in false alarms. Reliable gas density monitors must withstand harsh conditions, function across varying altitudes and pressures, and ensure continuous, accurate measurements. Breakthrough in Accuracy Traditional temperature-compensated pressure gauges fell short when it came to reliable gas density monitoring, often lacking the precision needed and leading to false alarms. To address this, Trafag AG, in collaboration with switchgear manufacturers, revolutionized the field in 1987 with the introduction of an innovative reference chamber system. This advancement significantly outperformed conventional manometer-based designs, offering greater accuracy and reducing the occurrence of false alerts. Unlike conventional density gauges, Trafag’s system uses a reference gas housed in an isolated reference chamber. This reference gas mirrors the properties of the insulation gas within switchgear components. Both gases are thermally coupled, maintaining identical temperatures, which eliminates pressure variations caused by temperature changes. By design, the monitors are fully temperature-compensated, delivering a level of accuracy that surpasses standard pressure gauges. Why Accuracy Matters When insulation gas pressure drops, the reference chamber system activates precise mechanical switching points via microswitches. At the first alarm level, operators are prompted to refill the insulation gas. Only a rapid and significant pressure loss triggers an automatic system shutdown, thanks to the system’s reliable secondary switching points. This high level of accuracy has significant benefits. Density monitors designed with narrow alarm thresholds enable more compact and efficient plant designs. With greater measurement precision, insulation volumes can be reduced, allowing for smaller, optimized systems. This minimizes the site area required for switchgear installations. In contrast, less accurate density monitoring necessitates larger volumes and broader tolerances, resulting in bulkier, less efficient designs. Continuous Monitoring Gas monitors have improved measurement accuracy by reducing temperature distortions Gas monitors with reference chamber designs have significantly improved measurement accuracy by reducing temperature-related distortions. But these systems have inherent limitations. They only provide precise readings at specific moments, triggered when pressure crosses a microswitch threshold, providing only intermittent data points. This limitation leaves gaps in system visibility, requiring engineers to rely on data interpolation or trend extrapolation to evaluate and predict system performance. As the power distribution industry increasingly relies on real-time, high-resolution data for advanced analytics and preventative maintenance, the need for continuous monitoring has become crucial. To address this challenge, a significant breakthrough emerged in the mid-1990s with the introduction of Trafag's electronic density sensor. Accurate Gas Measurement This innovation utilized quartz tuning fork technology—a method commonly used in timekeeping devices—to enable continuous, drift-free gas density measurement. By measuring changes in resonant frequency as the tuning fork oscillates within the gas, this technology provides continuous, real-time monitoring. The density sensors are mounted to the pressure compartment via a customizable process connection, ensuring equilibrium between the insulating gas in the compartment and the sensor's measurement chamber. The system uses two quartz oscillators: one in a vacuum and the other surrounded by the insulating gas. By comparing their resonant frequencies, the sensor determines the gas density with exceptional accuracy. Density Detection Gases of different densities alter the predetermined resonant frequency of the quartz tuning fork surrounded by the process gas. This shift in frequency is proportional to the gas density, with a response time of less than 10 milliseconds—ideal for detecting rapid density changes. Additionally, a built-in temperature sensor refines the measurement for even greater reliability. Condition-Based Preventive Maintenance Digital gas density sensors with continuous monitoring capabilities enable the shift from traditional time-based preventive maintenance to a more efficient, condition-driven approach. Time-Based Maintenance: Maintenance has traditionally been scheduled based on factors such as material aging and the environmental conditions in which equipment operates. This approach aims to prevent failures by servicing or replacing parts at set intervals. However, it often leads to unnecessary replacements and increased costs, as components may not always require maintenance when scheduled. Efficient Upkeep Condition-Based Maintenance: In contrast, condition-based maintenance is based on the actual, real-time state of the equipment. By monitoring the condition of components, this strategy identifies which parts require attention, allowing operators to perform maintenance only when wear or degradation is detected. This targeted approach not only reduces unnecessary downtime but also extends the lifespan of components by addressing issues before they escalate into major failures. It represents a more efficient and cost-effective way to manage equipment. Predictive Insights With the implementation of continuous monitoring, operators gain a comprehensive and accurate understanding of the gas's current state and its evolution over time. The sensors provide high resolution data that can be analyzed to spot trends, enabling predictive maintenance and more informed decision-making. Preparing for the Future The shift toward a smarter, more intelligent grid, coupled with condition-based maintenance, represents a gradual evolution rather than a sudden revolution. This transformation takes time, and systems are adapting at different speeds. However, even those in the early stages of this transition can recognize the direction the industry is heading. Given that gas-insulated switchgear typically has a lifespan of 30-40 years or more, it is prudent to future-proof infrastructure. As a result, some are turning to hybrid systems. The hybrid gas density monitor combines the advantages of a mechanical monitor with a reference gas chamber and the advanced functionalities of an electronic gas density sensor, all integrated into a compact, multi-functional device. With continuous measurement output, it is ideally suited for gas management and trend analysis systems. It also includes a local display and durable switchpoint alarm contacts for enhanced reliability. Smart Grid Integration Even if the current digital ecosystem is not fully equipped to utilize the continuous monitoring and real-time data provided by the electronic gas sensor, this technology is seamlessly embedded within the equipment. This ensures its availability for future use as grids evolve and become more compatible with smart technologies.
A-Gas, a world pioneer in environmentally responsible lifecycle refrigerant and fire suppressant management, acquired Refrigerant Services Inc. (RSI), a recognized brand in the Canadian refrigerant industry. The acquisition, finalized in late March 2025, further solidifies A-Gas' position as a world pioneer in the supply and lifecycle management of refrigerants and associated products and services. Strengthening Commitment It ensures that customers receive the maximum value and benefit of lifecycle refrigerant management This acquisition aligns with A-Gas' commitment to delivering enhanced refrigerant solutions and support to businesses across North America. It also ensures that customers in the Canadian market receive the maximum value and benefit of lifecycle refrigerant management while maintaining access to a full range of products and services. "We are thrilled to welcome Refrigerant Services Inc. to A-Gas," said Mike Armstrong, Managing Director and President of A-Gas in the Americas. “We are excited to continue serving the Canadian market, combining our expertise to provide circular solutions in the refrigerant industry with RSI’s over thirty years of exceptional customer service and dedication to the Canadian market. We look forward to delivering the same dedication and expertise that has defined both companies." Strengthening Innovation "We are excited to join forces with A-Gas, as their global expertise and resources will significantly enhance our ability to serve the Canadian market," said Jim Thomas , President of Refrigerant Services Inc. "Together, we will continue to innovate and provide environmentally responsible refrigerant management solutions that meet the evolving needs of our customers." Enhanced Refrigerant Solutions Both companies' merger and brands will remain intact, ensuring continuity and familiarity for existing customers. This strategic move allows A-Gas to leverage the strengths of both organizations, combining their expertise to better serve the evolving needs of the Canadian refrigerant market. A-Gas, with the support of its co-investors TPG Rise Climate and KKR, continues to strengthen its position as a world pioneer in the supply and lifecycle management of refrigerants and associated products and services. With this latest acquisition, A-Gas is poised to deliver enhanced solutions and support to businesses across Canada, furthering its goal of promoting environmentally conscious and circular practices in the refrigerant industry. Expert Consultancy A-Gas received legal advisory services from Stikeman Elliott LLP, financial advisory services from PricewaterhouseCoopers LLP and environmental support from Stantec Consulting Ltd.
Trane Technologies a global climate innovator, is revolutionizing mission critical operations with the development of two new air-cooled chiller offerings – Magnetic Bearing chillers and Ascend chillers for facility chilled water-cooling applications. Trane’s Magnetic Bearing Chiller provides unparalleled cooling capacity to address the escalating capacity needs of data center thermal management systems. Introduction of the Ascend chiller platform for data centers provides even greater efficiency for high ambient temperature operations. Advanced Thermal Solutions “Next-gen microprocessors are expected to exponentially increase rack density, elevating demand for efficient, higher capacity and higher ambient air-cooled chillers,” said Steve Obstein, Vice President and General Manager, Data Centers & High-Tech, Trane Technologies. “Building on our leading platforms, in close collaboration with our customers, gives us the ability to redefine the standards of cooling efficiency, capacity, and environmental sustainability for data center owners and operators, helping them stay ahead of rapidly advancing thermal management needs.” Maximize Cooling Capacity with a Reduced Footprint The new chiller helps maximize cooling capacity per square foot of unit footprint The new air-cooled chiller, based on Trane’s proven Magnetic Bearing compressor platform, produces up to 850 tons, 3MW at data center conditions on a single unit frame. The new chiller helps maximize cooling capacity per square foot of unit footprint, often allowing for a reduction in the number of chillers needed onsite and helping to enable lower installation costs. Replacing multiple chillers with a single larger capacity chiller can help reduce sound transmission to the local environment, helping reduce the impact in sound sensitive locations. Higher Ambient Temperature Operations Through the extended capabilities of the Ascend screw-compressor chiller platform, Trane is leading with solutions that meet customer needs to address escalating ambient temperatures from greater heat density generated by modern GPUs and AI adoption. Expansion of the Trane Ascend Air-Cooled Chiller with integrated indirect free cooling, supports data center uptime with efficient operation at up to 145F. Free cooling reduces reliance on mechanical cooling, and helps reduce energy consumption and operational costs. Designed for Higher Efficiency and Serviceability The new air-cooled chillers use refrigerants with lower global warming potential, supporting reduced energy costs and carbon footprints. Both chillers are equipped with Trane’s Symbio 800 unit controller with AdaptiView user interface, offering secure enhanced connectivity, flexibility, and serviceability. Trane supports operations and uptime throughout the lifecycle of the data center with thousands of local service experts across North America, strategically located in proximity to customers, and Smart Service options for proactive monitoring, predictive maintenance, and improved thermal management systems.
Pfannenberg, Inc., a pioneering manufacturer of thermal management and signaling technologies, proudly announces the DHS Hybrid Series (DHS 34X1). By combining free cooling with active cooling, this closed-loop system safeguards critical electronics within an enclosure while lowering energy consumption, cutting costs, and reducing carbon emissions. Free cooling with active cooling DHS-Series achieves its optimal efficiency by combining free cooling with active cooling “The DHS-Series combines the best of free cooling and active cooling to radically impact an end-user's energy consumption and carbon emissions while cooling their critical electronics,” says James Wong, Pfannenberg’s Director of Global NEMA Product Management. The DHS-Series achieves its optimal efficiency by combining free cooling with active cooling. Free cooling is a technology that minimizes energy use by using the cooler air outside the enclosure to remove heat from inside the enclosure. Efficiency of the cooling unit Active cooling utilizes a compressor and refrigerant cycle to cool the air in the enclosure when it exceeds the desired temperature of the enclosure. This combination optimizes the efficiency of the cooling unit, thereby reducing energy usage. This dual system also provides redundancy in a single unit to avoid downtime, fits all full-sized enclosures, and also features an easy-to-read status display. Warehouse automation The product proves ideal for locations with lower ambient temperatures The DHS-Series is offered in indoor (Type 12), outdoor (Type 3R/4), and in washdown (Type 4X) configurations. The product proves ideal for locations with lower ambient temperatures, climate-controlled facilities, and operations that periodically run at partial capacity. This can include everything from automotive manufacturing and warehouse automation to outdoor facilities and food and beverage manufacturing. DHS-Series UL 60335 standard The DHS-Series meets high standards for electrical safety, being certified to the UL 60335 standard. Additionally, the hybrid cooler is pre-gasketed to make installation even easier. The product has also been designed to meet upcoming environmental regulations governing the use of the R-513A refrigerant.
Quilt, a pioneering innovator in smart home climate technology, announced that Matt Rogers, CEO and co-founder of Mill, co-founder of Nest, and founder of Incite, has joined its board of directors. A prominent figure in the smart home, design, and climate space, Rogers is widely respected for creating the iconic smart thermostat and for accelerating growth for mission-driven organizations. Quilt's growth and innovation Quilt, Nest and Mill are among the most successful startups in the smart home space, and Rogersʼ deep expertise in product development, business scaling, and partnership building will be instrumental in driving Quilt's continued growth and innovation. Since launching in the Bay Area in May 2024, Quilt has quickly emerged as an industry pioneer, selling through its entire 2024 installation capacity shortly after its debut, and earning Energy Star recognition as the most efficient two-zone heat pump on the market. Adoption of smart home technology Quilt is poised to roll out industry-defining features and will expand its extreme smart heat pump Following such exceptional demand and recognition, Quilt is poised to roll out industry-defining features and will expand its revolutionary smart heat pump to new markets across the country in 2025. Rogersʼ appointment underscores the growing mainstream adoption of smart home technology, with intuitive and elegantly designed systems like Quilt heralding a future where sustainable living is both responsible and highly desirable. Modern home comfort to new markets "Matt has been an invaluable advisor to Quilt since our earliest days, and we are thrilled to officially welcome him to our board," said Paul Lambert, CEO of Quilt. "His deep industry expertise, proven business acumen, and collaborative spirit will be instrumental as we scale and bring our vision for modern home comfort to new markets nationwide." Incredible technology and people-centric approach “Quilt has developed technology that will change what is possible with smart climate control inside our homes. It gives people the ability to manage heating and cooling in a way thatʼs intuitive, effortless and cost-effective. Not only is this a better experience in your home, itʼs better for the planet too." "I love this combination of incredible technology and a people-centric approach. I am excited to join the board and continue to support Quiltʼs vision for the future,ˮ Matt Rogers, CEO, Co-Founder of Mill and Founder of Incite.
The Plumbing and Heating Federation (SNIPEF) has raised concerns that the Scottish Government’s announcement on a revised Heat in Buildings Bill failed to address the core challenge of how decarbonization will be delivered, with no mention of workforce skills, installer training or targeted support for small and medium-sized businesses (SME’s). This support is crucial, as 80% of heat pump installations are expected to be completed by SME’s. How Scotland will develop the skilled workforce While welcoming the move to more realistic long-term targets and a renewed focus on fuel poverty, SNIPEF said the announcement lacked critical detail on how Scotland will develop the skilled workforce and business capacity required to install low-carbon heating at scale. Fiona Hodgson, Chief Executive of SNIPEF, said: “We support the Government’s intention to move away from immediate restrictions on homeowners and instead focus on national targets. That change of tone is constructive and gives the plumbing and heating profession a clearer signal on the direction of travel." Rising apprenticeship costs SNIPEF represents over 700 member firms using more than 3,500 plumbing and heating experts Hodgson added: “But today’s announcement is silent on how the work will actually get done. There is no reference to skills, vocational training or business support; yet these are the foundations on which success depends. Without them, we risk setting targets that are simply undeliverable.” SNIPEF, which represents over 700 member firms employing more than 3,500 plumbing and heating professionals, also highlighted the financial strain facing smaller businesses, particularly in relation to rising apprenticeship costs following the significant increase in minimum apprentice wage rates. Policy measures The Federation is calling on the Scottish Government to ensure that the forthcoming Bill and accompanying policy measures include: Dedicated and accessible funding for SMEs to support upskilling and investment in low-carbon technologies Increased investment in apprenticeships and vocational education to grow a future-ready workforce Clear, stable policy direction that enables businesses to plan and invest with confidence. Skills, training, and SME capacity “Around 80% of our members still work in the traditional heating market,” Hodgson added. “They are willing to play a key role in Scotland’s transition, but they can’t do that without practical support. Skills, training and SME capacity must be at the heart of the next stage." “Apprenticeship funding has remained stagnant for over eight years, placing additional financial strain on small businesses already managing rising employer National Insurance contributions, increased minimum wage rates and growing operational costs. These pressures are real, and without targeted intervention, they risk choking off the very workforce we need to deliver change.”
The power grid is undergoing a transformation to keep pace with the rising energy demands of our modern era. This shift is driven by major trends such as the electrification of transportation and HVAC systems, as well as the rapid expansion of AI and renewable energy. Smart Grid The goal is to evolve the traditional electric infrastructure into a more advanced To enhance capacity, resilience, and adaptability, the goal is to evolve the traditional electric infrastructure into a more advanced "Smart Grid." This modernization takes inspiration from Industry 4.0, which leverages tools such as sensors, IoT, and data analytics, to revolutionize operational efficiency across all sectors of the economy. The cornerstone of this digital ecosystem is the intelligence it brings to grid operations, offering valuable insights and actionable data. It enables real-time asset health monitoring and supports proactive, condition-based maintenance. By identifying potential issues early, operators can implement predictive strategies—such as refilling gas or replacing O-rings—before failures occur. This condition-driven approach addresses problems based on the actual state of equipment, reducing the risk of unexpected breakdowns, lowering the need for expensive emergency repairs, and extending the lifespan of critical, high-value assets. The Role of Advanced Gas Density Sensors A key enabler of this transformation is the adoption of advanced gas density sensors in gas-insulated switchgear (GIS). Since the 1980s, GIS has become widely popular due to its compact design, excellent reliability, and ability to handle higher voltage levels efficiently. High-voltage switchgear has evolved significantly—from the bulky air-insulated switchgear (AIS), which occupied the size of a football field, to GIS systems that require just 10% of that space. This innovation is possible thanks to pressurized chambers filled with highly compressed insulating gas, which house the high-voltage components. This gas effectively prevents or extinguishes arc faults and short circuits, enabling more reliable and space-saving power systems. Critical Gas Density Sulfur hexafluoride is the most effective gas for insulation and arc extinguishing at high voltages Sulfur hexafluoride is the most effective gas for insulation and arc extinguishing at high and extra-high voltages. However, SF6 has a greenhouse gas effect 23,500 times greater than CO2, making even small leaks unacceptable. For this reason, strict regulations worldwide demand rigorous monitoring to prevent SF6 from escaping. Effectively monitoring insulating gas density is more critical than ever for ensuring the reliability and safety of gas-insulated high-voltage systems. Maintaining proper gas density within pressure compartments is essential to prevent functionality issues, safety risks, and environmental violations caused by leaks. This is also critical as the industry explores less environmentally harmful alternatives to SF6, which still require precise monitoring to ensure sufficient insulating gas levels are maintained. Predictive Maintenance Utilities now face dual challenges: operating plants without interruptions and reducing plant sizes. This has led to a shift toward continuous electronic density monitoring and predictive maintenance over traditional warning and shutdown systems. As smaller compartments with reduced insulation volumes become the norm, tighter gas monitoring is essential. Traditional Gas Density Monitoring Pressure gauges, using Bourdon tubes and bimetallic temperature compensation, were once standard for monitoring systems. While cost-effective, they are less precise due to design limitations. Gas density is typically inferred from pressure using manometers or sensors, but significant temperature variations in closed systems lead to inaccuracies without proper compensation. In a closed, gas-insulated system, the number of gas molecules (density) remains constant, but pressure and temperature vary based on isochores. Outdoor installations face temperature extremes from -40°C to +60°C, requiring precise temperature compensation to avoid false readings. Without this, sunlight or frost can cause density displays to fluctuate, even when the actual gas density remains unchanged. Extreme Condition Challenges Outdoor installations are an increasing share of gas-insulated switchgear (GIS) setups due to the rapid growth of renewable energy projects and the rising need to support bulk power transfers across long distances. Bimetallic temperature compensation must be tailored to the insulating gas, but large temperature fluctuations can lead to significant measurement inaccuracies. At extreme temperatures, these inaccuracies increase further, resulting in false alarms. Reliable gas density monitors must withstand harsh conditions, function across varying altitudes and pressures, and ensure continuous, accurate measurements. Breakthrough in Accuracy Traditional temperature-compensated pressure gauges fell short when it came to reliable gas density monitoring, often lacking the precision needed and leading to false alarms. To address this, Trafag AG, in collaboration with switchgear manufacturers, revolutionized the field in 1987 with the introduction of an innovative reference chamber system. This advancement significantly outperformed conventional manometer-based designs, offering greater accuracy and reducing the occurrence of false alerts. Unlike conventional density gauges, Trafag’s system uses a reference gas housed in an isolated reference chamber. This reference gas mirrors the properties of the insulation gas within switchgear components. Both gases are thermally coupled, maintaining identical temperatures, which eliminates pressure variations caused by temperature changes. By design, the monitors are fully temperature-compensated, delivering a level of accuracy that surpasses standard pressure gauges. Why Accuracy Matters When insulation gas pressure drops, the reference chamber system activates precise mechanical switching points via microswitches. At the first alarm level, operators are prompted to refill the insulation gas. Only a rapid and significant pressure loss triggers an automatic system shutdown, thanks to the system’s reliable secondary switching points. This high level of accuracy has significant benefits. Density monitors designed with narrow alarm thresholds enable more compact and efficient plant designs. With greater measurement precision, insulation volumes can be reduced, allowing for smaller, optimized systems. This minimizes the site area required for switchgear installations. In contrast, less accurate density monitoring necessitates larger volumes and broader tolerances, resulting in bulkier, less efficient designs. Continuous Monitoring Gas monitors have improved measurement accuracy by reducing temperature distortions Gas monitors with reference chamber designs have significantly improved measurement accuracy by reducing temperature-related distortions. But these systems have inherent limitations. They only provide precise readings at specific moments, triggered when pressure crosses a microswitch threshold, providing only intermittent data points. This limitation leaves gaps in system visibility, requiring engineers to rely on data interpolation or trend extrapolation to evaluate and predict system performance. As the power distribution industry increasingly relies on real-time, high-resolution data for advanced analytics and preventative maintenance, the need for continuous monitoring has become crucial. To address this challenge, a significant breakthrough emerged in the mid-1990s with the introduction of Trafag's electronic density sensor. Accurate Gas Measurement This innovation utilized quartz tuning fork technology—a method commonly used in timekeeping devices—to enable continuous, drift-free gas density measurement. By measuring changes in resonant frequency as the tuning fork oscillates within the gas, this technology provides continuous, real-time monitoring. The density sensors are mounted to the pressure compartment via a customizable process connection, ensuring equilibrium between the insulating gas in the compartment and the sensor's measurement chamber. The system uses two quartz oscillators: one in a vacuum and the other surrounded by the insulating gas. By comparing their resonant frequencies, the sensor determines the gas density with exceptional accuracy. Density Detection Gases of different densities alter the predetermined resonant frequency of the quartz tuning fork surrounded by the process gas. This shift in frequency is proportional to the gas density, with a response time of less than 10 milliseconds—ideal for detecting rapid density changes. Additionally, a built-in temperature sensor refines the measurement for even greater reliability. Condition-Based Preventive Maintenance Digital gas density sensors with continuous monitoring capabilities enable the shift from traditional time-based preventive maintenance to a more efficient, condition-driven approach. Time-Based Maintenance: Maintenance has traditionally been scheduled based on factors such as material aging and the environmental conditions in which equipment operates. This approach aims to prevent failures by servicing or replacing parts at set intervals. However, it often leads to unnecessary replacements and increased costs, as components may not always require maintenance when scheduled. Efficient Upkeep Condition-Based Maintenance: In contrast, condition-based maintenance is based on the actual, real-time state of the equipment. By monitoring the condition of components, this strategy identifies which parts require attention, allowing operators to perform maintenance only when wear or degradation is detected. This targeted approach not only reduces unnecessary downtime but also extends the lifespan of components by addressing issues before they escalate into major failures. It represents a more efficient and cost-effective way to manage equipment. Predictive Insights With the implementation of continuous monitoring, operators gain a comprehensive and accurate understanding of the gas's current state and its evolution over time. The sensors provide high resolution data that can be analyzed to spot trends, enabling predictive maintenance and more informed decision-making. Preparing for the Future The shift toward a smarter, more intelligent grid, coupled with condition-based maintenance, represents a gradual evolution rather than a sudden revolution. This transformation takes time, and systems are adapting at different speeds. However, even those in the early stages of this transition can recognize the direction the industry is heading. Given that gas-insulated switchgear typically has a lifespan of 30-40 years or more, it is prudent to future-proof infrastructure. As a result, some are turning to hybrid systems. The hybrid gas density monitor combines the advantages of a mechanical monitor with a reference gas chamber and the advanced functionalities of an electronic gas density sensor, all integrated into a compact, multi-functional device. With continuous measurement output, it is ideally suited for gas management and trend analysis systems. It also includes a local display and durable switchpoint alarm contacts for enhanced reliability. Smart Grid Integration Even if the current digital ecosystem is not fully equipped to utilize the continuous monitoring and real-time data provided by the electronic gas sensor, this technology is seamlessly embedded within the equipment. This ensures its availability for future use as grids evolve and become more compatible with smart technologies.


Expert Commentary
The HVAC/R industry is in the process of a major shift as A2L refrigerants become the standard in residential and commercial system HVAC. This change is being propelled by stricter environmental policy and advancements in refrigeration technology. However, the transition is not without its hurdles, posing new considerations for system owners, technicians, and equipment manufacturers. Favor of GWP alternatives The Environmental Protection Agency (EPA) has established clear guidelines to phase out hydrofluorocarbons (HFCs) in favor of lower global warming potential (GWP) alternatives. The 700 GWP limit imposed by the EPA, forced manufacturers away from non-flammable A1 to mildly flammable A2L refrigerants for comfort cooling chillers and air-to-air unitary equipment. R-410A split systems Under current regulations, R-410A split systems can still be installed until January 1, 2026 Under current regulations, R-410A split systems can still be installed until January 1, 2026, but manufacturers had to halt production of R-410A-based equipment by January 1, 2025. As for packaged systems, which are fully assembled and sealed at the factory, sales will remain permitted until January 1, 2028, but only for equipment manufactured before 2025. Adaptation of A2L refrigerants These regulatory milestones mark a significant step toward a new era in HVAC/R technology, emphasizing sustainability and compliance with modern environmental standards. While the transition is underway in our market as we speak, there are some key factors that play into the adaptation of A2L refrigerants. How we implement, gain familiarity, and roll out these systems provides challenges. System Design Modifications ASHRAE Standard 15 first added these requirements in its published version of 2019 ANSI/ASHRAE Standard 15 is widely recognized as the preeminent guide for the safe use of refrigeration equipment, as evidenced by its inclusion in building codes at the state and local level. ASHRAE Standard 15 first added these requirements in its published version of 2019. For high-probability systems, in which the basic design or the location of components is such that a leakage of refrigerant from a failed connection, seal, or component could enter the occupied space, these requirements underwent major revisions for the 2022 version, with intent to better harmonize with the requirements in UL 60335-2-40. Modifications in HVAC system design The transition to A2L refrigerants necessitates modifications in HVAC system design to ensure compatibility and safety. One significant consideration is component compatibility; all system components, including compressors, heat exchangers, and expansion devices, must be rated for A2L refrigerants to ensure optimal performance and safety. Failure to use appropriate components could lead to operational inefficiencies or increased safety risks. Component Testing/Approval Requirements UL 60335-2-34 is a safety standard that applies to motor-compressors used in refrigeration systems UL 60335-2-34 is a safety standard that applies to motor-compressors used in refrigeration and air-conditioning systems. The UL 60335-2-34 6th edition was established in 2017 as the safety standard for compressors, introducing several key updates. One major change is the requirement for a new Maximum Rated Current marking, ensuring clear identification of electrical ratings. Additionally, the standard introduces various new testing methods for motors and their protective mechanisms to enhance safety and reliability. Testing methods outlined in UL 207 UL207 covers “Refrigerant-Containing Components and Accessories, Nonelectrical” which are components Danfoss refers to as “line components”, such as filter driers, expansion valves and pressure regulating valves. The testing methods outlined in UL 207 include burst pressure tests, fatigue tests, and hydrostatic tests to verify nonelectrical refrigerant-containing components and accessories. UL 207, which remains a referenced standard under UL 60335-2-40, has been reapproved for use with R-454B. Dealing with A2L refrigerants Compliance can be achieved through burst testing at five times the maximum pressure rating Unlike A1 refrigerants, where leaks at gaskets or mechanical seals were not a concern at twice the maximum pressure, such leaks now pose a significant issue when dealing with A2L refrigerants. Compliance can be achieved through burst testing at five times the maximum pressure rating or by conducting a fatigue test at three times the maximum pressure rating without the product bursting or leaking from any mechanical connection. Implementation: Choosing a Solution Understanding what makes sense for your sector of the market for this transition is paramount in how OEMs will implement (and many already have) A2Ls into the next generation of equipment. Let’s zoom in and look at the HVAC segment related to commercial A/C units. The two main A2L refrigerants that were approved via SNAP rule 26, being used to replace R-410A in the 2025 transition requirement, are R-32 and R-454B. These two offer different approaches to the design requirements needed to be implemented. R-454B Danfoss has a selection tool called Cool Selector® 2 that is free to download online While no refrigerant is a direct replacement for R-410A, R-454B which has a GWP of 466, is considered a relatively close “drop in” solution. As such, most major components of the system, such as compressors and heat exchangers, can usually stay the same size. This is the lowest GWP solution available in the “high-pressure” range. With that being said, R-454B operates at lower pressures than R-410A, it also operates at lower mass flows than R-410A. This can leave your current liquid line, liquid line solenoid, expansion device slightly oversized. It is considered good practice to verify the sizing of these existing components when introducing R454B. Danfoss has a selection tool called Cool Selector® 2 that is free to download online. This can help you in verifying Danfoss components. R-32 If the transition to A2L refrigerants is going to coincide with a major redesign of that unit, then R-32 (GWP 677) may be an option for your transition. R-32 will work at overall higher operating pressures and provide a significant increase in capacity vs R-410A. But with this comes the reality that most components in the system, possibly including piping sizes, will need to be changed to better suit the use of R32. R32 as a refrigerant, will also generate higher discharge temperatures than systems running with R-410A, creating a problem that manufacturers will need to account for in low ambient heat pumps and high condensing temperature environments. Leak Detection and Mitigation Refrigerant leak detectors must be installed in every unit with individual circuits charged with 4lbs As A2Ls pose a higher flammability risk, effective leak detection and mitigation strategies are essential for maintaining safety in environments where A2L refrigerants are used. Refrigerant leak detectors must be installed in every unit with individual circuits charged with 4lbs of A2L refrigerant or more. More details on charge limits for systems and what mitigations requirements are needed can be found in UL60335-2-40 Annex GG. These detection systems enable quick identification and response to refrigerant leaks, reducing the potential for accidents or equipment damage. Danfoss leak detectors use thermal conductivity technology, were among the first to be UL-approved a year ago and come in a variety of configurations for HVAC/R equipment manufacturers. Proper mitigation strategies Proper mitigation strategies are crucial for preventing refrigerant accumulation in case of leaks. They must be tied into the unit control scheme. Disengaging any heating elements eliminates the possibility of ignition sources. Engaging evaporator fans increases circulation, ensuring that any leaked refrigerant is quickly dispersed, minimizing the likelihood of hazardous concentrations forming. In addition, per UL60335-2-40, service and maintenance procedures must incorporate regular leak inspections as a standard practice. Refer to ASHRAE 15 or UL60335-2-40 for further readings and requirements. Service and Familiarity Technicians must gain a version of the parts of A2L refrigerants and are required to pass an A2L test While manufacturers focus on design changes to accommodate the A2L transition, industry members who will install and service units also must adjust to the changing landscape of refrigerant. Technicians must gain an understanding of the characteristics of A2L refrigerants and are required to pass an A2L certification test under EPA Section 608. Looking Forward This phase of transition is better conceptualized as a mid-term solution. The American Innovation and Manufacturing (AIM) Act was passed in 2020. This directed the EPA to address hydrofluorocarbons (HFCs) and phase down production and consumption of HFCs by 85% by 2036. It is likely in the future, we will see another step in transitions to ultra-low GWP Refrigerants such as R-290 (A3 class), R-1234ze, or R-515B. Before the AIM Act, individual states like California were looking to regulate their own refrigerant marketplaces. As adoption of new EPA regulations might be slowed under the current U.S. administration, it is uncertain if any future deregulation by the federal government could lead to some states restarting their own regulation programs. But as we stand now, lower GWP A2L refrigerants still continue to grow in the marketplace.
Data centers worldwide are under intense pressure. High-powered computing is a global necessity that seemingly gets more demanding by the day. There’s also the need to prioritize sustainability improvements ranging from resource conservation to decarbonization. And data centers must consider their bottom line and remain competitive. Anticipating the challenges data centers will continue to face, scientists and engineers have innovated two-phase (2-PIC) immersion cooling. With the capacity to meet the elevated cooling requirements driven by high-powered computing, this next-generation solution delivers on environmental priorities by significantly lowering data center energy consumption, slashing, if not eliminating, water use, while supporting decarbonization, circularity missions, and more. Emergence of 2-PIC Traditional approaches are fast approaching capacity for meeting current and future cooling needs The emergence of 2-PIC comes at a critical time, because the traditional cooling methods that have kept data centers up and running so far—namely air cooling and water cooling—are doing so at the detriment of the planet. Additionally, these traditional approaches are quickly approaching capacity for meeting current and future cooling needs. Air- and water-cooling methods are used in approximately 95% of the estimated 8,000 data centers that exist today. The criticality of high-powered computing Once seen as a future need, high-powered computing, and faster-than-ever processing are now established as critical to the operation of businesses, governments, organizations, and other entities that support the way communities function, survive, and thrive. Whether it’s health and wellness, financial institutions, economic growth, safety and protection, entertainment, education, or any other service supporting our way of life, successfully providing that service fully depends on the ability of data centers to quickly and reliably obtain, store, and process data. Influence of AI AI has a profound influence and, generates far more power than traditional internet uses Moreover, when we say “data centers,” we’re not just speaking of big players like Microsoft, Google, Meta, and Amazon. Equally dependent on high-performance, high-speed computing are enterprise data center operators, such as our governments and military, financial institutions, healthcare systems, educational institutions, and more. We also must acknowledge the profound influence of artificial intelligence (AI), which generates far more power than traditional internet uses. Its effects are far-reaching, enhancing patient care, supporting risk management and fraud detection in finance, boosting crop yields within agriculture, and more. The environmental costs of data centers According to the latest estimates by the International Energy Agency, data centers worldwide produce 1% of energy-related carbon emissions and in 2022 used approximately 460 TWh of electricity per year—equating to 2% of global electricity demand. McKinsey and Company estimates 40% of this electricity is used for data center cooling. Data centers’ impact on the environment also includes their significant water consumption, averaging 300,000 gallons per day, and a physical footprint that averages 100,000 square feet but in the case of some hyperscale data centers can range between 1.3 to 2 million square feet. In terms of growth, a U.S. market report from Newmark tells us that in the U.S. alone, the U.S. data center footprint will absorb 35 gigawatts by 2030, which is more than twice the data center power consumption of 2022. The emergence of liquid cooling: the elevated interest in 2-PIC From reducing energy and water consumption to shrinking physical footprints, 2-PIC offers the planet a better data center solution. In less than two years, traditional cooling systems won’t be able to support the exponential growth in the world’s data processing and storage applications. Based on publicly available product roadmaps from major chip manufacturers, by 2026, air-cooled systems will no longer be able to meet the cooling needs of most next-generation, high-performance computing chips. Capable of removing heat more effectively than air cooling, liquid cooling uses a liquid such as water or a dielectric fluid to cool the heat-generating components of servers. The liquid can cool these components directly, or it can be done indirectly through a heat exchanger. With two-phase immersion cooling the entire server rack is submerged in a tank filled with a dielectric fluid. Single-phase and two-phase liquid cooling Single-phase liquid cooling uses a pump to circulate the liquid through a closed-loop system Single-phase liquid cooling uses a pump to circulate the liquid through a closed-loop system. Two-phase liquid cooling uses a phase-change material, such as a refrigerant, which evaporates and condenses as it absorbs and releases heat. With 2-PIC, which is a form of two-phase liquid cooling, the entire server rack is submerged in a tank filled with dielectric fluid. The fluid boils as it’s heated by the components of the servers, creating bubbles that rise to the surface and condense in a heat exchanger. Gravity then returns the condensed fluid to the tank, creating a natural circulation loop that does not require pumps or fans. Advantages of 2-PIC 2-PIC is commanding attention as the solution for meeting the cooling demands of the high-powered computing components of today and tomorrow. Moreover, the technology of 2-PIC systems, combined with the right dielectric fluid, delivers advantages to “take the heat off” data centers. Here’s a breakdown of additional 2-PIC benefits: Up to 90% reduction in energy consumption: Based on modeling completed by the industry, 2-PIC is expected to reduce up to 90% of data center cooling energy consumption and 40% of overall data center energy consumption*. (*Compared to traditional air-cooling technologies) Enhanced computing performance and data center reliability: 2-PIC allows servers to operate at higher temperatures and power densities, while reducing the risk of overheating. Significant reduction in water consumption: Depending on the data center location and cooling design methodology, water consumption could even be eliminated completely. 60% reduction in the physical footprint: 2-PIC reduces the space required for cooling equipment, freeing up more floor area for servers and increasing the rack density of the data center. Lower GWP and circularity: Chemours Opteon™ 2P50 is a developmental dielectric heat-transfer fluid, currently pre-commercial, pending regulatory approval. It offers an extremely low global warming potential (GWP) of 10 and was specifically created to optimize the performance of the electronic components in a 2-PIC system. This 2-PIC fluid also enables the reprocessing/reuse of existing fluid to maximize circularity. The bottom line: In addition to other compelling data, a recent study commissioned by Chemours and LiquidStack through Syska Hennessy, revealed that, compared with other state-of-the-art liquid cooling methods, 2-PIC can deliver up to a 40% lower total cost of ownership (TCO) and significantly reduce operational expenditures (OPEX), with savings ranging from 54% to 88.6%. Benefits of new data center cooling technologies compared to single-phase direct-to-chip, and single-phase immersion methods. 2-PIC, the future-ready solution As the world’s reliance on AI and other high-powered computing capabilities escalates, data center cooling solutions must grow with demand while significantly reducing their impact on the environment. In global energy savings alone, 2-PIC could generate an estimated savings of 340 TWh by 2055—the equivalent of powering more than 517 million laptops 24/7. And even with increasing IT loads, 2-PIC maintains its performance, ensuring long-term cost-effectiveness and adaptability to meet future demands. With society at a crossroads between the criticality of high-powered computing and a planet in crisis, the industry is turning its attention to 2-PIC as the solution for today and tomorrow.
Until a couple of years ago, most of the talk about heat pumps occurred around this time of year, when more than half the planet prepares for an autumn cooldown. These discussions were typically limited to regions that only experienced moderate winters. But as anyone who has recently perused an HVACR trade magazine or website—or participated in an industry webinar, event, or social media conversation—can tell you, the topic of heat pumps is virtually unavoidable. Not only do heat pump discussions now occur year-round, but they’ve also ascended to consistent headline status and transcended the traditional boundaries of moderate climates. The decarbonization megatrend One might say heat pumps have taken their place on the global stage. If you’re asking why this has happened, the answer requires just three words: the decarbonization megatrend. However, for industry professionals looking to grow their businesses, it’s helpful to gain a deeper understanding of heat pumps—how they work, ways they are currently meeting HVACR needs, and where the technology is headed for next-generation applications. Through this understanding, members of the industry can better forecast customer needs as well as identify opportunities for expanding in both current markets and, potentially, new ones. How heat pumps work—don’t let the name fool you The heat released as the refrigerant condenses is then transferred to interior spaces What heat pumps do and, more specifically, how they do it provides the key as to why they are now being considered a “hero” of decarbonization. The term can be misleading, because “heat pumps” do not generate heat. Because of this, heat pumps are being more widely embraced as the lower-carbon-emission alternative to combustion-based heating technology that uses, for example, fossil fuels. Instead of creating heat, heat pumps extract heat energy from where it’s not needed and move it to where it is needed. When a heat pump is in heating mode, its refrigerant evaporates as it absorbs heat from the outside. The heat released as the refrigerant condenses is then transferred to interior spaces. In warmer weather, a heat pump kicks into cooling mode and the process is reversed, as heat is extracted inside and released outside. This non-combustion process of moving heat from one place to another provides several potential benefits to society: Heat pumps support the megatrend toward decarbonization. They replace fossil-fuel heating with high-efficiency technology. They can be paired with lower-global-warming-potential (GWP) A2L refrigerants—such as R-454B and R-32—to further increase environmental benefits, while offering similar performance to the legacy R-410A. They offer the ability to tap into alternative energy sources, such as industrial waste heat as well as heat sourced from the air (ambient), ground (geothermal), or lakes/ponds (water). Meeting today’s needs—these aren’t your grandfather’s heat pumps Heat pump technology has been commercially available and in use since the 1950s. Early versions of heat pumps were essentially reversible air conditioning units, and most used traditional refrigerants—like R-22 and, more recently, R-410A. These units performed well and operated safely using lower-toxicity, nonflammable (A1) refrigerants. However, they were known to sometimes struggle at lower ambient temperatures. As often happens in the world of science and technology, challenges drive the search for solutions. Today, we’re seeing innovations that result in efficient, effective cold-climate heat pumps that optimize various components, such as compressors, heat exchangers, expansion valves, and their controls. Thanks to these innovations and others, the U.S. and other countries are experiencing broader heat pump adoption and, in turn, supporting progress toward decarbonization. Heat pump technology has been commercially available. Increasing heat pump accessibility and viability in more places and spaces is also critical to the HVACR industry’s commitments to the environment—and its need to heed regulations advancing the transition to systems reducing climate impact. Emerging systems use mildly flammable (A2L) refrigerants. They are similar in design to legacy systems and include modifications to mitigate risks associated with the change to A2Ls. Where things are headed—heat pump technology is just getting started Even with the significant advances we’ve seen in colder-climate heat pumps, there is still untapped potential in terms of what the technology can achieve. We can expect to see continued innovation as end-user needs and environmental priorities continue to evolve. Some foreseeable growth areas for heat pumps include: Traditional applications—that is, moderate climates Expansion into nontraditional climates—heating in very cold climates and cooling in hotter regions Domestic water heating, replacing fossil-fuel systems Leveraging a variety of heat sources—geothermal, air-sourced, and water-sourced Harnessing waste heat generated by energy-intensive industrial processes Use of lower-GWP A2L refrigerants System optimization will also drive greater use of lower-GWP A2L refrigerants, such as R-454B Supporting these growth areas will be innovations that optimize high-performance, high-efficiency delivery of extracted heat, using a combination of traditional and new split-ducted, ductless/mini-split, and mono-block technologies. System optimization will also drive greater use of lower-GWP A2L refrigerants, such as R-454B, while limiting the use of highly flammable refrigerants such as R-290. Refrigerant selection will also play an increasingly important role and may offer additional opportunities for application-specific technology. As heat pump applications expand, we can expect to see greater focus on selecting the optimum refrigerant to use as the working fluid. Criteria will weigh system design, operating conditions, and other priorities against key refrigerant properties: Physical—boiling point, vapor pressure, density, and material compatibility Thermodynamic—cooling/heat capacity, energy efficiency, pressure-enthalpy (PH) curves Environmental—ozone depletion potential (ODP) and global warming potential (GWP) Safety and health—flammability and toxicity Conclusion: There’s strong and ample reason to “stay pumped” Over the past several years, members of the HVACR industry have enthusiastically embraced new heat pump solutions. Evolving heat pump technology and expanding applications will continue as the industry progresses along the path of more energy-efficient, lower-GWP, and more sustainable new-generation and next-generation heating and cooling. This, coupled engineering and science that leverages untapped heat pump potential, will mean more opportunities for HVACR contractors to deliver new options to the markets they serve. With a strong understanding of their customers’ individual heating and cooling needs, climate challenges, and sustainability goals, contractors can confidently select the best heat-pump refrigerant solution.
Editor's Note
Johnson Controls’ Advanced Development Engineering Center (JADEC) in New Freedom, PA., about 25 miles from Philadelphia, highlights and demonstrates the company’s capabilities related to development, testing and manufacturing. The 357,000-square-foot facility is an advanced engineering and testing facility for water-cooled chillers, air-cooled chillers, air handlers, compressors, and heat pumps. Much of the development in the facility centers on advancements in a critical vertical market for the HVAC industry – data centers. Big challenge Data centers are a big challenge – and a huge opportunity – for the HVAC industry. “You cannot ignore the tremendous growth opportunity in this vertical,” says Todd Grabowski, president, Global Data Center Solutions for Johnson Controls. Unlike other verticals that are more dominant in certain geographic regions, data centers are growing everywhere globally – and at a breathtaking pace. “As a growth company, it is critical that we have solutions to handle the growth and serve the customers in the data center market,” says Grabowski. Performance of various components Testing options at JADEC include testing the performance of various components Testing options at JADEC include the ability to test the performance of various components in a controlled environment that approximates how they will operate in the customer’s real-world setting. There are more than 20 testing labs available at the JADEC campus, covering some 250,000 square feet. “We want everyone to understand the unique position Johnson Controls is in to use our technology and our manufacturing scale to accomplish desired outcomes,” said Grabowski. Non-compressor solution JADEC displays the full breadth of what they offer, including a non-compressor solution using direct evaporative cooling and an air-cooled unit that uses a screw compressor or a magnetic-bearing centrifugal compressor. Also included are various water-cooled chillers. Johnson Controls owns, develops, tests, and manufactures all the compressors on display. Customers are assured of getting a fully engineered and supported solution from Johnson Controls (e.g., no third-party compressors). Johnson Controls owns, develops, tests, and manufactures all the compressors on display. Colocated data centers Grabowski emphasizes that each customer installation has site-specific needs that require unique solutions that Johnson Controls seeks to fulfill. The company works closely with data centers, including those operated by “hyperscalers” such as Amazon, Microsoft, Apple, and Meta, and colocated data centers that rent space and capacity to customers based on their growth and needs. Colocated data centers come in a variety of sizes and types; some of them are operated by companies such as Equinix and NTT. Data center solutions Sustainable methods include the use of refrigerants with ultra-low GWP The sustainability of data center solutions is a bigger issue than ever, given the sheer volume of data centers being built to handle the world’s growing computational needs. Sustainable approaches include the use of refrigerants with ultra-low GWP, and water-free systems that do not require higher costs or create higher demands on a locality’s water infrastructure. Magnetic bearing centrifugal compressors are more energy-efficient because no friction is lost in the compression; also, the equipment is quieter. Impact on global electricity demand “Sustainability has always been an important aspect, and now it is critical in 2024 and beyond,” says Grabowski. Because data centers are huge consumers of energy, they can put more strain on the electricity grid and have a big impact on global electricity demand. Lowering energy usage helps to address the challenge. “We want to contribute to energy efficiency, be good stewards of water, and reduce noise,” says Grabowski. Increasing the challenges are the proliferation of new artificial intelligence (AI) chips, more common in newer data centers, which need more power and create more heat than older chips. Advantages of water cooling The liquid contained in a cold plate on top of the chip is denser than air and accept more transferred heat Closed-loop liquid systems are used to cool individual chips, an application that does not cause a strain on local water supplies. The liquid contained in a cold plate on top of the chip is denser than air and can accept more transferred heat. However, chillers and cooling towers lose water through evaporation and can strain local water supplies. Johnson Controls is researching and testing systems that provide the advantage of water cooling without losing excess water to evaporation. Air-cooled systems In contrast, air-cooled systems can cool chips to a point, but may not provide enough cooling for high-density chips. Johnson Controls provides air-cooled machines up to 600 tons and water-cooled systems up to 4,000-plus tons. “As chip technology evolves, the way you cool, secure and automate the entire data center changes as well,” says Grabowski. “Companies such as Johnson Controls must keep up with evolving trends and provide unique solutions.” As chips become denser from a heat-generation perspective, systems must be optimized from a footprint and energy standpoint. JCI provides air-cooled machines up to 600 tons and water-cooled systems up to 4,000-plus tons. Technological solutions “As chip density increases, we will have technological solutions ready for the next generation of chips when they come out,” adds Grabowski. Johnson Controls is also involved in developing new approaches to managing the heat from data centers, such as the possibility of recapturing the heat and circulating it into a district-heating system for a nearby community, university, or hospital. A more widely deployed approach in Europe, the concept of district heating is gaining acceptance in the U.S. market. {##Poll1725623180 - What is the biggest challenge the data center market presents to the HVAC community?##}
SNAP Rule 26 marks an important milestone in the transition from commercial refrigeration to new refrigerants. The rule lists refrigerant substitutes that provide a spectrum of technological solutions to meet required performance, global warming potential (GWP), safety, and environmental standards. SNAP stands for Significant New Alternatives Policy, a program by the U.S. EPA (Environmental Protection Agency) under the Clean Air Act. In general, the program aims to evaluate and regulate substitutes for ozone-depleting substances, considering their overall risks to both human health and the environment. Impact of SNAP Rule 26 Final SNAP Rule 26, Protection of Stratospheric Ozone, lists acceptable substitutes in commercial and industrial refrigeration. SNAP Rule 26 will be effective July 15, 2024. The incorporation by reference of certain material listed in the rule is approved by the Director of the Federal Register as of July 15, 2024. The incorporation by reference of certain material listed in the rule is approved by the Director of the Federal Register “To date, the SNAP program has provided a very effective framework for evaluation and approval in support of innovation and the transition to new technology,” says Andrew Pansulla, Technical Service Engineer, The Chemours Company, a global chemistry company that provides a range of refrigerant products. We asked Pansulla to elaborate further on the impact of SNAP Rule 26 and what lies ahead. Q: How will the Rule’s finalization impact various commercial refrigeration sectors? Pansulla: The rule’s finalization will impact commercial refrigeration in several ways. Areas, where impact will likely be seen, include providing more acceptable refrigerant options, adherence to updated standards, new equipment design standards, and the exemption of propane from the venting prohibition for refrigerated food processing and dispensing equipment. These impacts could trigger changes in operational, manufacturing, and environmental compliance strategies in the commercial refrigeration sectors. SNAP Rule 26 will enable the adoption of the listed substitutes, including Chemours Opteon™ refrigerants, with global warming potential (GWP) lower than existing refrigerants. This rule does not require any changes to existing equipment and will impact only new equipment that uses the specific substances referenced in the SNAP rule. Q: What is the outlook for additional requirements for safe handling and use of alternative refrigerants? What specific safety standards are expected or appropriate? Pansulla: As part of the comparative risk framework used by the EPA to assess new alternatives, the EPA considers and implements use conditions that will ensure the safe use of products. These use conditions rely upon existing safety standards (e.g., UL and ASHRAE) which are available at the time the rule is finalized. In the case of SNAP Rule 26, many of the use conditions require adherence to UL 60335-2-89 and ASHRAE-15-2022. These standards are reviewed and updated periodically to maintain relevance with the products subject to the standards. Q: What are any limitations of the use of A2L refrigerants under SNAP Rule 26? Pansulla: There are two main categories of limitations under SNAP Rule 26. The first, as mentioned above, is the adherence to specific safety standards that apply to refrigerants that are designated as mildly flammable (A2L). The second is based on the GWP of the refrigerant. In the case of the A2L refrigerants subject to SNAP Rule 26, the EPA imposed conditions on the type of equipment and specific circumstances in which the substitute may be used. For example, the EPA is permitting the use of R-454A in supermarket systems, but only on the high side of a cascade system, or when the refrigerant charge capacity is less than 200 pounds. Q: Which new-generation A2L refrigerants are fit for which commercial refrigeration applications? Pansulla: Under SNAP Rule 26, the EPA deems R-1234yf, R-1234ze(E), R-454C, R-455A, R-457A, and R-516A as acceptable subject-to-use conditions for various commercial refrigeration applications. This selection is primarily driven by these refrigerants having GWPs under 150. However, certain applications necessitate refrigerants with higher GWPs due to unique performance characteristics. For example, R-454B and R-32 were listed for industrial process refrigeration with exiting fluid temperatures below minus 30 degree Celsius because these two specific refrigerants have lower boiling points than the other six less-than-150-GWP alternatives. However, it is critically important to consider the additional use conditions when designing equipment with refrigerants that have a GWP greater than 150. Q: So various equipment needs different refrigerants? Pansulla: The EPA purposefully lists several different refrigerants in each application to allow for equipment manufacturers to consider a variety of different factors that go into refrigerant selection, such as energy efficiency, capacity, normal boiling point, temperature glide, cost, safety, and use conditions. There is no one-size-fits-all solution for the entire commercial refrigeration industry. Q: How can commercial refrigeration businesses achieve a smooth transition to A2Ls? Pansulla: Keys to a smooth transition to A2Ls include understanding what refrigerants the EPA has approved as acceptable substitutes under the SNAP program, the sector-based GWP limits imposed by the Technology Transitions Program under the American Innovation and Manufacturing (AIM) Act, and which refrigerants provide the best combination of technical performance and environmental characteristics. Many resources are available to navigate the regulatory landscape and select the best low-GWP refrigerants to meet the needs of this industry. Working with companies like Chemours, who has nearly a century of refrigerant innovation and experience, is a great first step in the transition process. Q: What is the “staying power” of A2Ls — based on their chemistry, sustainability, and other attributes, combined with regulations such as SNAP Rule 26? Pansulla: The identification, selection, and development of new refrigerants that deliver required performance while meeting increasingly stringent environmental standards is a challenging process. With the identification of certain hydrofluoroolefin-based (HFO) refrigerants as an alternative to meet these criteria came a new safety classification. These HFO-based refrigerants are classified as A2Ls. While slightly more flammable than existing hydrofluorocarbon-base (HFC) refrigerants, HFOs are much less flammable than hydrocarbons, which are classified as A3 (two categories higher on the ASHRAE flammability spectrum). Moreover, such refrigerants offer an excellent alternative to substances with higher toxicity, such as R-717. The listing of A2L refrigerants in SNAP Rule 26 clearly indicates that such refrigerants can be used safely in commercial refrigeration as well as many other applications, which are subject to the SNAP Program, when adhering to the applicable safety standards.
Humidity can influence employee health and productivity in the workplace. Humidity, temperature, and ventilation all work in concert to create a healthy indoor environment that supports overall occupant well-being. “Dry indoor air can cause discomfort in the form of dry skin, eyes, and throat for staff and visitors,” says Jennifer Montville, Director of Marketing at DriSteem, a manufacturer of humidification systems. Air-related health issues “There are real costs associated with health-related issues caused by dry air, including a higher occurrence of infections and increased rates of staff absenteeism?” Maintaining a comfortable work environment, including the correct humidity levels, prevents respiratory issues and reduces the spread of illnesses, ensuring a healthy working environment and boosting productivity and efficiency, says Montville. humidity levels Humidified spaces help keep facility costs down by improving thermal comfort at lower temperatures Maintaining humidity levels between 40% and 60% RH is ideal for mitigating virus transmission, she comments. Humidified spaces feel warmer and are more comfortable for employees, which in turn increases their productivity with improved concentration and less fatigue. It also helps keep facility costs down by improving thermal comfort at lower temperatures. dehumidifiers Employing dehumidifiers to keep humidity levels from rising above that 60% RH threshold is also important. Removing excess moisture from the air reduces distraction from unpleasant smells or health issues caused by mold, mildew, or fungi that thrive in moist environments. All the ways that proper humidity levels affect employee health and productivity in the workplace also contribute to increased customer satisfaction in office and retail spaces, says Montville. preventing product issues “We all prefer to spend time in places where we feel physically comfortable,” she says. “Customers in offices and retail spaces are no different. When physical comfort is not an issue, we are likely to spend more time and engage more deeply.” Well-managed humidity levels also help to prevent product issues such as shrinkage, warping, or degradation due to moisture fluctuations. Food quality is particularly impacted by humidity levels. In a retail store, this can translate to spending more time shopping in a store and a more positive opinion of the products being considered. recommended indoor relative humidity level Keeping relative humidity levels within the range ensures the health and safety of building occupants The recommended indoor relative humidity level ranges from 30% to 60% RH, according to guidelines published by the American Society of Heating, Refrigerating, and Air-Conditioning Engineers (ASHRAE). Keeping relative humidity levels within this range ensures the health and safety of building occupants without promoting mold growth or other indoor air quality issues. air quality goals With that said, the type of indoor space, air quality goals, and how the space is used will determine the best relative humidity levels for each facility, according to Montville. Machinery and sensitive electronic equipment are vulnerable to low or fluctuating moisture levels. Static electricity buildup and electrical malfunctions are among the potential consequences of inadequate humidity control. precise humidity control Many industrial processes depend on the consistent quality of materials, and fluctuations in relative humidity (RH) can result in less-than-ideal inputs which in turn impact the quality of final products. From preventing mold growth, spoilage, and texture deterioration in food processing to safeguarding medication stability, efficacy, and safety of pharmaceuticals, precise humidity control is critical to achieving intended results. Optimal RH levels Adequate humidity also supports the body's natural defense mechanisms, enhancing the effectiveness Maintaining appropriate humidity levels is essential for infection control. Optimal RH levels can inhibit the growth and transmission of airborne pathogens, such as viruses, bacteria, and fungi. Adequate humidity also supports the body's natural defense mechanisms, enhancing the effectiveness of respiratory tract mucous membranes in trapping and neutralizing pathogens. Conversely, dry indoor air impairs these defenses, increasing susceptibility to respiratory infections. humidity control systems Investing in commercial humidity control systems, such as those offered by DriSteem, can effectively regulate RH levels within facilities. “These systems provide flexibility and precision in catering to specific humidity needs across different areas within the facility,” says Montville. Whether integrating humidity control solutions in existing structures or implementing them in new buildings, factors such as the type of indoor space, energy source, required maintenance, and capacity determine the best technology for each building, she says.
Case studies
Sophisticated temperature control using Fujitsu General Air Conditioning UK technology is delivering the best possible growing conditions for a vertical farming enterprise in Northamptonshire. Vertical farming involves growing food indoors on multiple levels, in vertically stacked layers, using UV lighting. With arable space increasingly coming under pressure from urbanization, the technique aims to provide an efficient and sustainable source of food into the future. energy and resource-efficient Vertical Future says its systems use up to 98% less water compared to traditional farming, are energy and resource-efficient, and can grow the same amount of produce in 1% of the space when compared to traditional methods. The installation was carried out by CSL Air Conditioning with equipment supplied by distributor Oceanair. monitoring and control technologies Darren James, Director of Vertical Future, said, “We deliver advanced growing solutions tailored to an industry that demands unparalleled precision and control. Our systems integrate sophisticated monitoring and control technologies, ensuring the optimum growth environment to maximize crop quality and yield." “I was extremely impressed with the combined work of both Fujitsu and Oceanair on this project." choosing equipments "Both companies attended the site in tandem so that they could come up with the best option for this project in loadings and efficiency, and choose the relevant equipment within the area where we could install the systems." “This meant more than one site visit but they kept me informed throughout the design stage of the project and it has worked wonders. The site has been up and running for over 12 months with no issues.’’ Controlled Environment Agriculture (CEA) technology By monitoring every aspect of the environment, it can achieve the best possible yield For the installation at Syan Farms in Horton, CSL Air Conditioning chose equipment from Fujitsu to meet the precise requirements of the customer and end-user. Electrical installation was carried out by a third party. Syan Farms uses Controlled Environment Agriculture (CEA) technology, which sets the temperature, light, and humidity within each growing stack. By monitoring every aspect of the environment, it can achieve the best possible yield and ensure crops are never affected by poor weather conditions or land damage. addressing air conditioning challenges Dave Crate from CSL Air Conditioning, said, “The biggest challenge is designing a system that can distribute air efficiently across the growing area." "We have developed a solution with all air conditioning units installed at a high level, with cool air sinking across the growing pods and any heat rising into the units. The wall mounts are positioned perpendicular to the growing racks to deliver air across the vertically stacked pods.’’ Fujitsu 22kW High Static Duct Units The ducted units are mounted centrally, and each uses a flexible fabric duct sock to distribute air evenly Oceanair supplied CSL with the equipment needed to keep the growing area at a constant 23°C. It was also crucial to design a system which avoided high-velocity air movement in the 30m2 space, as the plants require conditions as close to natural as possible. Two Fujitsu 22kW High Static Duct Units are paired with 22kW HP Inverter Condensers. The ducted units are mounted centrally, and each uses a flexible fabric duct sock to distribute air evenly along the center of the warehouse. These units work alongside eight Fujitsu 9.4kW Inverter Heat Pump Condensers, connected to eight 9.4kW Wall Mount Units. single controller operation The two groups of four systems, operating off a single controller, are sited at high levels on facing walls perpendicular to the growing racks to prevent excess air movement. Tony Holland of Oceanair said, “We know from long experience the capabilities of the Fujitsu kit and were confident that it was the correct choice for Vertical Future at Syan Farms." “It was a new experience to work out climate control loadings for plants rather than people but working as a team of manufacturers, distributors, engineers, and end users, we came up with a grid system to make sure each section had the correct loading to do the job and the proof of the warehouse now up and running and working to its full capacity is a testament to all parties concerned.” Fujitsu 6.8kW Multi Condenser The installation marks a significant leap forward from the container-based modules with localized cooling Elsewhere on site, a multi-split system consisting of a Fujitsu 6.8kW Multi Condenser connected to two 3.4kW Wall Mount Units and a Compact Cassette serves the entrance, offices, and meeting area. The project is the first of this size for Vertical Future and further sites are in development. For Syan Farms, the installation marks a significant leap forward from the container-based modules with localized cooling used previously. Food security Kelly Bullivant, Distribution Account Manager at Fujitsu General Air Conditioning, said, “Food security is becoming increasingly important and we are proud to be able to contribute to the development of vertical farming." "Our equipment is ideally suited to the precision needed for an installation of this type.’’
When the Florida Keys Aqueduct Authority opens its upgraded desalination plant on Stock Island, Danfoss high-pressure pumps and energy recovery devices will radically improve the energy efficiency of a SWRO plant that plays a central role in the Florida Keys water supply strategy. The Florida Keys Aqueduct Authority (FKAA) supplies 20 million gallons of potable water per day (75.7k m3/d) to its nearly 80,000 customers in the Florida Keys. While most of the water is normally sourced in aquifers, FKAA also operates two seawater reverse osmosis (SWRO) plants for emergency purposes and as a supplemental supply in periods of high demand. FKAA initiated the SWRO plant upgrade FKAA initiated the upgrade of one of these plants, the Kermit H. Lewin Water Treatment Plant located on Stock Island, to increase its capacity, make it more resilient to hurricanes and rising flood levels, and improve its energy efficiency. Since opening in 1980, not only have guidelines for storm protection of such critical infrastructure changed significantly, so has the potential to save on the energy required by desalination. Designed to withstand future floods and hurricanes With sustained winds above 157 mph, such storms can cause severe damage to everything in their path To improve resiliency to extreme weather events in the low-lying Florida Keys, the entire site and facility have now been upgraded to withstand Category 5 hurricanes, the most dangerous level of tropical storms. With sustained winds above 157 mph (252 kph), such storms can cause severe damage to everything in their path. Accordingly, the refurbished facility lifts all electrical and mechanical equipment above the base flood elevation and the expected sea-level rise anticipated by 2060, effectively placing the plant’s desalination operations on stilts to mitigate the risk of severe flooding. improve the plant’s energy efficiency Another key goal of the upgrade was to improve the plant’s energy efficiency at the same time as doubling its production capacity from 2 MGD (7,500 m3/d) to 4 MGD (15,000 m3/d). To bring the refurbished plant up to date and reduce its financial and environmental costs, Carollo, a major U.S. engineering firm specializing in water and wastewater facilities, specified the latest axial-piston high-pressure pumps to replace legacy centrifugal pumps and swapped out old turbines for the newest active isobaric energy recovery technology. Upgraded plant to consist of four RO trains This innovative high-pressure setup dramatically reduces the plant’s energy needs This innovative high-pressure setup dramatically reduces the plant’s energy needs. In the new Kermit H. Lewin Water Treatment Plant being built by Biwater, a world pioneer in water treatment, the RO process-specific energy consumption will be slashed from 25.6 kW/kgal (6.77 kWh/m3) to 8.6 kW/kgal (2.27 kWh/m3). With this improvement, the new plant will be among the most energy-efficient in its class, with significantly reduced electricity bills and greenhouse gas emissions. The upgraded plant will consist of four RO trains, each of which includes two Danfoss APP 86 high-pressure pumps and three Danfoss iSave 70 ERDs. Improvement in energy efficiency In addition to the dramatic improvement in energy efficiency, configuring each train with parallel high-pressure pumps provides additional resilience and other benefits: the smaller pumps are easier to lift and work on, and it is now affordable to keep a spare pump in stock. The new improved plant will come online in Q4 2024. The new Kermit H. Lewin Water Treatment Plant is located just north of the existing plant. Construction began in Q3 2021 and will be completed by Q2 2024. The plant is expected to be fully operational by Q4 2024.
Convoy of Hope is an international nonprofit based in Springfield, Missouri. Founded in 1994 by Hal Donaldson, the humanitarian organization strives to feed the world and end intergenerational poverty. Programs include training and equipping local farmers to create food security, feeding more than 533,000 children every school day worldwide, U.S. and international disaster response, and empowering women as entrepreneurs and in the workforce. Since its founding, Convoy of Hope has served more than 250 million people and provided more than $2.5 billion worth of supplies to those in need. tackling global priorities In 2021, Convoy of Hope’s leadership decided that building a new headquarters and training center would improve the organization’s ability to serve humanity. For the first time in its nearly 30-year existence, Convoy of Hope would bring staff together on one campus to tackle its global priorities. The new facility would be a point of pride in Springfield and connect team members in an inviting and comfortable setting. culture of the humanitarian organization The building would reflect the culture of the humanitarian organization and demonstrate good stewardship Additionally, the building would reflect the culture of the humanitarian organization and demonstrate good stewardship of financial resources. “We’re a non-profit organization, so we don’t want to spend more than we need to. We need to be able to take care of the heating and cooling needs in a way that’s efficient and cost-effective," said Ethan Forhetz, Vice President of Public Engagement, at Convoy of Hope. Project highlights Convoy of Hope’s headquarters is a 200,000-square-foot, modern, industrial-styled, open-concept, multi-use facility. The building houses a large atrium, auditorium, cafeteria, dining room, kitchen, open office spaces, and private offices. More than 280 of the organization’s 500-plus total employees work at the facility daily. The project team, assembled in 2021, collaborated from the design phase through the grand opening in 2023. Installation and project management Buxton Kubik Dodd, Inc., a full-service design firm in Springfield, did the architectural design, interior design, and mechanical engineering. Knight Heating & Air Conditioning, a local, family-owned HVAC contractor, did the installation and project management with support from Fields Mechanical Systems, a local LG-applied representative firm. “We try to recommend a product to the customer that has good local representation. It usually boils down to who supports a product the best. So that’s why we recommended LG,” said Chris Knight, Vice President, of Knight Heating and Air Conditioning. Challenges The heating and cooling system would need to satisfy diverse comfort requirements simultaneously Load diversity was the project team’s most significant challenge. Comfort requirements in the multi-use building vary by each space’s purpose, solar orientation, time of day, glazing, and whether the space is on the perimeter or interior. Southwest-facing offices have different heating and cooling needs than similar offices on the northeast side, as does the large, wide-open atrium versus the kitchen. On cold days when most of the building requires heating, some spaces still require cooling due to the facility’s glass frontage. The heating and cooling system would need to satisfy diverse comfort requirements simultaneously throughout the seasons, as Missouri’s weather ranged from intense heat to extreme cold. Acoustics, mechanical systems and designs The project team also considered acoustics while evaluating mechanical systems and designs. Convoy of Hope’s headquarters embraces an industrial aesthetic, which includes hard floors and concrete, exposed ceilings. With large, open spaces and few surfaces to absorb noise, a noisy HVAC system would disturb employees and reduce each space’s usability. The heating and cooling solution needed to operate quietly and fit in aesthetically. Concealing the HVAC equipment Given the facility’s size and profile in the community, Convoy of Hope tasked the project team with concealing the HVAC equipment so that it did not detract from the exterior appearance of the building. Thousands of cars pass the facility daily. The team rejected mechanical options that would have required extensive ductwork and equipment sitting in full view on the building’s lower roofs. Comfortable and seamless While hiding the equipment posed an engineering challenge, Convoy of Hope prioritized the building’s beauty While hiding the equipment posed an engineering challenge, Convoy of Hope prioritized the building’s beauty as part of being a good neighbor. “The ability to handle varying loads comfortably and seamlessly was the main goal of the project,” said Dylan Chorice, Principal Engineer, Buxton Kubik Dodd, Inc. Solution The project team decided that a variable refrigerant flow (VRF) system with heat recovery from LG would be the best and most cost-effective solution to meeting Convoy of Hope’s needs. “Early in the process, we knew LG was the partner we wanted to work with,” said Dylan Chorice, Principal Engineer, Buxton Kubik Dodd, Inc. Multi V 5 system LG’s Multi V 5 system uses comprehensive controls and outdoor units with inverters to vary compressor speeds and heating and cooling capacity based on occupant comfort needs and ambient conditions. Every outdoor unit connects to multiple indoor units, each serving a zone within the building. With LG’s inverter technology, the all-electric system uses minimal energy to move heat out of zones requiring cooling and transfer heat to zones that need heating. “What LG does for us here is allow us to meet the unique needs of our building’s individual spaces,” said Ethan Forhetz, VP of Public Engagement, at Convoy of Hope. Heat-recovery unit VRF systems typically reject indoor heat to the outdoors during cooling and operate in one mode at a time The project team specified an LG Multi V 5 system with a heat-recovery unit to solve Convoy of Hope’s load diversity challenge with simultaneous heating and cooling. VRF systems typically reject indoor heat to the outdoors during cooling and operate in one mode at a time: heating or cooling. Adding a heat-recovery unit enables LG’s VRF system to transfer heat from zones in cooling mode and simultaneously use it to warm zones in heating mode. Increased efficiency and cost savings By repurposing heat instead of rejecting it, a VRF system with heat recovery increases efficiency and cost savings while keeping diverse spaces comfortable. For example, the Multi V 5 can cool Convoy of Hope’ssouthwest-facing offices and account for solar gain while using that heat to warm the building’s cooler opposite side. The technology also allows Convoy of Hope to customize setpoints for each zone based on individual and administrator preferences. Powered by the Niagara 4 Framework®, LG’sMultiSITE VM3 controls empower facility managers to visualize, monitor, and control the entire VRF system. Mid-static ducted units The project team installed mid-static ducted units in the areas with covered ceilings. In the open office spaces with exposed high ceilings, the project team installed LG’s DUAL Vane 4-way cassettes. The cassettes cover wide spaces and contribute to healthier air with a five-step filtration and purification kit. To better match the space’s aesthetic requirements, the team placed shrouds on the cassettes, giving the units a cloud-like look that fits seamlessly into the design. Compact refrigerant lines Multi V 5 solution supported Convoy of Hope’s aesthetic needs and reduce costs by requiring less ductwork The Multi V 5 solution also supported Convoy of Hope’s aesthetic needs and reduced costs by requiring less ductwork than alternative systems.LG’s VRF system runs very quietly. Convoy of Hope team members can focus on their work without complaints about comfort or mechanical noise. The Multi V 5’s long, compact refrigerant lines enabled the project team to tackle the facility’s exterior design challenges. VRF outdoor units By installing the VRF outdoor units on the third floor’s roof, the project team kept the system out of sight to pass neighbors or people entering the parking lot. The refrigerant lines run from the upper roof and down the sides of the buildings to serve the lower floors without requiring units on the ground or the lower roofs. Result Convoy of Hope is currently listed among the top 50 organizations in the Forbes list of America’s Top 100 Charities. With its new headquarters and training center, the organization is positioned to continue and grow its humanitarian work. “It’s a brand-new building. It’s a big building. But it felt very homey right off the bat. I think a large part of that is because it’s very comfortable,” said Ethan Forhetz, VP of Public Engagement, at Convoy of Hope. Cost-effective operation LG’s Multi V 5 VRF system with heat recovery satisfies Convoy of Hope's requirements LG’s Multi V 5 VRF system with heat recovery satisfies Convoy of Hope's requirements across comfort, efficiency, acoustics, and aesthetics. The facility is a community showpiece that helps the organization keep faith with its financial supporters through cost-effective operation. “Convoy of Hope plans to be here for a very long time, so every dollar we can save on utility bills is another dollar they can put toward their mission, which is critically important,” said Dylan Chorice, Principal Engineer, Buxton Kubik Dodd, Inc. LG HVAC Products Multi V 5 (20 - 40 Ton) MultiSITE VM3 DUAL Vane 4way Cassettes Ceiling Concealed Duct Unit (Mid-Static)
With 53 men on the Jacksonville Jaguars roster, practicing 5 to 6 days per week for 10 to 12 hours a day, the demand for hot water must be enormous. As the choice for the team’s practice facility’s hot water storage and water heating capabilities, we happen to have the deets. How about 1,880 gallons of storage capacity and 2,400,000 btu/hr heating the water? Miller Electric Center The Miller Electric Center is a new state-of-the-art practice facility in downtown Jacksonville that serves as the Jaguars’ football operations headquarters. The 120 million dollar facility is 125,000 square feet and includes locker rooms, training and medical facilities, office space, and a draft room. It also features two full-size grass practice fields and one indoor field, along with shaded public viewing stands, concession areas, and a team store. Big men need big spaces Armor’s SMART TOUCH operating control makes adjusting parameters and troubleshooting a breeze Luckily, Lochinvar’s Armor Condensing water heaters are up for the job. The Armor’s stainless steel heat exchanger delivers hot water at 98% thermal efficiency and modulates at a 10:1 turndown ratio. That means the units can fire as low as 10% of their total capability and modulate up to 100% when the demand is greatest. The Jag’s facility has 3 of the AWH0800NPM units installed providing the ability to cascade which ensures the units operate with equal runtime and extends the life of the heaters. The Armor’s SMART TOUCH operating control makes adjusting parameters and troubleshooting a breeze – which is nice in Florida. Lock-Temp Round Jacketed Storage Tank With a proven storage vessel like the Lock-Temp Round Jacketed Storage Tank, making sure the stored hot water is ready for delivery is a given. These tanks have the exclusive Lock-Temp baffle that keeps water evenly stratified and the 80% draw factor allows almost the entire capacity to be used at the designated temperature. installation and commission With the help of a local manufacturers’ rep firm, Harry Warren, the installing contractor, Touchton Plumbing out of Jacksonville reported that the whole experience went off without a hitch. “The installation went extremely well, and the units have been working without fail through the first year of the facility being in use,” said Parker Touchton, project manager. The equipment was installed and commissioned according to schedule and is said to be performing as promised and at the end of a 12-hour practice, there’s no room for disappointment.
To offset the cost of tenants’ monthly electric bills and provide prospective residents with high-quality HVAC upgrades that prioritize comfort and performance, Samuels Associates, owner of the Fenway Triangle luxury apartments, sought a new, building-wide heating solution that was not only cost-effective but also added a modern touch to the building’s extravagance. QMark® MUH-Pro+ and CU900 electric heaters with SmartSeries® Plus (SSP) digital BACnet thermostats from Goodyear HVAC Sales proved to be the ideal solution. Heat in a contemporary design “From their energy efficiency, quiet operation and low maintenance to the fact that they can be controlled individually for personalized comfort, electric heaters offer several benefits in apartment buildings,” explained Andrew Martin, Manager of Product Management with Marley Engineered Products® (MEP). “Delivering supplemental comfort heat in a contemporary design, these heaters are ideal for a variety of spaces including school hallways, church vestibules, transportation terminals, stairwells, entrances, lobbies, mechanical rooms and more.” Installing Heaters while Maintaining esthetics Buildings boast modern frills and discreet and esthetically good HVAC plans that act quietly Steps away from the iconic Fenway Park, the Fenway Triangle is an 891,000-square-foot complex comprising more than 570 luxury apartment units, as well as an eclectic mix of national and local retailers, restaurants, shops and green spaces. Since opening in 2006, the building needed to address issues with its HVAC systems and controls, which were leading to high monthly electric bills. The culprit? More than 50 outdated competitor electric terminal heaters, which offered only on/off controls and needed to be operated manually. If the maintenance team forgot to shut off the heaters, "The Fenway" would incur the cost of each heater running at full capacity at a rate of about 27 cents per kilowatt-hour. Another challenge facing Fenway Triangle: The emergence of new luxury apartment complexes. These buildings boast modern amenities and discreet and esthetically pleasing HVAC systems that operate quietly. They pose significant competition for “The Fenway”, as tenants increasingly prioritize indoor air quality (IAQ) and HVAC performance when selecting their luxury residences. To remain competitive in the luxury apartment market, investing in HVAC upgrades to replace outdated equipment is imperative. QMark MUH-Pro+ and CU900 electric heaters Heaters were installed in elevator banks, stairwells, worker lounges, hallways, and facility To combat the rising cost of heating each unit within the building, MEP’s local Sales Representative, Goodyear HVAC Sales, worked with HVAC distributor Equipment Direct Sales, Inc. (EDSI) to provide the client with energy-efficient QMark MUH-Pro+ and CU900 electric heaters from Marley Engineered Products. Designed to maintain occupant comfort and a comfortable environment, the heaters were installed in various elevator banks, stairwells, employee lounges, hallways and inside the building’s recently upgraded building management system (BMS) room. “Equipped with SSP digital thermostats that provide connections to BACnet MS/TP BMS for easy control and monitoring, the MUH-Pro+ and CU900 units only run when directed by the internal schedule of the BMS,” said Matthew Goodrich, President of Goodyear HVAC Sales. “Use of the BMS saves time and reduces personnel costs by eliminating the need to travel to the heater site. And, if a BMS is not available, the maintenance team can simply use the built in seven-day programmable scheduling feature.” New electric heating units Cost-Effective Heat for Unmatched Comfort and Lower Monthly Bills In tandem with EDSI, Goodrich and his team installed several brand-new electric heating units in The Fenway’s BMS room to provide cost-effective warmth without taking up floor space or creating a tripping hazard. “Innovation and collaboration converged as we tailored a custom heating solution, seamlessly blending functionality and aesthetics,” explained Goodrich. “In fabricating this solution for the client, our dedicated team and the coordination of skilled contractors transformed this building into a space that harmonizes comfort and elegance and exemplifies the blending of form and function.” Full control of the entire heating system The thermostats include features that allow the building’s maintenance team to monitor each heater The success of the project resulted in an extremely satisfied customer. Already, the SSP thermostats have provided cost savings by turning on the heaters only when needed, resulting in less electricity usage throughout The Fenway. Additionally, the thermostats include features that allow the building’s maintenance team to monitor each heater individually from within the BMS room, granting them full control of the entire heating system and eliminating the daily trips previously needed to turn each heater on and off. “We’re already seeing the savings associated with the upgraded controls,” said John Belmonte, Head of Trilogy Operations for the Fenway Triangle. “Being able to control over 40 heaters locally allows our team to focus on tenant needs without being bogged down by the time it takes to touch each individual unit. We’re eager to work further with the Goodyear team on other buildings in the neighborhood.” Innovative approach and exceptional achievements To acknowledge the innovative approach and exceptional achievements demonstrated by the Goodyear team in overcoming the challenges faced during this project, Marley Engineered Products awarded Goodrich the 2024 Jim Herring Memorial Silver Fox Award at its recent national sales meeting. “This award for excellence in solution design embodies the spirit of Herring, who left a lasting legacy of designing creative solutions for specialized applications, was always up for a challenge and most happy when solving a unique heating or ventilation problem,” said Sean Pesce, Director of Sales for Marley Engineered Products. “Matthew and his team at Goodyear perfectly captured Jim’s talent for finding creative solutions to the most complex issues and left a lasting impression on the client.”
To adequately heat the 111 Murray Street residential skyscraper in New York, the owner sought an effective way to maintain the aesthetic of the mostly glass building without being obtrusive to its design. Custom convection style heaters, mounted in the building’s millwork by Faber Industrial Technologies, proved to be the game-changing resolution. “Convection heaters provide warmth and heat to a specific area or room by circulating air and heating it using a highly efficient electric element,” explained Andrew Martin, Manager of Product Management with Marley Engineered Products. He adds, “Designed for quiet, controlled comfort, they are ideal for both residential and commercial applications, including living rooms and bedrooms, offices, hallways, lobbies, conference rooms, retail stores and buildings with floor-to-ceiling windows.” Installing heaters while maintaining aesthetics 111 Murray Street is a 792-foot-tall residential skyscraper with 156 luxury condominiums Located in the Financial District and Tribeca neighborhoods in Lower Manhattan, 111 Murray Street is a 792-foot-tall residential skyscraper with 156 luxury condominiums and 2,100 square feet of retail space on the ground floor. Due to mechanical constraints exacerbated by the building’s slim design, hot water was not available in most of the upper residences, rendering hydronic heating systems impractical. Therefore, the client requested Berko ASL3 convector heaters from Marley Engineered Products to be installed for elegant, supplemental comfort for heat loss, condensation prevention and continuous warmth throughout each condo. The challenge, however, came from their preference to keep the heaters hidden for aesthetic reasons. “The varying heights and angles of the millwork in each condo limited our ability to install the heaters directly where we wanted them,” said Christopher Smith, a Heater Manufacturing Representative with Faber Industrial Technologies, adding “Therefore, we needed a custom design that enabled us to mount the heaters properly while also keeping them out of sight.” Hidden Heat for Unmatched Comfort and Elegance The solution involved fabricating and supplying custom dual inlet convector heaters, which were then mounted within the millwork of each condominium unit. Using a thermocouple array, the engineering team at Marley tested the Berko ASL3 convectors – at 125 watts per foot and 120V – inside a customer-supplied demo millwork section sent from New York City. After making some adjustments to the design, thermal couplers were utilized on both the heaters and their enclosures to ensure their surface temperatures were within Marley Engineered Products’ limits to pass a UL site inspection. Berko ASL3 convector heaters The result was an ‘invisible solution’ in which none of the controls or heaters could be seen in the residential units Next, Smith coordinated with the electrical and mechanical contractors on-site to fit the heaters into each condo’s temperature control system using power relays. The result was an ‘invisible solution’ in which none of the controls or heaters could be seen in the residential units. “Innovation and collaboration converged as we tailored a custom heating solution, seamlessly blending functionality and aesthetics,” explained Christopher Smith, adding “In fabricating this ‘invisible solution’ for the client, our dedicated team and the coordination of skilled contractors transformed these condos into spaces that harmonize comfort and elegance and exemplify the blending of form and function.” Berko ASL3 convector heaters The success of the project not only resulted in an extremely satisfied customer, but also left the contractors pleased with the uninterrupted delivery and installation of the heaters. They were further impressed when the custom heater and millwork system passed the UL site inspector’s test after just one evaluation. To acknowledge the innovative approach and exceptional achievements demonstrated by the Faber team in overcoming the challenges faced during this project, Marley Engineered Products awarded Smith the 2023 Jim Herring Memorial Silver Fox Award at its recent national sales meeting. Solving unique heating or ventilation problems “This award for excellence in solution design embodies the spirit of Herring, who was always up for a challenge and most happy when solving a unique heating or ventilation problem,” said Sean Pesce, Acting Director of Sales for Marley Engineered Products. He adds, “Chris and his team perfectly captured Jim’s talent for finding creative solutions to the most complex issues and left a lasting impression on the client.”
Sophisticated temperature control using Fujitsu General Air Conditioning UK technology is delivering the best possible growing conditions for a vertical farming enterprise in Northamptonshire. Vertical farming involves growing food indoors on multiple levels, in vertically stacked layers, using UV lighting. With arable space increasingly coming under pressure from urbanization, the technique aims to provide an efficient and sustainable source of food into the future. energy and resource-efficient Vertical Future says its systems use up to 98% less water compared to traditional farming, are energy and resource-efficient, and can grow the same amount of produce in 1% of the space when compared to traditional methods. The installation was carried out by CSL Air Conditioning with equipment supplied by distributor Oceanair. monitoring and control technologies Darren James, Director of Vertical Future, said, “We deliver advanced growing solutions tailored to an industry that demands unparalleled precision and control. Our systems integrate sophisticated monitoring and control technologies, ensuring the optimum growth environment to maximize crop quality and yield." “I was extremely impressed with the combined work of both Fujitsu and Oceanair on this project." choosing equipments "Both companies attended the site in tandem so that they could come up with the best option for this project in loadings and efficiency, and choose the relevant equipment within the area where we could install the systems." “This meant more than one site visit but they kept me informed throughout the design stage of the project and it has worked wonders. The site has been up and running for over 12 months with no issues.’’ Controlled Environment Agriculture (CEA) technology By monitoring every aspect of the environment, it can achieve the best possible yield For the installation at Syan Farms in Horton, CSL Air Conditioning chose equipment from Fujitsu to meet the precise requirements of the customer and end-user. Electrical installation was carried out by a third party. Syan Farms uses Controlled Environment Agriculture (CEA) technology, which sets the temperature, light, and humidity within each growing stack. By monitoring every aspect of the environment, it can achieve the best possible yield and ensure crops are never affected by poor weather conditions or land damage. addressing air conditioning challenges Dave Crate from CSL Air Conditioning, said, “The biggest challenge is designing a system that can distribute air efficiently across the growing area." "We have developed a solution with all air conditioning units installed at a high level, with cool air sinking across the growing pods and any heat rising into the units. The wall mounts are positioned perpendicular to the growing racks to deliver air across the vertically stacked pods.’’ Fujitsu 22kW High Static Duct Units The ducted units are mounted centrally, and each uses a flexible fabric duct sock to distribute air evenly Oceanair supplied CSL with the equipment needed to keep the growing area at a constant 23°C. It was also crucial to design a system which avoided high-velocity air movement in the 30m2 space, as the plants require conditions as close to natural as possible. Two Fujitsu 22kW High Static Duct Units are paired with 22kW HP Inverter Condensers. The ducted units are mounted centrally, and each uses a flexible fabric duct sock to distribute air evenly along the center of the warehouse. These units work alongside eight Fujitsu 9.4kW Inverter Heat Pump Condensers, connected to eight 9.4kW Wall Mount Units. single controller operation The two groups of four systems, operating off a single controller, are sited at high levels on facing walls perpendicular to the growing racks to prevent excess air movement. Tony Holland of Oceanair said, “We know from long experience the capabilities of the Fujitsu kit and were confident that it was the correct choice for Vertical Future at Syan Farms." “It was a new experience to work out climate control loadings for plants rather than people but working as a team of manufacturers, distributors, engineers, and end users, we came up with a grid system to make sure each section had the correct loading to do the job and the proof of the warehouse now up and running and working to its full capacity is a testament to all parties concerned.” Fujitsu 6.8kW Multi Condenser The installation marks a significant leap forward from the container-based modules with localized cooling Elsewhere on site, a multi-split system consisting of a Fujitsu 6.8kW Multi Condenser connected to two 3.4kW Wall Mount Units and a Compact Cassette serves the entrance, offices, and meeting area. The project is the first of this size for Vertical Future and further sites are in development. For Syan Farms, the installation marks a significant leap forward from the container-based modules with localized cooling used previously. Food security Kelly Bullivant, Distribution Account Manager at Fujitsu General Air Conditioning, said, “Food security is becoming increasingly important and we are proud to be able to contribute to the development of vertical farming." "Our equipment is ideally suited to the precision needed for an installation of this type.’’
When the Florida Keys Aqueduct Authority opens its upgraded desalination plant on Stock Island, Danfoss high-pressure pumps and energy recovery devices will radically improve the energy efficiency of a SWRO plant that plays a central role in the Florida Keys water supply strategy. The Florida Keys Aqueduct Authority (FKAA) supplies 20 million gallons of potable water per day (75.7k m3/d) to its nearly 80,000 customers in the Florida Keys. While most of the water is normally sourced in aquifers, FKAA also operates two seawater reverse osmosis (SWRO) plants for emergency purposes and as a supplemental supply in periods of high demand. FKAA initiated the SWRO plant upgrade FKAA initiated the upgrade of one of these plants, the Kermit H. Lewin Water Treatment Plant located on Stock Island, to increase its capacity, make it more resilient to hurricanes and rising flood levels, and improve its energy efficiency. Since opening in 1980, not only have guidelines for storm protection of such critical infrastructure changed significantly, so has the potential to save on the energy required by desalination. Designed to withstand future floods and hurricanes With sustained winds above 157 mph, such storms can cause severe damage to everything in their path To improve resiliency to extreme weather events in the low-lying Florida Keys, the entire site and facility have now been upgraded to withstand Category 5 hurricanes, the most dangerous level of tropical storms. With sustained winds above 157 mph (252 kph), such storms can cause severe damage to everything in their path. Accordingly, the refurbished facility lifts all electrical and mechanical equipment above the base flood elevation and the expected sea-level rise anticipated by 2060, effectively placing the plant’s desalination operations on stilts to mitigate the risk of severe flooding. improve the plant’s energy efficiency Another key goal of the upgrade was to improve the plant’s energy efficiency at the same time as doubling its production capacity from 2 MGD (7,500 m3/d) to 4 MGD (15,000 m3/d). To bring the refurbished plant up to date and reduce its financial and environmental costs, Carollo, a major U.S. engineering firm specializing in water and wastewater facilities, specified the latest axial-piston high-pressure pumps to replace legacy centrifugal pumps and swapped out old turbines for the newest active isobaric energy recovery technology. Upgraded plant to consist of four RO trains This innovative high-pressure setup dramatically reduces the plant’s energy needs This innovative high-pressure setup dramatically reduces the plant’s energy needs. In the new Kermit H. Lewin Water Treatment Plant being built by Biwater, a world pioneer in water treatment, the RO process-specific energy consumption will be slashed from 25.6 kW/kgal (6.77 kWh/m3) to 8.6 kW/kgal (2.27 kWh/m3). With this improvement, the new plant will be among the most energy-efficient in its class, with significantly reduced electricity bills and greenhouse gas emissions. The upgraded plant will consist of four RO trains, each of which includes two Danfoss APP 86 high-pressure pumps and three Danfoss iSave 70 ERDs. Improvement in energy efficiency In addition to the dramatic improvement in energy efficiency, configuring each train with parallel high-pressure pumps provides additional resilience and other benefits: the smaller pumps are easier to lift and work on, and it is now affordable to keep a spare pump in stock. The new improved plant will come online in Q4 2024. The new Kermit H. Lewin Water Treatment Plant is located just north of the existing plant. Construction began in Q3 2021 and will be completed by Q2 2024. The plant is expected to be fully operational by Q4 2024.
Convoy of Hope is an international nonprofit based in Springfield, Missouri. Founded in 1994 by Hal Donaldson, the humanitarian organization strives to feed the world and end intergenerational poverty. Programs include training and equipping local farmers to create food security, feeding more than 533,000 children every school day worldwide, U.S. and international disaster response, and empowering women as entrepreneurs and in the workforce. Since its founding, Convoy of Hope has served more than 250 million people and provided more than $2.5 billion worth of supplies to those in need. tackling global priorities In 2021, Convoy of Hope’s leadership decided that building a new headquarters and training center would improve the organization’s ability to serve humanity. For the first time in its nearly 30-year existence, Convoy of Hope would bring staff together on one campus to tackle its global priorities. The new facility would be a point of pride in Springfield and connect team members in an inviting and comfortable setting. culture of the humanitarian organization The building would reflect the culture of the humanitarian organization and demonstrate good stewardship Additionally, the building would reflect the culture of the humanitarian organization and demonstrate good stewardship of financial resources. “We’re a non-profit organization, so we don’t want to spend more than we need to. We need to be able to take care of the heating and cooling needs in a way that’s efficient and cost-effective," said Ethan Forhetz, Vice President of Public Engagement, at Convoy of Hope. Project highlights Convoy of Hope’s headquarters is a 200,000-square-foot, modern, industrial-styled, open-concept, multi-use facility. The building houses a large atrium, auditorium, cafeteria, dining room, kitchen, open office spaces, and private offices. More than 280 of the organization’s 500-plus total employees work at the facility daily. The project team, assembled in 2021, collaborated from the design phase through the grand opening in 2023. Installation and project management Buxton Kubik Dodd, Inc., a full-service design firm in Springfield, did the architectural design, interior design, and mechanical engineering. Knight Heating & Air Conditioning, a local, family-owned HVAC contractor, did the installation and project management with support from Fields Mechanical Systems, a local LG-applied representative firm. “We try to recommend a product to the customer that has good local representation. It usually boils down to who supports a product the best. So that’s why we recommended LG,” said Chris Knight, Vice President, of Knight Heating and Air Conditioning. Challenges The heating and cooling system would need to satisfy diverse comfort requirements simultaneously Load diversity was the project team’s most significant challenge. Comfort requirements in the multi-use building vary by each space’s purpose, solar orientation, time of day, glazing, and whether the space is on the perimeter or interior. Southwest-facing offices have different heating and cooling needs than similar offices on the northeast side, as does the large, wide-open atrium versus the kitchen. On cold days when most of the building requires heating, some spaces still require cooling due to the facility’s glass frontage. The heating and cooling system would need to satisfy diverse comfort requirements simultaneously throughout the seasons, as Missouri’s weather ranged from intense heat to extreme cold. Acoustics, mechanical systems and designs The project team also considered acoustics while evaluating mechanical systems and designs. Convoy of Hope’s headquarters embraces an industrial aesthetic, which includes hard floors and concrete, exposed ceilings. With large, open spaces and few surfaces to absorb noise, a noisy HVAC system would disturb employees and reduce each space’s usability. The heating and cooling solution needed to operate quietly and fit in aesthetically. Concealing the HVAC equipment Given the facility’s size and profile in the community, Convoy of Hope tasked the project team with concealing the HVAC equipment so that it did not detract from the exterior appearance of the building. Thousands of cars pass the facility daily. The team rejected mechanical options that would have required extensive ductwork and equipment sitting in full view on the building’s lower roofs. Comfortable and seamless While hiding the equipment posed an engineering challenge, Convoy of Hope prioritized the building’s beauty While hiding the equipment posed an engineering challenge, Convoy of Hope prioritized the building’s beauty as part of being a good neighbor. “The ability to handle varying loads comfortably and seamlessly was the main goal of the project,” said Dylan Chorice, Principal Engineer, Buxton Kubik Dodd, Inc. Solution The project team decided that a variable refrigerant flow (VRF) system with heat recovery from LG would be the best and most cost-effective solution to meeting Convoy of Hope’s needs. “Early in the process, we knew LG was the partner we wanted to work with,” said Dylan Chorice, Principal Engineer, Buxton Kubik Dodd, Inc. Multi V 5 system LG’s Multi V 5 system uses comprehensive controls and outdoor units with inverters to vary compressor speeds and heating and cooling capacity based on occupant comfort needs and ambient conditions. Every outdoor unit connects to multiple indoor units, each serving a zone within the building. With LG’s inverter technology, the all-electric system uses minimal energy to move heat out of zones requiring cooling and transfer heat to zones that need heating. “What LG does for us here is allow us to meet the unique needs of our building’s individual spaces,” said Ethan Forhetz, VP of Public Engagement, at Convoy of Hope. Heat-recovery unit VRF systems typically reject indoor heat to the outdoors during cooling and operate in one mode at a time The project team specified an LG Multi V 5 system with a heat-recovery unit to solve Convoy of Hope’s load diversity challenge with simultaneous heating and cooling. VRF systems typically reject indoor heat to the outdoors during cooling and operate in one mode at a time: heating or cooling. Adding a heat-recovery unit enables LG’s VRF system to transfer heat from zones in cooling mode and simultaneously use it to warm zones in heating mode. Increased efficiency and cost savings By repurposing heat instead of rejecting it, a VRF system with heat recovery increases efficiency and cost savings while keeping diverse spaces comfortable. For example, the Multi V 5 can cool Convoy of Hope’ssouthwest-facing offices and account for solar gain while using that heat to warm the building’s cooler opposite side. The technology also allows Convoy of Hope to customize setpoints for each zone based on individual and administrator preferences. Powered by the Niagara 4 Framework®, LG’sMultiSITE VM3 controls empower facility managers to visualize, monitor, and control the entire VRF system. Mid-static ducted units The project team installed mid-static ducted units in the areas with covered ceilings. In the open office spaces with exposed high ceilings, the project team installed LG’s DUAL Vane 4-way cassettes. The cassettes cover wide spaces and contribute to healthier air with a five-step filtration and purification kit. To better match the space’s aesthetic requirements, the team placed shrouds on the cassettes, giving the units a cloud-like look that fits seamlessly into the design. Compact refrigerant lines Multi V 5 solution supported Convoy of Hope’s aesthetic needs and reduce costs by requiring less ductwork The Multi V 5 solution also supported Convoy of Hope’s aesthetic needs and reduced costs by requiring less ductwork than alternative systems.LG’s VRF system runs very quietly. Convoy of Hope team members can focus on their work without complaints about comfort or mechanical noise. The Multi V 5’s long, compact refrigerant lines enabled the project team to tackle the facility’s exterior design challenges. VRF outdoor units By installing the VRF outdoor units on the third floor’s roof, the project team kept the system out of sight to pass neighbors or people entering the parking lot. The refrigerant lines run from the upper roof and down the sides of the buildings to serve the lower floors without requiring units on the ground or the lower roofs. Result Convoy of Hope is currently listed among the top 50 organizations in the Forbes list of America’s Top 100 Charities. With its new headquarters and training center, the organization is positioned to continue and grow its humanitarian work. “It’s a brand-new building. It’s a big building. But it felt very homey right off the bat. I think a large part of that is because it’s very comfortable,” said Ethan Forhetz, VP of Public Engagement, at Convoy of Hope. Cost-effective operation LG’s Multi V 5 VRF system with heat recovery satisfies Convoy of Hope's requirements LG’s Multi V 5 VRF system with heat recovery satisfies Convoy of Hope's requirements across comfort, efficiency, acoustics, and aesthetics. The facility is a community showpiece that helps the organization keep faith with its financial supporters through cost-effective operation. “Convoy of Hope plans to be here for a very long time, so every dollar we can save on utility bills is another dollar they can put toward their mission, which is critically important,” said Dylan Chorice, Principal Engineer, Buxton Kubik Dodd, Inc. LG HVAC Products Multi V 5 (20 - 40 Ton) MultiSITE VM3 DUAL Vane 4way Cassettes Ceiling Concealed Duct Unit (Mid-Static)
With 53 men on the Jacksonville Jaguars roster, practicing 5 to 6 days per week for 10 to 12 hours a day, the demand for hot water must be enormous. As the choice for the team’s practice facility’s hot water storage and water heating capabilities, we happen to have the deets. How about 1,880 gallons of storage capacity and 2,400,000 btu/hr heating the water? Miller Electric Center The Miller Electric Center is a new state-of-the-art practice facility in downtown Jacksonville that serves as the Jaguars’ football operations headquarters. The 120 million dollar facility is 125,000 square feet and includes locker rooms, training and medical facilities, office space, and a draft room. It also features two full-size grass practice fields and one indoor field, along with shaded public viewing stands, concession areas, and a team store. Big men need big spaces Armor’s SMART TOUCH operating control makes adjusting parameters and troubleshooting a breeze Luckily, Lochinvar’s Armor Condensing water heaters are up for the job. The Armor’s stainless steel heat exchanger delivers hot water at 98% thermal efficiency and modulates at a 10:1 turndown ratio. That means the units can fire as low as 10% of their total capability and modulate up to 100% when the demand is greatest. The Jag’s facility has 3 of the AWH0800NPM units installed providing the ability to cascade which ensures the units operate with equal runtime and extends the life of the heaters. The Armor’s SMART TOUCH operating control makes adjusting parameters and troubleshooting a breeze – which is nice in Florida. Lock-Temp Round Jacketed Storage Tank With a proven storage vessel like the Lock-Temp Round Jacketed Storage Tank, making sure the stored hot water is ready for delivery is a given. These tanks have the exclusive Lock-Temp baffle that keeps water evenly stratified and the 80% draw factor allows almost the entire capacity to be used at the designated temperature. installation and commission With the help of a local manufacturers’ rep firm, Harry Warren, the installing contractor, Touchton Plumbing out of Jacksonville reported that the whole experience went off without a hitch. “The installation went extremely well, and the units have been working without fail through the first year of the facility being in use,” said Parker Touchton, project manager. The equipment was installed and commissioned according to schedule and is said to be performing as promised and at the end of a 12-hour practice, there’s no room for disappointment.
To offset the cost of tenants’ monthly electric bills and provide prospective residents with high-quality HVAC upgrades that prioritize comfort and performance, Samuels Associates, owner of the Fenway Triangle luxury apartments, sought a new, building-wide heating solution that was not only cost-effective but also added a modern touch to the building’s extravagance. QMark® MUH-Pro+ and CU900 electric heaters with SmartSeries® Plus (SSP) digital BACnet thermostats from Goodyear HVAC Sales proved to be the ideal solution. Heat in a contemporary design “From their energy efficiency, quiet operation and low maintenance to the fact that they can be controlled individually for personalized comfort, electric heaters offer several benefits in apartment buildings,” explained Andrew Martin, Manager of Product Management with Marley Engineered Products® (MEP). “Delivering supplemental comfort heat in a contemporary design, these heaters are ideal for a variety of spaces including school hallways, church vestibules, transportation terminals, stairwells, entrances, lobbies, mechanical rooms and more.” Installing Heaters while Maintaining esthetics Buildings boast modern frills and discreet and esthetically good HVAC plans that act quietly Steps away from the iconic Fenway Park, the Fenway Triangle is an 891,000-square-foot complex comprising more than 570 luxury apartment units, as well as an eclectic mix of national and local retailers, restaurants, shops and green spaces. Since opening in 2006, the building needed to address issues with its HVAC systems and controls, which were leading to high monthly electric bills. The culprit? More than 50 outdated competitor electric terminal heaters, which offered only on/off controls and needed to be operated manually. If the maintenance team forgot to shut off the heaters, "The Fenway" would incur the cost of each heater running at full capacity at a rate of about 27 cents per kilowatt-hour. Another challenge facing Fenway Triangle: The emergence of new luxury apartment complexes. These buildings boast modern amenities and discreet and esthetically pleasing HVAC systems that operate quietly. They pose significant competition for “The Fenway”, as tenants increasingly prioritize indoor air quality (IAQ) and HVAC performance when selecting their luxury residences. To remain competitive in the luxury apartment market, investing in HVAC upgrades to replace outdated equipment is imperative. QMark MUH-Pro+ and CU900 electric heaters Heaters were installed in elevator banks, stairwells, worker lounges, hallways, and facility To combat the rising cost of heating each unit within the building, MEP’s local Sales Representative, Goodyear HVAC Sales, worked with HVAC distributor Equipment Direct Sales, Inc. (EDSI) to provide the client with energy-efficient QMark MUH-Pro+ and CU900 electric heaters from Marley Engineered Products. Designed to maintain occupant comfort and a comfortable environment, the heaters were installed in various elevator banks, stairwells, employee lounges, hallways and inside the building’s recently upgraded building management system (BMS) room. “Equipped with SSP digital thermostats that provide connections to BACnet MS/TP BMS for easy control and monitoring, the MUH-Pro+ and CU900 units only run when directed by the internal schedule of the BMS,” said Matthew Goodrich, President of Goodyear HVAC Sales. “Use of the BMS saves time and reduces personnel costs by eliminating the need to travel to the heater site. And, if a BMS is not available, the maintenance team can simply use the built in seven-day programmable scheduling feature.” New electric heating units Cost-Effective Heat for Unmatched Comfort and Lower Monthly Bills In tandem with EDSI, Goodrich and his team installed several brand-new electric heating units in The Fenway’s BMS room to provide cost-effective warmth without taking up floor space or creating a tripping hazard. “Innovation and collaboration converged as we tailored a custom heating solution, seamlessly blending functionality and aesthetics,” explained Goodrich. “In fabricating this solution for the client, our dedicated team and the coordination of skilled contractors transformed this building into a space that harmonizes comfort and elegance and exemplifies the blending of form and function.” Full control of the entire heating system The thermostats include features that allow the building’s maintenance team to monitor each heater The success of the project resulted in an extremely satisfied customer. Already, the SSP thermostats have provided cost savings by turning on the heaters only when needed, resulting in less electricity usage throughout The Fenway. Additionally, the thermostats include features that allow the building’s maintenance team to monitor each heater individually from within the BMS room, granting them full control of the entire heating system and eliminating the daily trips previously needed to turn each heater on and off. “We’re already seeing the savings associated with the upgraded controls,” said John Belmonte, Head of Trilogy Operations for the Fenway Triangle. “Being able to control over 40 heaters locally allows our team to focus on tenant needs without being bogged down by the time it takes to touch each individual unit. We’re eager to work further with the Goodyear team on other buildings in the neighborhood.” Innovative approach and exceptional achievements To acknowledge the innovative approach and exceptional achievements demonstrated by the Goodyear team in overcoming the challenges faced during this project, Marley Engineered Products awarded Goodrich the 2024 Jim Herring Memorial Silver Fox Award at its recent national sales meeting. “This award for excellence in solution design embodies the spirit of Herring, who left a lasting legacy of designing creative solutions for specialized applications, was always up for a challenge and most happy when solving a unique heating or ventilation problem,” said Sean Pesce, Director of Sales for Marley Engineered Products. “Matthew and his team at Goodyear perfectly captured Jim’s talent for finding creative solutions to the most complex issues and left a lasting impression on the client.”
To adequately heat the 111 Murray Street residential skyscraper in New York, the owner sought an effective way to maintain the aesthetic of the mostly glass building without being obtrusive to its design. Custom convection style heaters, mounted in the building’s millwork by Faber Industrial Technologies, proved to be the game-changing resolution. “Convection heaters provide warmth and heat to a specific area or room by circulating air and heating it using a highly efficient electric element,” explained Andrew Martin, Manager of Product Management with Marley Engineered Products. He adds, “Designed for quiet, controlled comfort, they are ideal for both residential and commercial applications, including living rooms and bedrooms, offices, hallways, lobbies, conference rooms, retail stores and buildings with floor-to-ceiling windows.” Installing heaters while maintaining aesthetics 111 Murray Street is a 792-foot-tall residential skyscraper with 156 luxury condominiums Located in the Financial District and Tribeca neighborhoods in Lower Manhattan, 111 Murray Street is a 792-foot-tall residential skyscraper with 156 luxury condominiums and 2,100 square feet of retail space on the ground floor. Due to mechanical constraints exacerbated by the building’s slim design, hot water was not available in most of the upper residences, rendering hydronic heating systems impractical. Therefore, the client requested Berko ASL3 convector heaters from Marley Engineered Products to be installed for elegant, supplemental comfort for heat loss, condensation prevention and continuous warmth throughout each condo. The challenge, however, came from their preference to keep the heaters hidden for aesthetic reasons. “The varying heights and angles of the millwork in each condo limited our ability to install the heaters directly where we wanted them,” said Christopher Smith, a Heater Manufacturing Representative with Faber Industrial Technologies, adding “Therefore, we needed a custom design that enabled us to mount the heaters properly while also keeping them out of sight.” Hidden Heat for Unmatched Comfort and Elegance The solution involved fabricating and supplying custom dual inlet convector heaters, which were then mounted within the millwork of each condominium unit. Using a thermocouple array, the engineering team at Marley tested the Berko ASL3 convectors – at 125 watts per foot and 120V – inside a customer-supplied demo millwork section sent from New York City. After making some adjustments to the design, thermal couplers were utilized on both the heaters and their enclosures to ensure their surface temperatures were within Marley Engineered Products’ limits to pass a UL site inspection. Berko ASL3 convector heaters The result was an ‘invisible solution’ in which none of the controls or heaters could be seen in the residential units Next, Smith coordinated with the electrical and mechanical contractors on-site to fit the heaters into each condo’s temperature control system using power relays. The result was an ‘invisible solution’ in which none of the controls or heaters could be seen in the residential units. “Innovation and collaboration converged as we tailored a custom heating solution, seamlessly blending functionality and aesthetics,” explained Christopher Smith, adding “In fabricating this ‘invisible solution’ for the client, our dedicated team and the coordination of skilled contractors transformed these condos into spaces that harmonize comfort and elegance and exemplify the blending of form and function.” Berko ASL3 convector heaters The success of the project not only resulted in an extremely satisfied customer, but also left the contractors pleased with the uninterrupted delivery and installation of the heaters. They were further impressed when the custom heater and millwork system passed the UL site inspector’s test after just one evaluation. To acknowledge the innovative approach and exceptional achievements demonstrated by the Faber team in overcoming the challenges faced during this project, Marley Engineered Products awarded Smith the 2023 Jim Herring Memorial Silver Fox Award at its recent national sales meeting. Solving unique heating or ventilation problems “This award for excellence in solution design embodies the spirit of Herring, who was always up for a challenge and most happy when solving a unique heating or ventilation problem,” said Sean Pesce, Acting Director of Sales for Marley Engineered Products. He adds, “Chris and his team perfectly captured Jim’s talent for finding creative solutions to the most complex issues and left a lasting impression on the client.”


Round table discussion
The HVAC market is a rapidly changing environment on a variety of fronts, from the introduction of new refrigerants to the increasing use of artificial intelligence to the embrace of interconnected systems in the Internet of Things (IoT) environment. We asked our Expert Panel Roundtable: How will the HVAC market change in the next five years?
Some of the technologies in the HVAC market are mature, although the newest innovation is always just around the corner. Newer systems seek to be more sustainable and energy-efficient, and digital control technologies play a role in maximizing their performance. Trends such as the Internet of Things (IoT) and smart systems are the basis for the newest connectivity and control approaches. These innovations tie into the broader environment of smart buildings. Systems are also providing remote access to enable technicians to analyze system operation and troubleshoot any problems. We asked our Expert Panel Roundtable: What's new in connectivity and control systems for HVAC?
For schools, improving indoor air quality (IAQ) is a basic function of HVAC systems, which also ensures a high comfort level for students, teachers and staff. Schools can be a lucrative market for HVAC systems, but there are challenges, such as long sales cycles and the lingering impact of the COVID-19 pandemic. We asked our Expert Panel Roundtable: What are the challenges for HVAC in serving the education/schools market?
Products


Videos

From A To L: Your A2L Transition Guide
Download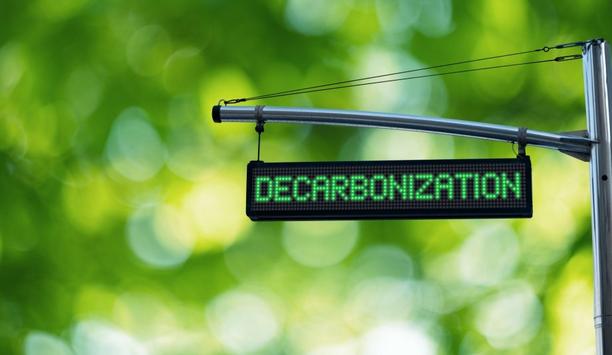
Leveraging Radiant And Hydronics To Help Achieve Decarbonization Goals
Download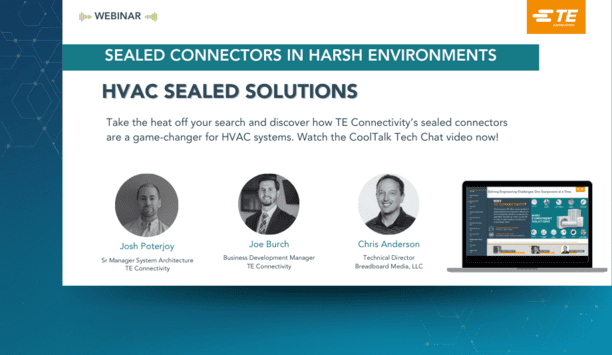
Sealed Connectors In Harsh Environments
Download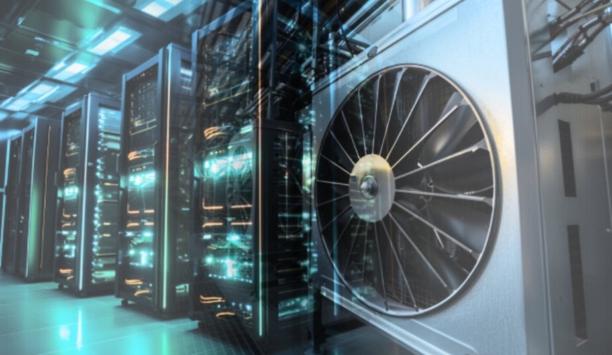
Powering And Cooling Next Generation Data Centers
Download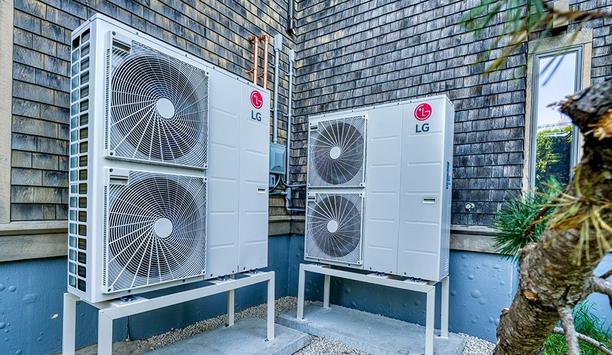
Debunking Myths To Promote A Bright Future For Heat Pumps
Download